In the dynamic world of automotive manufacturing, precision is the cornerstone of success. Every component must be meticulously assembled to ensure optimal performance and reliability, and nowhere is this more evident than in the assembly of automotive water pumps. In this case study, we’ll explore a fascinating case study that highlights how the Promess Electro-Mechanical Assembly Press (EMAP) has revolutionized the assembly process, overcoming challenges and setting new standards for accuracy and efficiency.
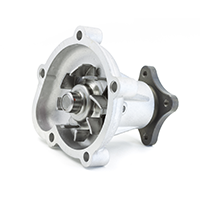
The Challenge: Precision in Water Pump Assembly
The assembly of automotive water pumps presents unique challenges. Various components, including the bearing pack, impeller, and hub, must be pressed to specific dimensions relative to a machined surface on the pump housing, rather than to a shoulder. This precision is essential for ensuring proper pump flow and belt alignment, critical factors in the functionality and longevity of the water pump.
Traditional Solutions:
Traditionally, manufacturers relied on hydraulic presses with fixed tooling or servo-controlled presses with pre-measured parts to assemble water pumps. However, these methods fell short in meeting the stringent requirements of precision assembly.
Hydraulic presses struggled to accommodate the tight tolerances required, while servo-controlled presses with pre-measured parts added complexity, cost, and floor space due to the need for multiple gauging stations. Moreover, these methods couldn’t adequately compensate for variations at the press station, leading to inconsistencies in assembly quality.
The Promess Solution:
Enter the Promess Electro-Mechanical Assembly Press (EMAP), a paradigm-shifting solution designed to address the challenges of water pump assembly head-on. The EMAP is a closed-loop, servo-controlled, ball screw press system that integrates an external position transducer into the press tooling.
During the assembly process, the EMAP measures the critical dimensions of the components in real-time using the position transducer. A master part is utilized to calibrate the transducer, establishing the zero point for precise assembly. The system then adjusts the press to achieve the desired position, compensating for variations in pallets, machine deflection, and part spring back.
The Outcome:
The implementation of the Promess EMAP has transformed the water pump assembly process. With a tolerance of ±0.03 mm, the EMAP ensures consistent, precise assembly of components, surpassing the capabilities of traditional methods. By gauging parts and pressing them to tolerance in a single station, the EMAP streamlines the assembly process, reducing complexity, cost, and floor space requirements.
Furthermore, the EMAP monitors the force versus position signature to ensure the correct interference fit of the components, guaranteeing optimal pump flow and belt alignment. Manufacturers can now produce water pumps with unparalleled accuracy and reliability, setting new standards for quality in automotive manufacturing.
Innovation is the driving force behind progress in automotive manufacturing, and the Promess EMAP exemplifies this ethos. By overcoming the challenges of water pump assembly with precision and efficiency, the EMAP sets a new benchmark for assembly technology. Manufacturers can now embrace the future of assembly with confidence, knowing that the Promess EMAP delivers unmatched quality and performance.
Are you ready to revolutionize your assembly process? Explore the possibilities with the Promess EMAP and unlock new levels of precision and efficiency in your manufacturing operations.