The Rotational-Electro Mechanical Assembly Press from Promess helped automotive supplier IFA Group reduce scrap rate by 90 percent.
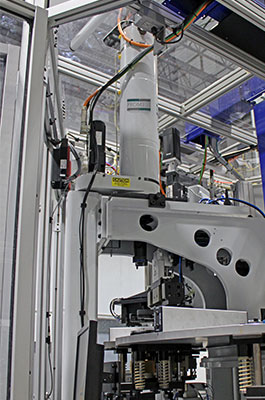
the REMAP-based
system has let IFA
Group reconfigure its
assembly process
and cut cycle time
from 46 seconds to 27
seconds.
Global automotive supplier IFA Group makes driveshafts and other components for cars, trucks, tractors and industrial machinery. The company has assembly plants in Germany, Poland, China and the United States.
One of the company’s main products are universal joints and constant velocity (CV) joints. These devices allow uninterrupted transmission of torque while the driveshaft is flexed. Universal joints utilize two yokes which are joined with a cardan cube or cross. CV joints use steel balls that travel in steel grooves to transmit the torque. Constant velocity joints allow higher inclination angles than universal joints. The rotational speed of the shafts joined by a CV joint are identical at all times, even if the joint is flexed. In contrast, the rotational speed of shafts joined by a universal joint oscillates continuously if the shaft is flexed.
These joints are decisive for the vehicle’s noise level. They also influence the size and weight of the driveshafts. In case of a vehicle collision, joints aid the shaft parts to telescope, thereby protecting lives. IFA has developed different classes of universal and CV joints that cover all performance and durability requirements.
One of the company’s newest products is an advanced disk-type constant velocity joint (DCVJ), which is used in a variety of luxury automobiles. IFA’s U.S. subsidiary, IFA-Group North America, makes DCVJs at an assembly plant in Ladson, SC.
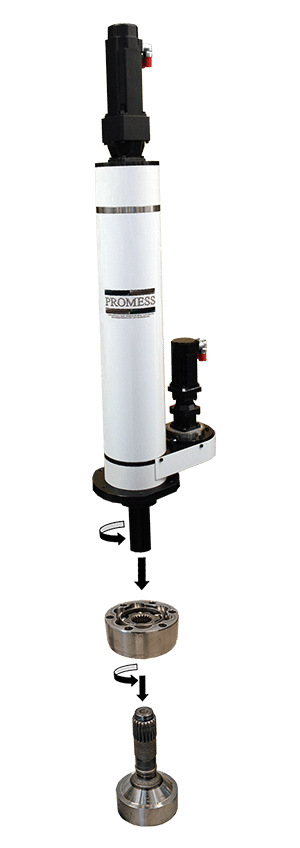
Each joint consists of an axially grooved inner and outer race with a cage containing six steel balls between them. The balls run in the grooves to transfer constant motion between the races while the joint flexes.
In a front-wheel drive, all-wheel drive or independent rear suspension vehicle, each driven wheel typically has a CV joint at each end. The joint at the wheel end typically includes a stub shaft to which the rotating brake and wheel assembly is mounted. The splined stub shaft is press-fit to the splined inner race.
Initially, the Ladson plant’s assembly systems came from one of the parent company’s factories in Germany. Unfortunately, the stub shaft assembly operation was a challenge from the beginning.
“With the press system, we were experiencing a 20 percent failure rate in the stub shaft assembly operation,” says Joey Watkins, CVJ value stream leader. “The DCVJ was positioned over the stub shaft and an air-over-oil cylinder was used to apply a small preload and then oscillate for a second or two before initiating the press stroke.
“It was literally hit or miss as to whether or not the mating splines were aligned by the oscillation and when they weren’t; we got a damaged joint or a damaged stub shaft or both. It was all we had, so we lived with it for many years.”
That all changed when Watkins happened to see some marketing materials about the Promess Rotational Electro-Mechanical Assembly Press (REMAP), a servo-driven ballscrew press with a rotating ram and integral position, force and torque sensors.
“I read the flyer and immediately knew I had an application for the REMAP,” Watkins says. “I got in touch with Promess and our assembly system builder and started developing a ‘smart’ solution to our ongoing assembly challenge.”
Automated Assembly
Six months later, Watkins had a prototype of his REMAP-based assembly system using a Promess MotionPRO controller. It’s a 12-station dial-type system using the REMAP for the critical stub shaft assembly operation.
Parts are manually loaded and the first station aligns the inner and outer races to make sure they are parallel. The parts then index to the second station where the REMAP applies a small, 1-kilonewton load and begins rotating. As this is happening, the force, position and torque values are all monitored in real time.
“We look for a torque spike during the rotation,” Watkins explains. “That tells us the splines are aligned, so we perform a light press to keep the assembly together and then rotate everything back to the home position to realign the holes the customer uses to mount the joint. The CV boot, end cap, gaskets and the joint itself have to be lined up properly before we perform the final pressing operation.
“The REMAP and MotionPRO working together let us monitor force and distance on every assembly and produce a traceable quality verification,” Watkins continues. “The ability to find the data for the shaft and pull up graphs and take screenshots of them to include in reports for the customer is really important if you have an issue in the field.
“A lot of our customers use Promess equipment, so we can give them raw data straight from the Promess system and they understand it. That lets us discuss different measuring strategies or assembly strategies, and they understand how we are evaluating the product. It makes it a lot easier to communicate with the customer’s quality staff when they understand the systems we are using.”
Fortunately, that kind of customer interaction is a lot less common because the failure rate for the stub shaft assembly has been cut from 20 percent to 2 percent on the REMAP-based system. And while that’s impressive, it’s not the only benefit of the new technology.
“The flexibility of the REMAP-based systems has let us reconfigure the process and cut the cycle time from about 46 seconds to 27 seconds,” Watkins continues. “The new work flow includes an additional 11 to 12 seconds for boot installation that used to be part of the basic process, but we’re still well below the old-time requirement. The actual assembly operation only takes 18 to 22 seconds, but the operators can’t sustain that pace all day.”
Production has grown from 800,000 DCVJs produced annually on four German systems to 1.5 million produced on six REMAP-based systems. Each of the new systems can produce three different size assemblies with only a 30-minute changeover.
The Next Step
Not content with those achievements, Watkins and his team have designed and installed four universal machines using 12- and 30-kilonewton Promess Electro-Mechanical Assembly Presses (EMAPs). These use the same MotionPRO controls and are now the preferred standard system for center bracket and bearing assembly operations in the Ladson plant.
They also have designed a new, eight-station REMAP based system that offers slightly less flexibility while retaining all of the quality and productivity advantages of the 12 station systems. The major difference is a simplified workflow limited to one part instead of three and eight-hour changeover time. The major advantage is a significantly lower capital cost.
At the same time, IFA-Group North America has introduced a new family of DCVJs that require a much more sophisticated assembly capability including the ability to measure and control specific rates of change during the process. Those specifications are well within the capabilities of the REMAP-based systems without any modifications.
“We simply would not have been able to assemble these advanced products on the old machines,” Watkins says. “The product has grown with the process and that’s why Promess is now our preferred and specified vendor for measuring and pressing.”