Application
A manually operated release mechanism is placed into the housing body. A seal is then placed into one of the body halves. Then an air actuated press assembles the two body halves with integrated male and female clips. A torque test is then conducted on the release mechanism to assure proper assembly and functionality.
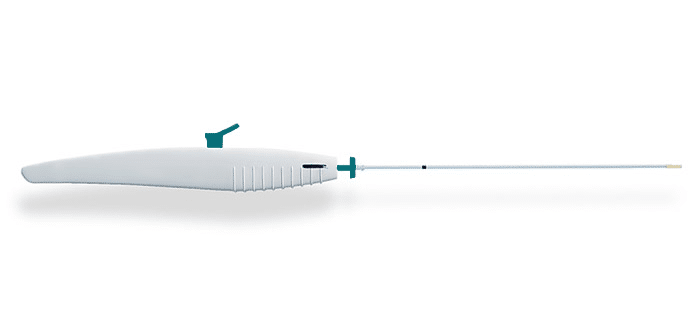
Challenge
A medical equipment manufacturer was experiencing intermittent product failures in the field. The original assembly technique was not adequate for a medical device manufacturer and there was no monitoring or traceability. The assembly presses that manufactured the vascular closure devices had very little quality control and because of this, assemblies would sometimes see failures of the release mechanism or a seal that was not properly installed leading to the male/female clips being un-joined but still progressing down the assembly line.
These issues were costing the manufacturer thousands of dollars in reworks and end-of-line batch checking. The manufacturer found that the problem was two-fold, because installation of the release mechanism and seal were done by hand, the “human element” had to be taken into account and because there was no in process monitoring, issues that could have been easily fixed became failures in the field. Promess offered an Electro-Mechanical Assembly Press “EMAP” with integrated force vs. position monitoring as well as a TorquePRO system for functional testing of the final assembly.
Solution
After Promess application engineers found the proper forces for the housing to be assembled and the necessary torque for the release mechanism functional test, the EMAP allowed the customer to press to the same force +/- .5% every time. With the TorquePRO now conducting a functional test on every vascular closure device, the medical manufacturer was now able to ensure 100% in process verification that every assembly was done correctly. This eliminated the need for end-of-line batch checking and gave them individual part traceability.
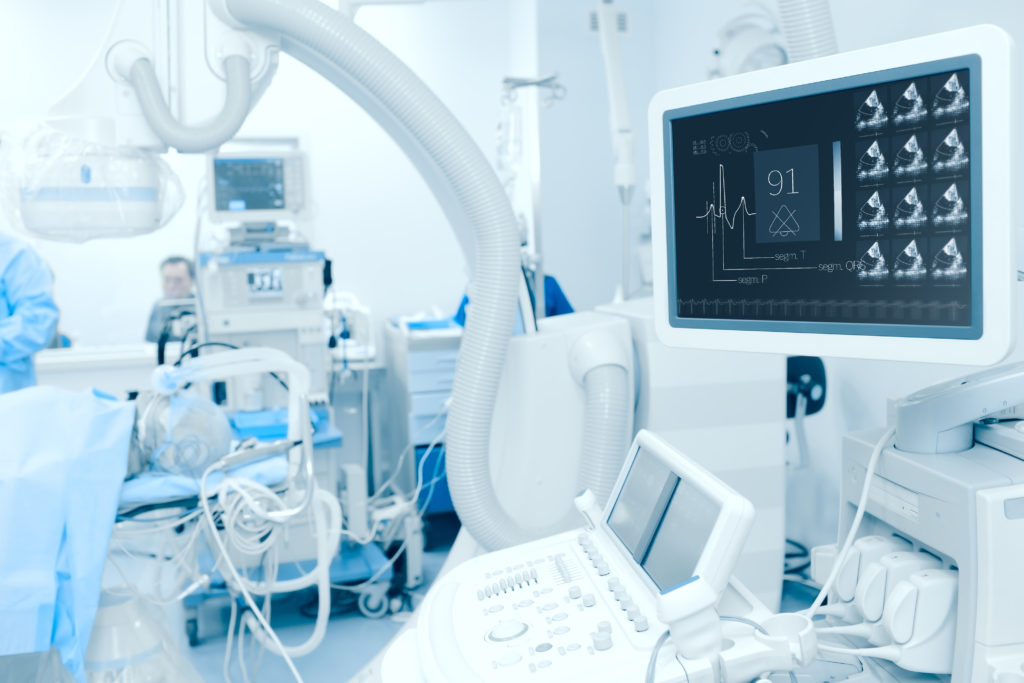