In the world of precision manufacturing, ensuring that every component meets strict quality standards is paramount. For one manufacturer of precision bearings, maintaining the perfect preload was a critical aspect of their quality assurance process. This post explores how they overcame challenges in their quality testing procedure and significantly improved their production line using advanced torque testing technology.
The Challenge: Ensuring Accurate Bearing Preload
Precision bearings are essential in many industries, from automotive to aerospace, where reliability and performance are non-negotiable. A key factor in the performance of these bearings is the preload, which must be accurately set to ensure optimal functionality and longevity.
The manufacturer faced significant challenges with their existing system, which measured the breakaway and running torque of each bearing to determine the preload. The system failed to provide consistent and repeatable results, leading to quality control issues and the potential for defective bearings reaching customers. Furthermore, any new solution had to fit seamlessly into the existing assembly line, handle a torque range up to 1,000 gm/cm, and connect to the plant’s network for data acquisition and analysis.
The Solution: Implementing the TorquePRO System
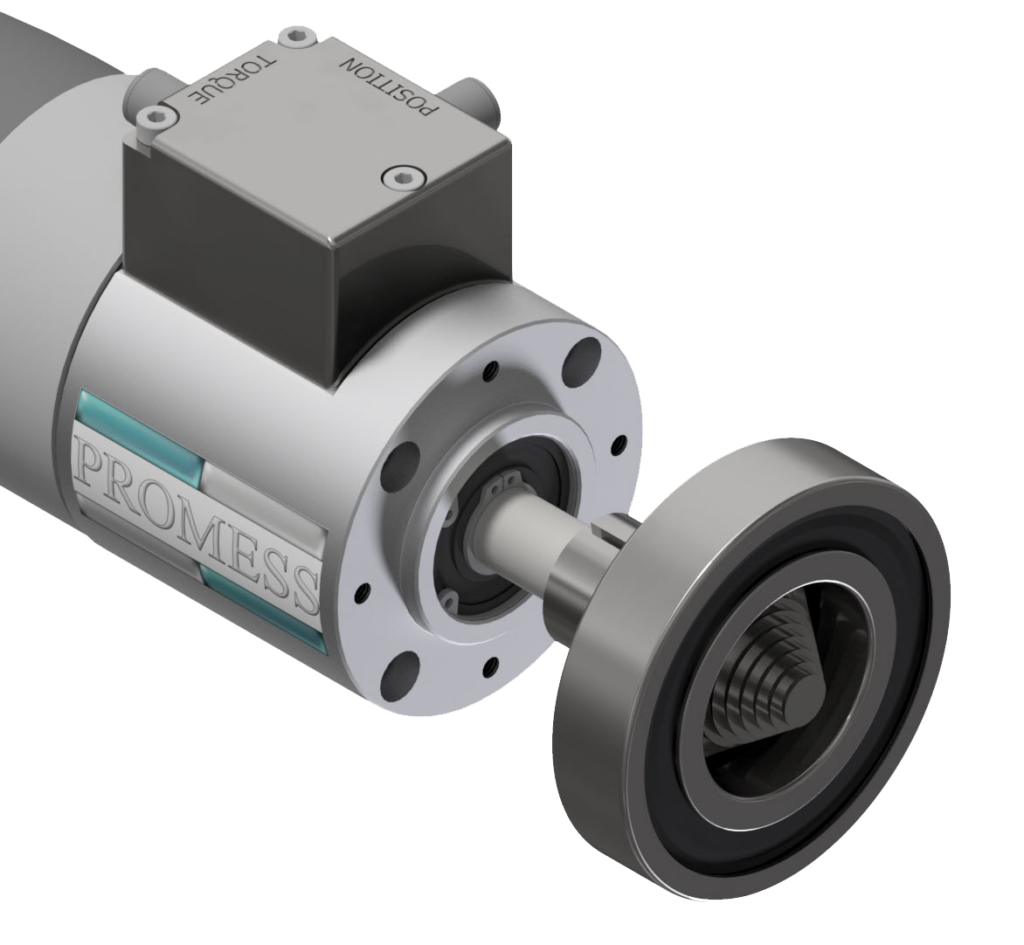
To address these issues, the manufacturer turned to the TorquePRO system from Promess. This integrated system offered both torque monitoring and motion control via a servo motor, providing the stability, repeatability, and flexibility needed to meet the demanding requirements of precision bearing testing.
Key Features of the TorquePRO System:
- Breakaway Torque Measurement: The TorquePRO system measured the initial torque required to start the rotation of the bearing’s inner race while holding the outer race stationary. This measurement is crucial for determining the correct preload.
- Running Torque Measurement: It also measured the torque needed to maintain rotation, providing insights into the bearing’s performance under operational conditions.
- Data Acquisition and Analysis: All torque measurements were recorded and stored, allowing for detailed analysis and quality tracking over time.
- Integration with Existing Systems: The system was easily retrofitted into the existing assembly line, connecting seamlessly to the plant network for real-time data acquisition and communication with the PLC.
How It Works:
The TorquePRO system performs two essential quality checks on each bearing:
- Breakaway Torque Check: This check determines the torque required to initiate movement, which is vital for setting the correct preload.
- Running Torque Check: This ensures that the bearing runs smoothly and within specified torque limits once movement has started.
If any bearing’s torque measurements fall outside the predefined limits, the system sends a fail signal to the PLC, triggering an automatic rejection of the defective part. This closed-loop control process ensures that only bearings meeting the high-quality standards are approved for shipping.
The Results: Improved Quality and Efficiency
The introduction of the TorquePRO system revolutionized the manufacturer’s quality control process for precision bearings. Here’s how:
- Enhanced Quality Control: With consistent and accurate torque measurements, the manufacturer could ensure that each bearing met the strict preload specifications, significantly reducing the risk of defects and ensuring high product reliability.
- Increased Operational Efficiency: The system’s seamless integration into the existing assembly line minimized disruption, eliminated inconsistencies, and reduced downtime, leading to a more efficient production process.
- Comprehensive Data Insights: The ability to store and analyze torque data allowed the manufacturer to monitor quality trends over time and make informed decisions to continuously improve their process.
- Automated Defect Rejection: The automated fail signal system ensured immediate rejection of any bearing not meeting the torque requirements, maintaining high standards of quality without manual intervention.
A Commitment to Quality and Innovation
This case study highlights the transformative impact of the TorquePRO system on the precision bearing manufacturing process. By providing accurate and repeatable torque measurements and seamless integration with existing systems, the TorquePRO system enabled the manufacturer to achieve superior quality control and operational efficiency. This investment in advanced torque testing technology not only resolved existing challenges but also positioned the company for future success in a competitive market.
For manufacturers facing similar quality assurance challenges, investing in precise and reliable testing systems like TorquePRO can make a significant difference in maintaining high product standards and enhancing overall process efficiency. As this case demonstrates, the right technology can be a game-changer in the pursuit of manufacturing excellence.