Case Study #1880 | TorquePRO
Crankshaft Testing with Promess TorquePRO
CHALLENGE
Crankshaft testing is a critical process in engine manufacturing, ensuring that the crank assembly rotates freely, is free from contamination, and meets functional specifications at various build stages. Traditionally, manufacturers relied on custom-built, in-house testing solutions, which often presented significant challenges:
- Complexity & Maintenance Issues: These systems were difficult to operate, maintain, and troubleshoot—especially when the original designer left the company.
- Limited Flexibility: Adjusting the system for different crankshaft models or testing parameters was cumbersome.
- Lack of Reliable Data & Traceability: Many setups did not offer comprehensive process monitoring, making it difficult to detect issues in real time and maintain quality records.
With the industry shifting toward in-process testing for improved quality control, manufacturers needed a standardized, reliable, and easy-to-use solution for crankshaft testing.
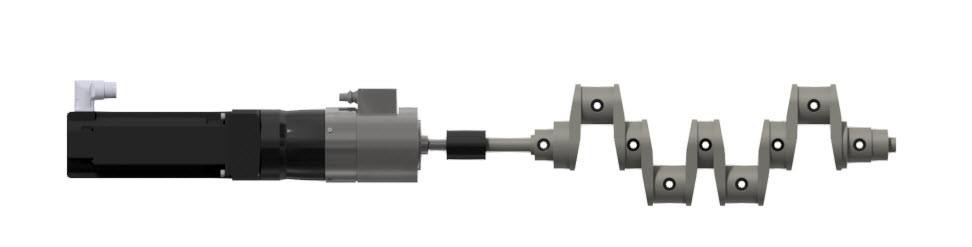
SOLUTION
Promess introduced the TorquePRO system, a standardized torque test solution that offers maximum flexibility and precision in crankshaft testing. Paired with a Promess Motion Controller, this system provided a complete, user-friendly solution with:
- Advanced Torque Testing Capabilities: The TorquePRO system and software package allow custom programming for any combination of rotational positions and torque values, with user-defined acceleration rates.
- Comprehensive Process Monitoring: Key parameters such as breakaway torque, running torque, torque at specific angles, angular position, and time are continuously monitored.
- Automated Part Verification: If any process parameter is outside the acceptable range, the system can be programmed to flag the part, abort the test, or initiate a retest based on specific requirements.
- Full Data Storage & Traceability: The system records torque and angle values, peak torque, and torque-over-angle graphs, storing all relevant cycle data (date, time, serial number, tolerances, etc.) in a centralized database for full traceability.
- Ongoing Support: Promess provides 24/7/365 support for the life of the system, ensuring manufacturers can adjust processes or troubleshoot issues as needed.
RESULTS
The implementation of Promess TorquePRO improved the crankshaft testing process by:
✔ Providing real-time failure detection through torque-over-angle graphs, allowing manufacturers to identify and address irregularities before they lead to defects.
✔ Ensuring process consistency and quality by standardizing crankshaft testing across different models and specifications.
✔ Eliminating the challenges of in-house solutions with an intuitive, maintainable, and flexible system.
✔ Enhancing traceability and compliance with comprehensive data recording for every part produced.
By integrating Promess TorquePRO, the manufacturer eliminated unreliable testing methods, improved process efficiency, and ensured every crankshaft met stringent quality standards—ultimately reducing rework, scrap, and production downtime.