Manufacturing Engineering: How can software help manufacturers improve overall productivity?
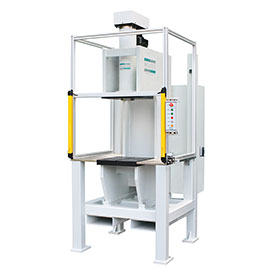
Andy Joseph, VP of Engineering at Promess: Software can make a huge impact in productivity whenever workers can multitask. For example, I remember a day when personal computers could do only one thing at a time. Windows fundamentally changed how people work by allowing them to multitask among several applications.
An operator using a Promess Electric Press Workstation is able to safely and efficiently multitask between part loading, unloading, inspection, and operating other equipment, by relying on the smarts built into Promess Software. Contrast this with a manual press where the operator must give sole attention to what’s happening throughout the whole assembly process, including watching for misalignment and attempting to ‘feel’ if a good part is being made.
ME: Describe the latest software additions from your company.
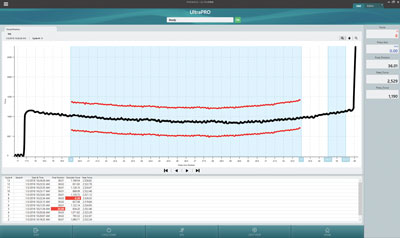
Joseph: Last year we introduced the UltraPRO software suite, which is our third-generation software that runs our systems. UltraPRO provides a unified software for all Promess systems, ranging from traditional Force/Position monitoring, assembly presses, to complex multi-axis functional part testing.
The centerpiece is our new controller hardware that runs the UltraPRO controller software. The controller connects the entire Promess system, including sensor preamplifiers and servo drives, through a real-time network using standard Ethernet cabling. The suite has a new HMI and editing software that runs on Windows, allowing a person to see what’s happening in the system, to manually control the system, configure the system, and write programs.
The entire suite was built from the ground up using an Agile software development approach with an emphasis toward good user experience design.
ME: How does software give your automotive customers an edge in helping improve quality control, long-term reliability, or other factors?
Joseph: The automotive industry is trending away from large, expensive, complicated assembly lines and toward smaller cell-oriented processes that are more agile and scalable. Because our presses have built-in sensing, they can measure and verify the part as its being made, reducing the need for additional quality checks after the part is assembled. The measurement data can be sent to other quality systems such as Q-DAS or QualityWorx using the Promess Data Service. Furthermore, our press systems excel at rapid changeover to different parts. They can be programmed to support hundreds of part programs and each program supports unlimited variation through the use of modifiable parameters, which can be updated through PLC logic or operator entry.
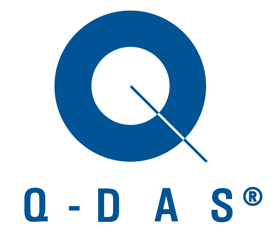
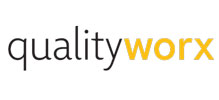
ME: What key software features, such as connectivity, ease of use, multitasking or other factors, can help users ensure success?
Joseph: One of my favorite quotes is from Andrew Grove, the former CEO of Intel Corporation: ‘Make mistakes [sic] faster.’ Good software design should create a safe environment for humans to make mistakes yet protect against their impact. Lots of software do this wrong by assuming that humans proceed in a linear fashion when programming a system and they use cumbersome pop-up questions or block human input to prevent mistakes. The UltraPRO editing software accommodates non-linear user interactions through a feature called Validation, which allows the user to make mistakes, while editing offline, and visually flags them with a quick explanation. Once the mistakes are corrected, the program can be downloaded to the controller. The Promess UltraPRO improves on connectivity by using standard HTTP-style traffic between the controller and other software in the suite. This simplifies matters when firewalls are turned on or network switches are used to filter traffic. The UltraPRO employs Apple Bonjour technology for locating and identifying controllers on the network. Bonjour replaces the need for IP addresses with human-readable names for true plug-and-play access. Configuring network settings is unnecessary for simple to moderate installations. When desired, IP addresses can be used for tightly controlled networks.
ME: How will the push toward new smart, connected machines with the Industrial Internet of Things [IIoT] affect users of your software?
Joseph: When you look at the manufacturing industry today, what you’ll find is more of an ‘Intranet of Things.’ In many ways, the users of our software are accustomed to the idea of machines talking to each other using technologies like Fieldbus and real-time Ethernet. Attempts to extend connectivity to machines beyond the ‘Intranet’ have been slow because manufacturers are rightfully reluctant to expose the plant floor to potential attacks. There is clear value in obtaining data produced by machines on the plant floor. Today, our customers can deploy the Promess Data Service on their Intranet to automatically collect and aggregate data produced by any number of Promess systems into standard SQL format. The data can be consumed by most analytical tools, including our Database Viewer software, which displays Promess data as its produced, enables searching and filtering of data, and exporting to other formats.
ME: With the auto industry closing a record year, how does the economic climate look for the short-term future?
Joseph: Despite the recent volatility of the stock markets and some talk of a coming recession, JD Power and LMC Automotive are forecasting a record 18 million automotive units manufactured in 2016. This bodes well for the automotive industry going into 2017. For those of us in the manufacturing technology space, the long-term outlook is even brighter. Electro-Mechanical Assembly Press technology, which Promess helped to invent over 20 years ago, is now a mainstay in automotive manufacturing. This technology is just starting to make its way into other industries like medical, energy, electronics, and consumer goods, to make higher quality parts at a lower cost.