In the highly demanding world of automotive manufacturing, the quality and reliability of each component are paramount. For a manufacturer producing spare tire carrier assemblies for trucks and vans, ensuring the perfect functionality of these assemblies is critical. The spare tire carrier’s role in lifting, lowering, and securely holding the spare tire makes it a vital component for vehicle safety and performance. This case study explores how advanced torque testing technology was implemented to overcome significant quality control challenges and enhance the manufacturing process for these assemblies.
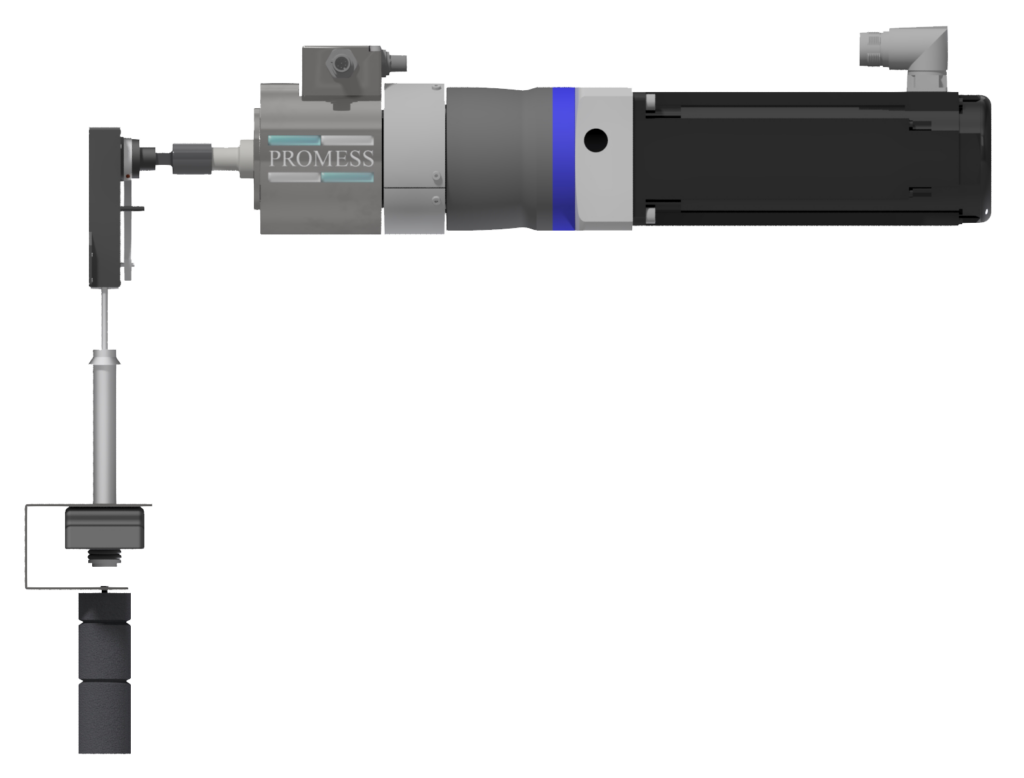
The Challenge: Ensuring Precise Torque and Force in Spare Tire Carriers
Spare tire carriers must undergo rigorous testing to confirm they can reliably handle the weight and movement of a tire. The key challenge was to accurately measure and gauge the peak torque required to operate the lift mechanism and ensure it met the stringent product specifications. The process also needed to measure the force applied to the carrier cable and set the cable length to 800 mm, the required position for shipping. The existing system struggled with these requirements, lacking the ability to provide consistent and repeatable results. Moreover, it was essential to integrate a solution that could fit seamlessly into the existing assembly line and connect to the plant’s network for comprehensive data acquisition and traceability.
The Solution: Integrating the TorquePRO System
To tackle these challenges, the manufacturer turned to the TorquePRO system from Promess. This advanced system was chosen for its ability to deliver precise torque monitoring and motion control, meeting the demanding requirements of the spare tire carrier assembly process.
