Introduction
Motorized ball screw-type actuators are used to move and position many critical aircraft components, including wing flaps, elevators, tabs, slats, rudders, stabilizers, landing gear and a host of ancillary components. In most of these applications the actuators must function reliably to ensure the overall safety of the aircraft, and manufacturers and regulators have established rigorous testing and certification requirements, which include 100% functional tests for the final assemblies prior to shipment and installation. Tests (“Science Project”) commonly fall into one or more of four basic methodologies:
Free Running Torque
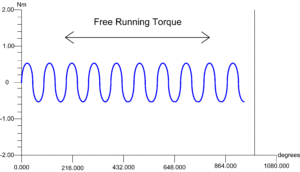
Free Running Torque is about measuring the amount of effort or torque it takes to run the actuator under zero load conditions—also known as torque-to-turn—typically consists of measuring the input torque while driving the actuator forward and in reverse. Captured and plotted, these values determine whether the assembly falls within a certain threshold.
System Efficiency
System Efficiency is often the main test to determine if an actuator assembly is functioning at an acceptable level. It’s calculated by measuring the input torque required to drive a pre-set resistance load. Varying the resistive load applied to the actuator will also determine if the efficiency of the actuator assembly is affected by the level of load it has to drive.
Mechanical Stiffness (Lash)
The most common test is to lock the input shaft in position and apply a precise thrust load to the output side of the linear actuator, record its position, then replace the thrust load with an equal but opposite pulling load on the actuator and record that position. Calculating the difference between the two positions gives the mechanical stiffness (lash) of the system.
Transmission Error
This test can be very important when positional accuracy is critical, such as in wing flap actuation. The rotational position of the input shaft can be directly correlated with the linear position of the actuator throughout its travel to verify that the correct components were properly assembled.
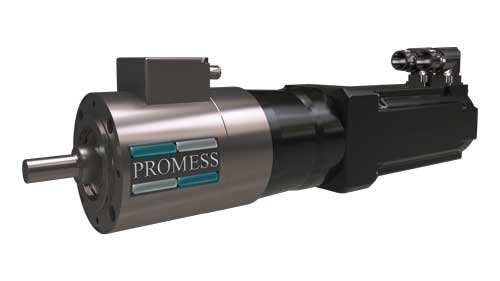
The System Efficiency test is probably the most common actuator performance test used in A&D—and the most difficult to implement. Few aerospace manufacturers have the internal resources and expertise required to design and build efficient apparatus to perform any of these tests, let alone the vital 100% testing of key components and sub-assemblies.
Most aerospace test apparatus is cobbled together in-house from a variety of components that were not intended to work together. These “science projects” may perform the required measurements, but seldom, if ever, do it efficiently. That’s why the industry norm is 100% functional testing of the final assembly, and sampling the components and sub-assemblies.
Current Technologies
Current technologies—provided by my company and others—are very efficient at sensing functional parameters of a part, sub-assembly, or finished assembly and determining whether or not it’s acceptable before it leaves the production line. Coupled with data storage and part tracking, this makes it possible to prevent “bad” assemblies from ever making it farther into the production process.
Obviously, catching defective components and sub-assemblies before they are installed in the actuator is much more cost-effective than catching them during the final 100% functional test. The good news is that the technology to make it happen already exists. My company, for example, has supplied flexible test stations to actuator manufacturers to perform system efficiency and other tests. These standardized solutions are built with hardware and software purposefully designed for interoperability in functional testing applications.
All of the motion control, data acquisition, data analysis, and documentation can be done by our controller. These systems make 100% functional testing practical for all components and sub-assemblies in an actuator.
For the manufacturer it’s a win-win situation. They get lower cost by eliminating defective components and sub-assemblies earlier in the manufacturing process and higher quality by assuring 100% testing and trace ability of every component that goes into every actuator.