Mention “quality” and the almost certain response is “tighter dimensional tolerances.” But, with today’s machine tools able to mass produce parts with tolerances we couldn’t even measure just a few years ago, that is quickly becoming a dead-end street. It leads ultimately to a dimensionally perfect product that nobody can afford to buy because of the enormous sum of money needed.
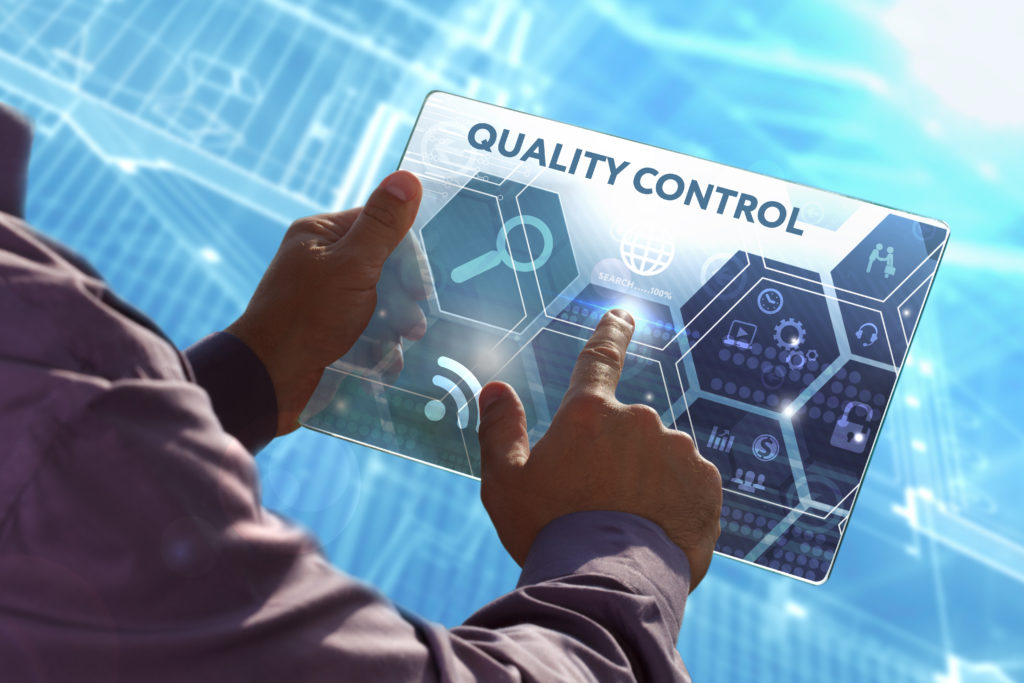
While things like engines and transmissions really do benefit from increased dimensional precision, and probably will continue to do so, there are a huge number of products that don’t. These products are fertile ground for a new definition of quality based on function rather than dimension, and new technologies that implement this approach.
Phantom Dimensions Are Everywhere
An automotive control arm is a good example of a product that requires geometric precision to achieve proper function, yet is made of components that cannot be produced economically with very close tolerances. The control arm links the vehicle’s front, and sometimes rear, wheels to the chassis, a function that requires a high level of precision, but it is made up of heavy-duty stamping with three rubber-encased bushings pressed in place – clearly not a candidate for extreme dimensional precision.
What automotive engineers typically do is define the geometry required in the assembly and leave the how-to achieve it part up to the supplier. Suppliers call this a “phantom” dimension, and it’s really quite common in a variety of industries.
A common approach to meeting the specification for a phantom dimension is to build very precise tools and fixtures, and then constantly adjust them to deal with the constant and totally unpredictable variations in heavy-duty stampings and rubber parts. Other suppliers choose to simply “press and hope” and then “measure and sort” and accept the scrap and re-work as a cost of doing business.
There is a third approach, however, based on an advanced Electro-Mechanical Assembly Press (EMAP) technology. This approach uses force and position sensors to implement a “push-measure-push” process that achieves an overall dimensional tolerance of 0.06mm for upper and lower control arms.
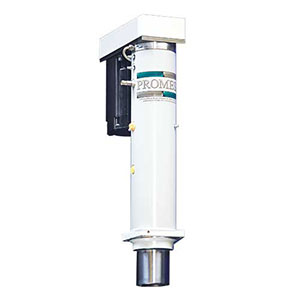
In one installation, four Promess EMAPs are configured in opposing pairs and mounted horizontally in the bushing insertion station at the end of the control arm assembly system. When the control arms reach this station, the ball joint and shock absorber stud have been installed and a snap ring pressed into place.
The ball joint is used to locate the control arm, which is then clamped for bushing insertion by the EMAPs. During this operation, the EMAPs repeat a ‘push-measure-push’ cycle based on their ability to monitor both ram position and pressing force with extreme precision. Both the absolute amount of force being exerted, and the rate at which that force changes over time are monitored.
System software collects this data and uses it to produce an operational signature of the process. By comparing the signature of the control arm being assembled, with the signature of a known good assembly, the control makes it possible to produce virtual clones of the good assembly with a high degree of reliability.
A New Way Of Thinking About Quality
The system just described has significantly improved the functional quality of the control arm it assembles with no change in the dimensional specifications of the component parts. In fact, it’s quite possible that the tolerances on those component parts could be loosened to reduce manufacturing costs with no impact on the finished product’s functional quality.
Function is the consumer’s measure of quality, and function ought to be the manufacturer’s as well. Manufacturers spend enormous sums of money to produce ultra-precise parts that are assembled with technologies that have not changed significantly in a century.
Why not spend less on the components and assemble them with an intelligent system that can accommodate dimensional variations and still produce functional products?
All that’s needed to make that happen is a willingness to step back and look at the possibilities inherent in today’s intelligent assembly technologies.