Key Features and Process Integration:
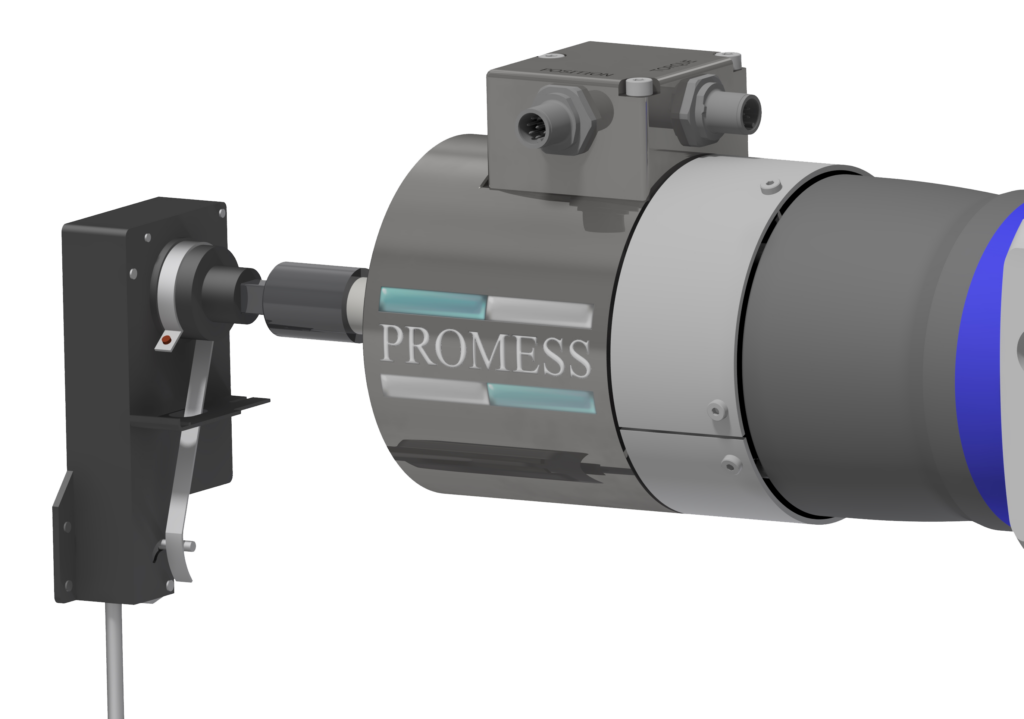
- Precise Torque Measurement:
- Initial Torque Application: The TorquePRO system begins by winding up the carrier cable until it reaches a torque of 20 Nm. At this point, the tire support contacts a fixed stop on the testing machine.
- Peak Torque Gauging: The system then rotates the cable an additional three revolutions. During this movement, the TorquePRO system, equipped with the Promess Motion Controller, captures detailed torque data and determines the peak torque. This ensures that each assembly meets the required torque specifications for optimal performance.
- Cable Length Setting:
- The system accurately sets the cable length to 800 mm, ensuring that the spare tire carrier is ready for installation and meets shipping requirements.
- Force Measurement with External Load Cell:
- The Promess Motion Controller monitors an external load cell within the testing fixture. This load cell measures the “tire squash,” indicating the tension applied to the carrier cable, a critical factor in confirming that the carrier can handle the specified load.
- The system records the peak force data from the load cell, ensuring that the force applied is within acceptable limits.
- Comprehensive Data Acquisition:
- All measurements, including torque and force values, are stored in a data file for each test. This data is crucial for part traceability and allows for detailed analysis of the manufacturing process to ensure continuous quality improvement and problem resolution.
The Results: Enhanced Quality and Efficiency
The integration of the TorquePRO system transformed the manufacturer’s quality control process for spare tire carrier assemblies. Here are the key benefits realized from this implementation:
Improved Quality Assurance:
The system’s accurate measurement and monitoring of peak torque and force ensured that every assembly met strict product specifications. This enhanced quality control significantly reduced the likelihood of defective products reaching customers, thereby improving overall reliability and safety.
Increased Process Efficiency:
The plug-and-play design of the TorquePRO system enabled quick and seamless integration into the existing assembly line. This minimized downtime and allowed for a smoother, more efficient production process.
Reliable Data Collection and Analysis:
The automated data acquisition provided detailed traceability for each tested assembly, which was invaluable for tracking product quality and identifying areas for process improvement. This comprehensive data collection enabled the manufacturer to maintain high standards and continually refine their manufacturing process.
Reduced Defect Rate:
The system’s ability to detect assemblies that did not meet torque and force specifications led to a significant reduction in the defect rate. This ensured that only compliant products progressed in the production line, improving overall product quality and customer satisfaction.
Seamless Integration:
The TorquePRO system’s ability to set the cable length and measure critical parameters without major modifications to the existing setup made it a highly effective solution, enhancing the flexibility and adaptability of the manufacturing process.
A Commitment to Quality and Innovation
This case study highlights the transformative impact of the TorquePRO system on the spare tire carrier assembly process. By providing precise torque and force measurements and integrating seamlessly into the existing production line, the TorquePRO system significantly enhanced the manufacturer’s quality control capabilities and operational efficiency. This investment in advanced torque testing technology not only resolved existing challenges but also paved the way for future success in the competitive automotive market.
For manufacturers facing similar quality assurance challenges, adopting advanced torque testing solutions like the TorquePRO can lead to significant improvements in product quality and process efficiency. As this case demonstrates, the right technology can make a profound difference in achieving and maintaining high standards in manufacturing.