In the fast-paced world of automotive manufacturing, ensuring product reliability and safety is paramount. However, even the most stringent quality control measures can sometimes fall short, leading to perplexing challenges that defy conventional solutions. One such challenge that has plagued Automotive OEMs and tier two suppliers is intermittent fuel rail leakage.
Imagine this scenario: every fuel rail undergoes rigorous 100% testing, meticulously adhering to industry-standard leak test inspection protocols. Yet, despite these efforts, approximately one in every 100,000 fuel rails exhibits leaks once deployed in the field. The implications are staggering, ranging from potential injuries to costly recalls and warranty claims.
For the automotive industry, grappling with such intermittent failures posed a formidable obstacle to maintaining consumer trust and corporate reputation. The urgency to identify and address the root cause of this elusive problem was palpable, prompting a concerted effort to unravel the mystery behind fuel rail leakage.
Enter Promess, a renowned expert in assembly and quality control solutions. Recognizing the pressing need for a definitive resolution, Automotive OEMs and tier two suppliers turned to Promess for assistance. Together, they embarked on a collaborative journey to confront the challenge head-on, leveraging cutting-edge technology and interdisciplinary expertise to delve into the heart of the issue.
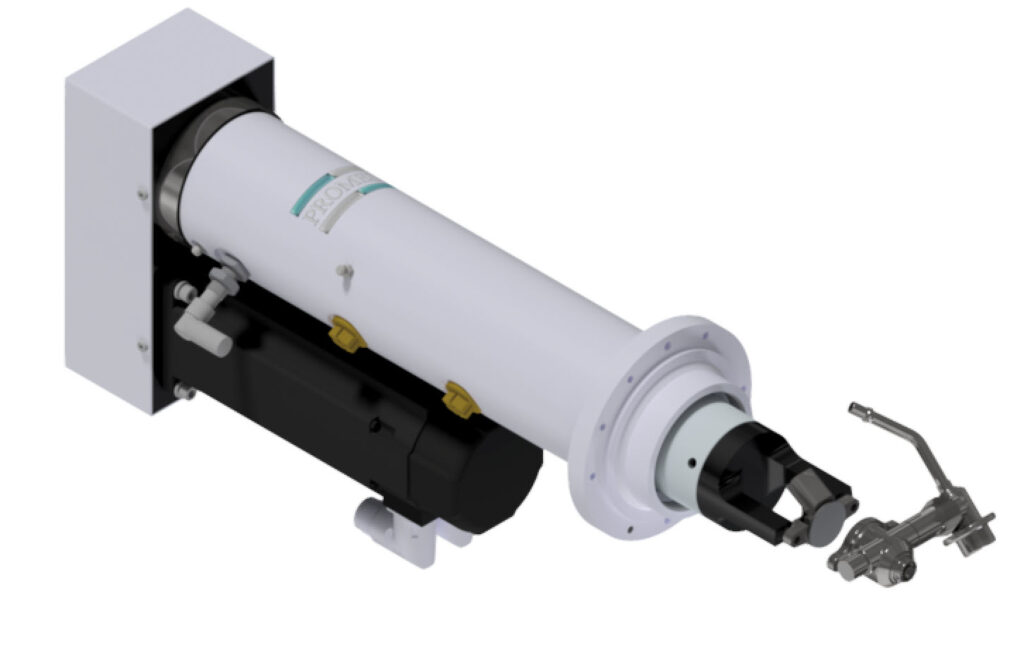
At the heart of the solution lay the Electro-Mechanical Assembly Press (EMAP), a sophisticated machinery equipped with differential monitoring capabilities. Through meticulous testing and analysis conducted at Promess’ Process Development Center, a breakthrough was achieved. Despite passing conventional pressure tests during standard inspection, the EMAP system successfully identified 100% of faulty components, offering crucial insights into the root cause of the failures.
The collaborative effort between the automotive industry and Promess exemplifies the power of innovation and partnership in overcoming seemingly insurmountable challenges. By embracing a shared commitment to excellence and a determination to push the boundaries of conventional thinking, they succeeded in unraveling the mystery of intermittent fuel rail leakage.
As we reflect on this journey, it underscores the importance of collaboration, perseverance, and technological innovation in driving progress within the automotive manufacturing landscape. Through collaborative innovation, we have not only enhanced product reliability but also reaffirmed our commitment to safeguarding consumer safety and trust.
In the ever-evolving landscape of automotive manufacturing, challenges will inevitably arise. However, it is through collaboration and innovation that we can turn these challenges into opportunities for growth and advancement. Together, we continue to push the boundaries of what is possible, forging a path towards a future defined by excellence and resilience in automotive manufacturing.