Case Study #1650 | EMAP
Precision Crimping in Catheter Assembly with Promess EMAP
CHALLENGE
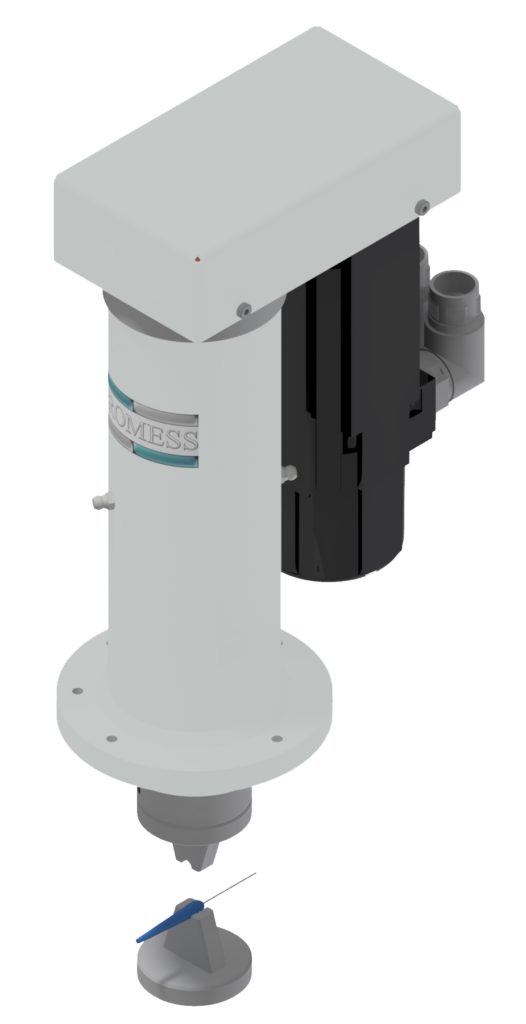
In the medical device industry, precision and reliability are critical—even minor defects can compromise patient safety. A medical equipment manufacturer faced significant challenges in their catheter assembly process, struggling to achieve consistent quality in a crucial crimping operation.
The process involved crimping a small inner-diameter (ID) metal tube inside a larger ID tube, ensuring proper fluid passage. However, they encountered two major issues:
- Loose Crimps: Causing the catheter to pull apart
- Tight Crimps: Blocking the fluid passage
The root cause was the hydraulic press used in production, which lacked precision force control. An external load cell failed to provide the necessary accuracy, leaving the manufacturer in urgent need of a more reliable and repeatable solution.
SOLUTION
Promess provided its Electro-Mechanical Assembly Press (EMAP) to address these challenges. Promess Application Engineers first determined the optimal forces required to achieve the perfect crimp. The EMAP, with its precision control, allowed the manufacturer to press to the exact force (+0.5%) consistently. Additionally, the closed-loop feedback system, utilizing external position transducers integrated into the fixturing/tooling, enabled real-time monitoring of the assembly process. This ensured that each crimp met the precise specifications required.
RESULTS
Implementing the Promess EMAP led to dramatic improvements in the catheter assembly process resulting in:
- Consistent Force Application: The EMAP’s precise control ensured that each crimp was within the required force range, eliminating issues of being too loose or too tight.
- Enhanced Quality Control: The real-time monitoring and closed-loop feedback system allowed for continuous verification of each catheter during production.
- 100% Effort Test Certification: Every catheter produced now meets the proper specifications, guaranteeing that each one will function correctly.
- Increased Reliability: The manufacturer can now confidently produce catheters that are reliable and safe for medical use, significantly reducing the risk of product failure.
By replacing inconsistent hydraulic pressing with intelligent, closed-loop force control, the Promess EMAP helped the manufacturer eliminate defects, improve efficiency, and ensure patient safety. This case study highlights the importance of precision assembly in medical device manufacturing and the critical role of real-time force monitoring in ensuring consistent, high-quality production.
