Case Study #1880 | TorquePRO
Spare Tire Carrier Assembly Testing
Challenge:
Verifying torque and force specifications in spare tire carrier assembly
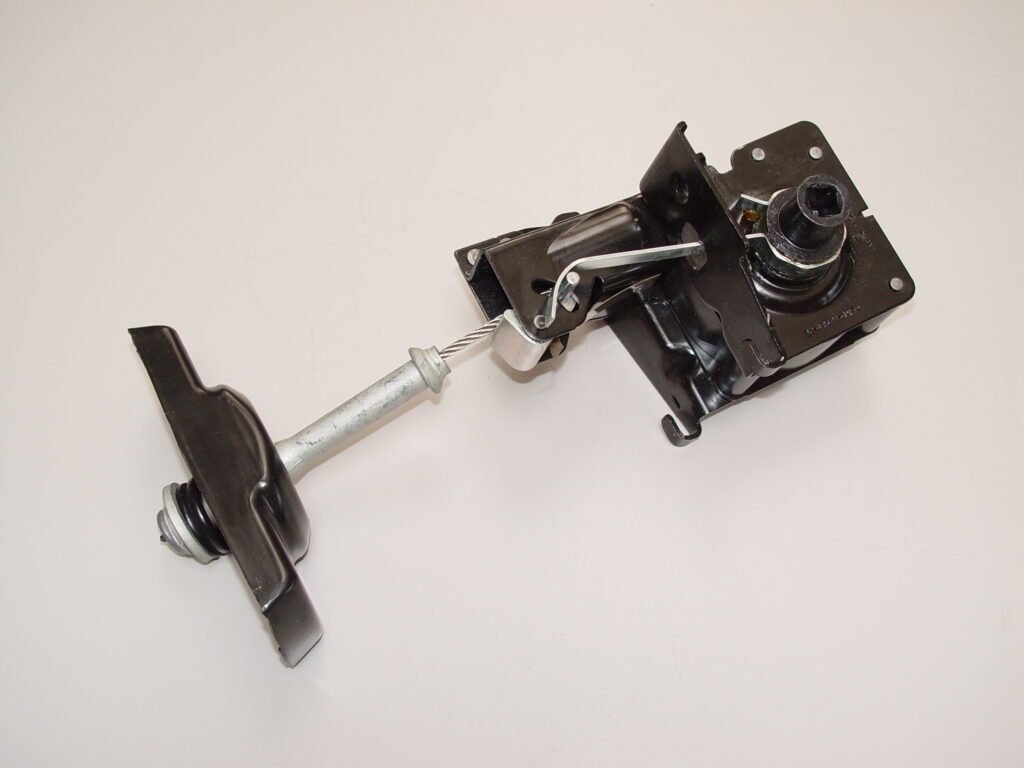
A leading truck and van manufacturer required a reliable end-of-line functional test for its Spare Tire Carrier Assembly, a critical component responsible for lifting, lowering, and securing the spare tire on the vehicle. The primary challenge was ensuring that the lift mechanism met stringent torque specifications while maintaining precise control over cable length and external load forces.
Application Requirements
To meet production and quality standards, the testing system needed to:
- Operate within a torque range of 50Nm
- Measure and gauge peak torque per product specifications
- Set the cable length to 800mm (shipping position)
- Measure and gauge force using an external load cell
- Enable data acquisition for part traceability
- Provide a plug-and-play torque monitoring system
Solution: TorquePRO System Integration
The Promess TorquePRO system was selected for its ability to handle both motion control and real-time monitoring of torque and force throughout the functional testing process.
- Controlled Torque Application: The process begins with the TorquePRO winding the carrier cable until it reaches 20Nm of torque. At this point, the tire support at the end of the cable makes contact with a fixed stop on the machine.
- Peak Torque Measurement: The TorquePRO then rotates an additional three revolutions, during which the Promess Motion Controller acquires and analyzes torque data. The system evaluates the peak torque, and if it exceeds process limits, the part is automatically rejected.
- Force Monitoring via Load Cell: An external load cell, integrated within the fixture, monitors a characteristic known as tire squash, ensuring that sufficient tension is applied to the carrier cable. The system measures and gauges the peak force from the acquired data.
- Data Acquisition for Traceability: All torque and force values are recorded and stored after each test, allowing for comprehensive process analysis and part traceability.
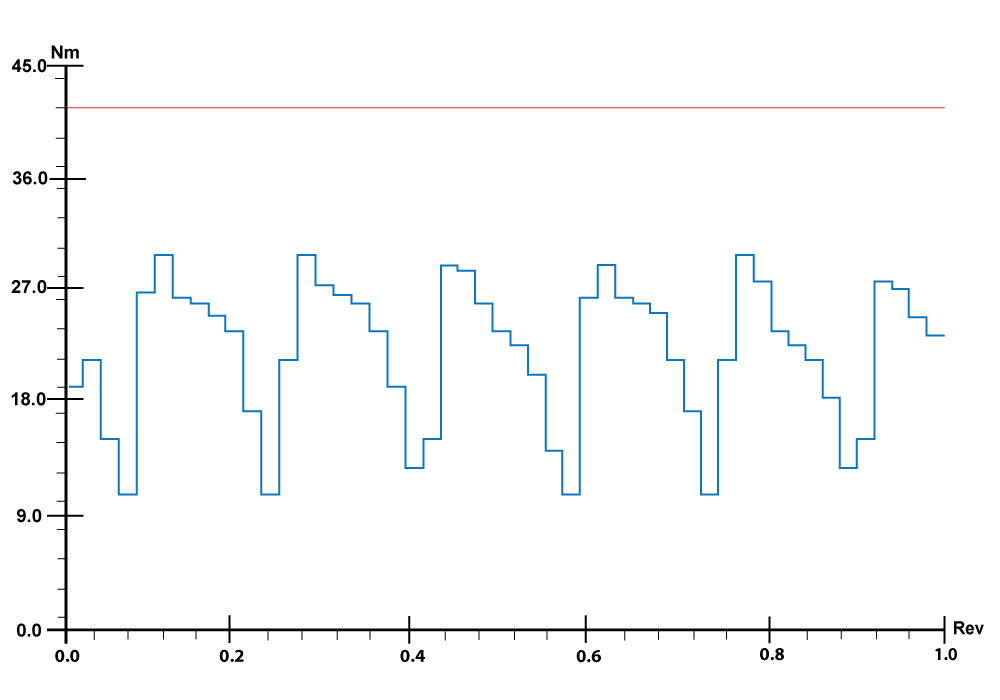
Results & Benefits
By implementing the Promess TorquePRO system, the manufacturer achieved:
- Enhanced Quality Control: Precise measurement and monitoring ensured that all assemblies met stringent torque and force specifications.
- Automated Rejection of Faulty Parts: The system’s ability to gauge peak torque and force in real time reduced defects and improved overall reliability.
- Increased Efficiency: The plug-and-play design streamlined integration into existing production lines, minimizing downtime.
- Comprehensive Data Tracking: Storing test data enabled long-term process optimization and compliance with quality standards.
Through the integration of Promess TorquePRO and Motion Controller, the manufacturer successfully optimized its end-of-line testing process for Spare Tire Carrier Assembly.