Case Study #1935| GANTRY
PIN PRESS APPLICATION
CHALLENGE
In the heavy truck industry, a customer faced a complex challenge involving the pressing of multiple pins into a turbocharger at varying heights and locations using just one actuator. The difficulty lay in finding technologies that could seamlessly integrate to provide precise accuracy, location flexibility, and the necessary force to press the pins. Additionally, the customer aimed to avoid the inefficiency of handling the part multiple times and repositioning it manually.
To achieve this, the customer needed a solution that could synchronize different technologies to ensure each pin was pressed accurately and at the correct location. Furthermore, it was imperative that the system collected force and position data for each pin press. This data was essential for quality control and ensuring that the pins were pressed with the right amount of force at the precise positions, maintaining the integrity and performance of the turbocharger.
Overall, the customer required a highly integrated and automated system that could handle the complexity of pressing multiple pins at different heights and locations while providing accurate data and minimizing manual intervention.
SOLUTION
In order to avoid the custom science project approach, our solution was the Promess Gantry paired with a 20kN EMAP press. The Promess UltraPRO controller was used as the control platform to support each axis. This allowed one common software and controller to be used, which resulted in a simple, seamless solution that the customer could easily understand and support.
The Gantry matched with the 20kN EMAP allowed for precise X, Y and Z motion control and up to 20kN’s of precision force control. In addition, these are standard product offerings from Promess, so no real customization was required, resulting in a simple and fast integration.
Results
With this fully programmable multi-axis solution, the customer was able to press multiple pins into a turbo charger without physically removing the product from the table. The precise control and programmability allowed all the pins to be pressed individually to their required specification, fast and accurately. The force/position data from each part was useful in determining the quality of the product each time.
This solution proved to be a faster process for the customer, simplified the process by adding simple automation and gave them the quality assurance that each part would be made identical to the next with data to prove it.
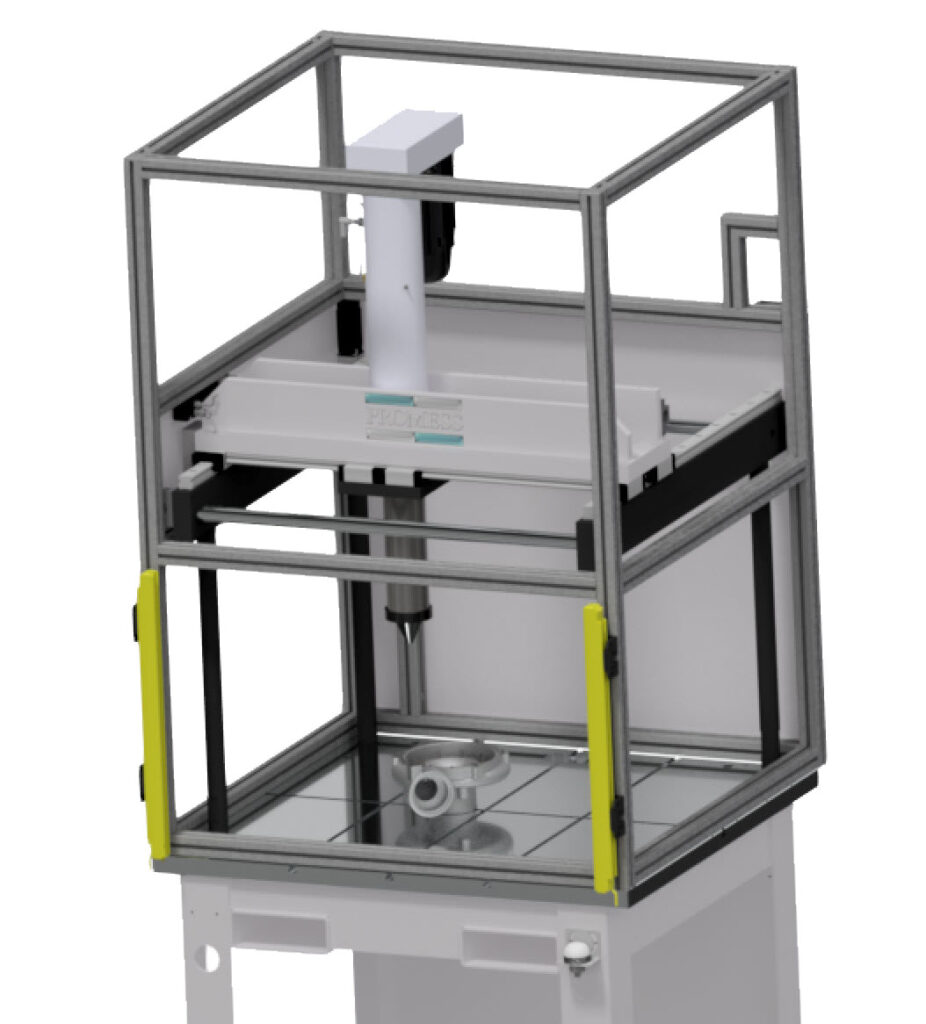