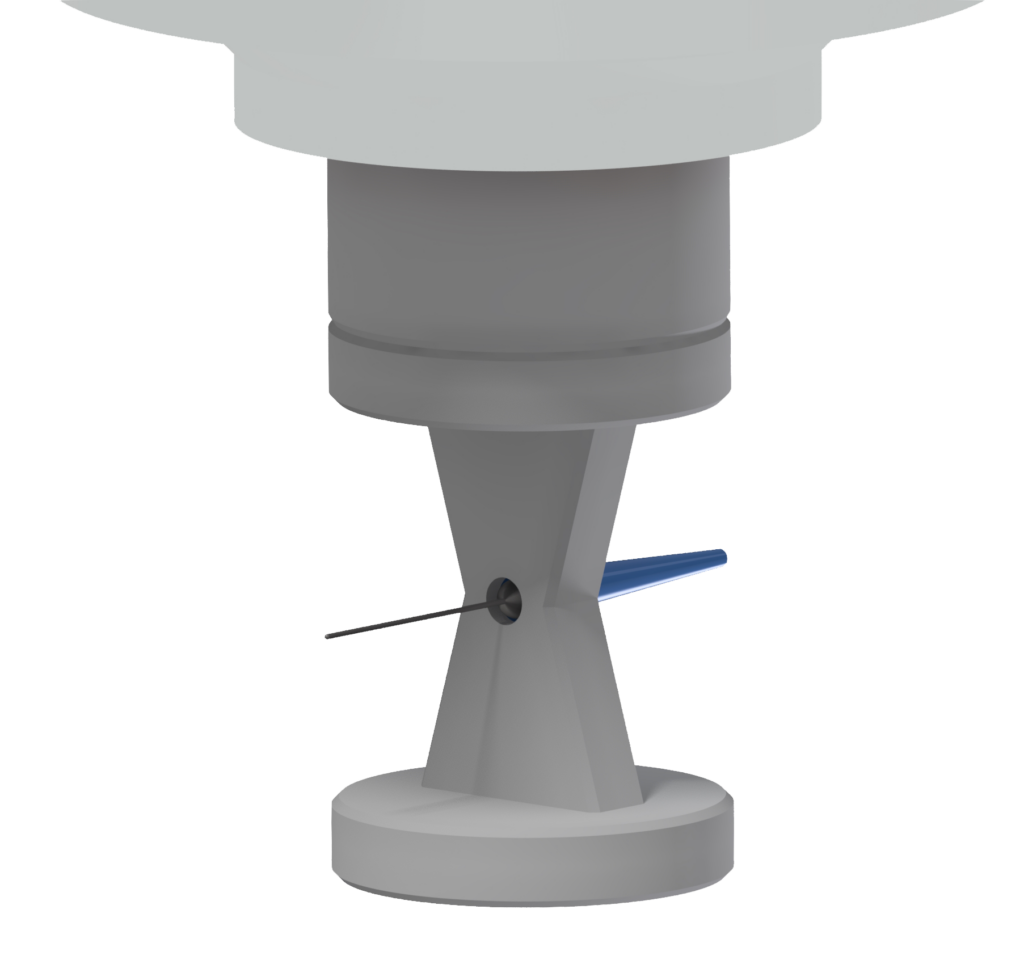
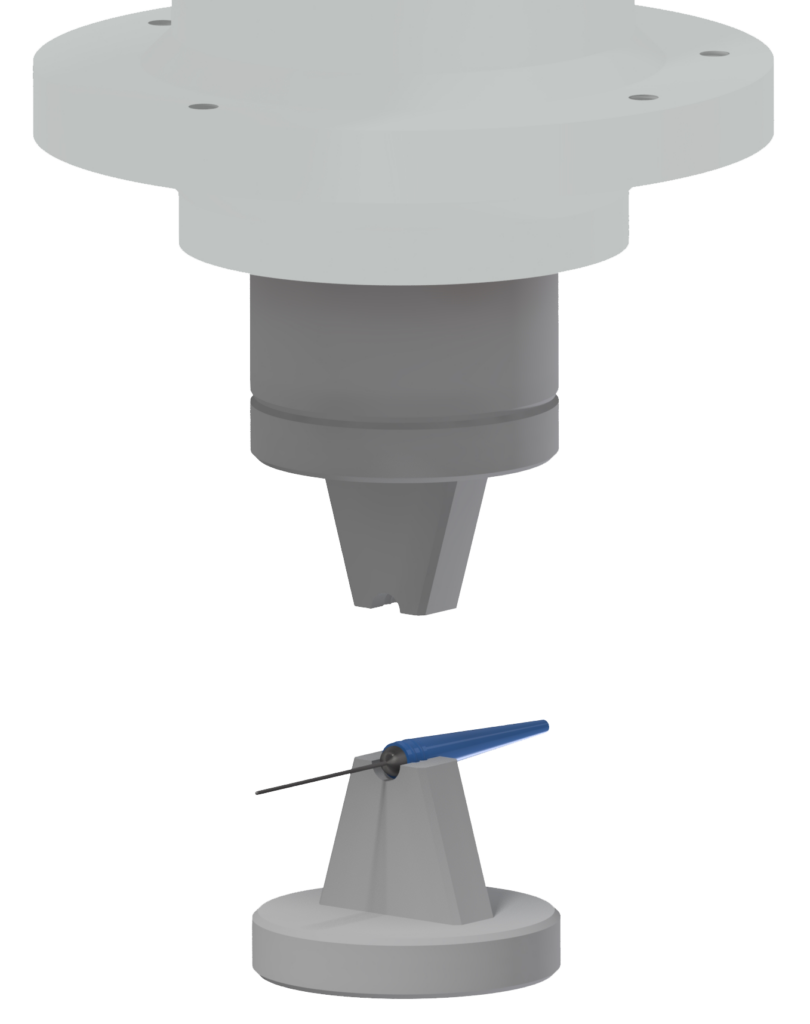
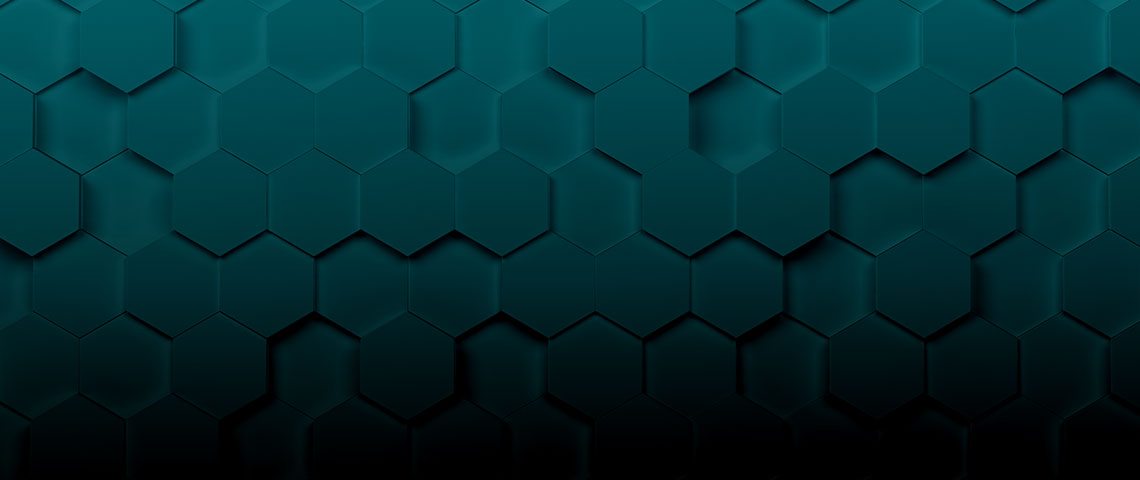
Do You Have an Application?
Talk to one of our expert engineers or learn more about proving your
application in our Process Development Center.