Case Study #1855 | EMAP
Improving Quality & Traceability in Vascular Closure Device Assembly
Challenge
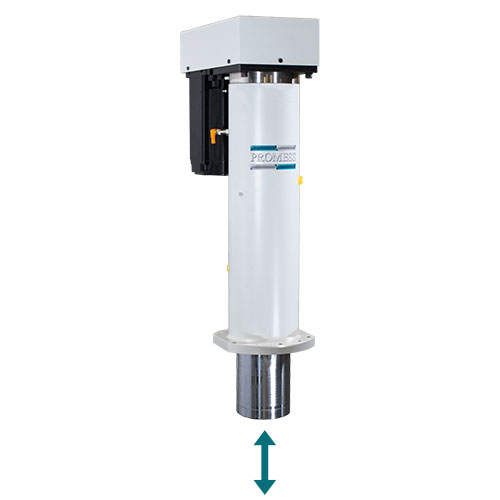
A medical equipment manufacturer faced intermittent product failures in the field due to an inadequate assembly process for vascular closure devices. The original method relied on manual installation of the release mechanism and seal, followed by an air-actuated press to join the body halves. A torque test was performed afterward to verify assembly. However, lack of process monitoring and traceability led to failures, including:
- Misassembled release mechanisms, impacting device functionality.
- Improperly installed seals, preventing proper joining of body halves.
- Undetected failures progressing through production, increasing rework and inspection costs.
With no real-time monitoring, the manufacturer had to rely on costly end-of-line batch checking, leading to inefficiencies and potential risks in the field.
SOLUTION
To address these challenges, Promess provided an Electro-Mechanical Assembly Press (EMAP) with integrated force vs. position monitoring and a TorquePRO system for functional testing of the final assembly.
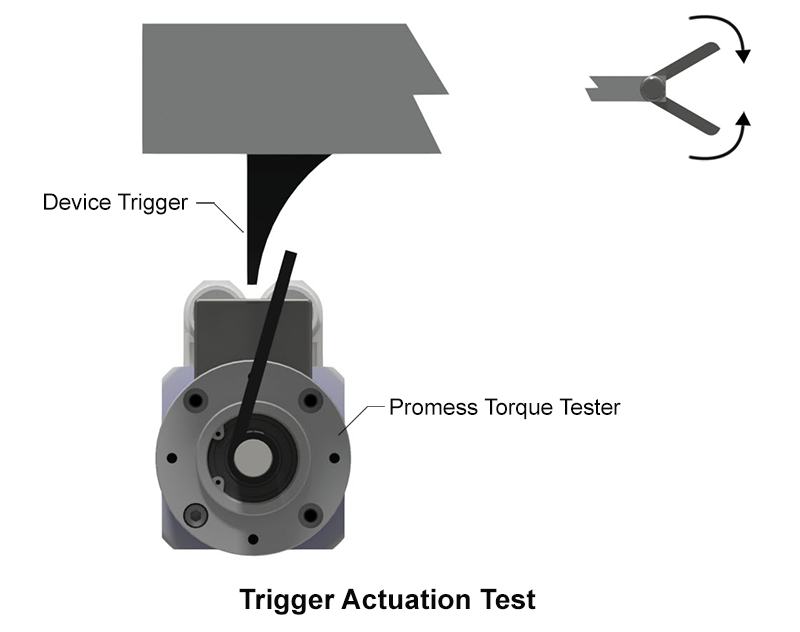
- Consistent Assembly Forces: Promess application engineers determined the optimal force requirements for assembling the housing. The EMAP press ensured repeatable force application within ±0.5%, eliminating variability in assembly.
- Functional Testing with TorquePRO: By implementing a torque test on every unit, the manufacturer could verify the proper function of the release mechanism before the device moved forward in production.
- 100% In-Process Verification & Traceability: With real-time monitoring, failures were caught immediately, eliminating the need for batch testing and reducing rework costs.
RESULTS
The implementation of Promess solutions resulted in dramatic improvements for the manufacturer:
✅ Eliminated manual variability, ensuring consistent assembly quality.
✅ Prevented defective assemblies from moving down the production line.
✅ Eliminated end-of-line batch checking, reducing waste and rework costs.
✅ Provided full traceability, ensuring each part met quality standards.
By integrating real-time monitoring and precision control, the manufacturer significantly improved product reliability, reduced costs, and achieved higher customer confidence in their medical devices.
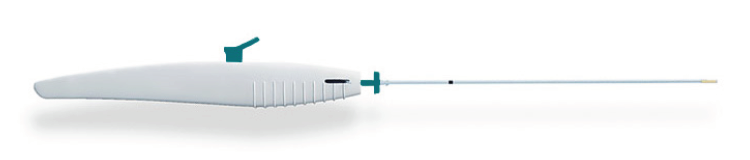