In the world of manufacturing, even the smallest component can cause significant headaches when quality issues arise. This was the case for a company that was struggling with cracked plastic housings during the insertion of brass fittings. Despite implementing initial fixes, the problem persisted, leading to a quest for a more reliable solution. Here’s how the company tackled the issue with innovative torque testing technology and improved their production process.
The Challenge: Persistent Cracking of Plastic Housings
The challenge began with a common yet critical task: inserting brass fittings into plastic housings. This seemingly straightforward process was plagued by an unexpected problem—cracking of the plastic housings. Despite attempts to strengthen the plastic by adding a metallic ring around the opening, the solution proved to be only partially effective. The metallic ring did reduce the number of visible cracks, but it also masked the issue, making it difficult to detect cracks during visual inspections. This led to a significant number of defective parts slipping through the quality control process and causing frustration in the production line.
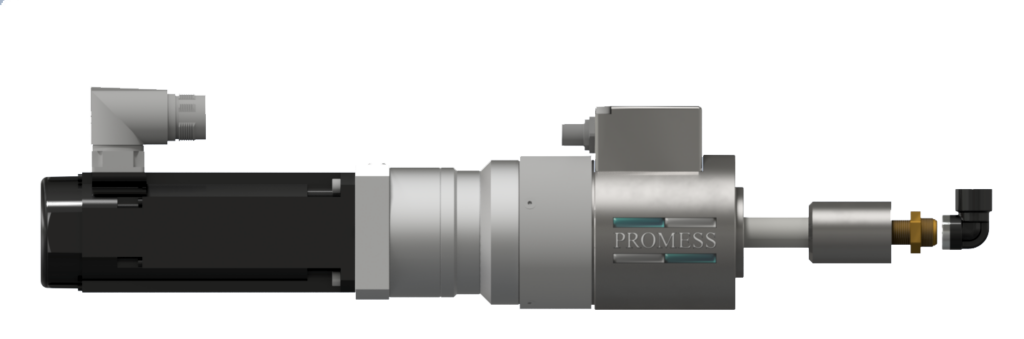
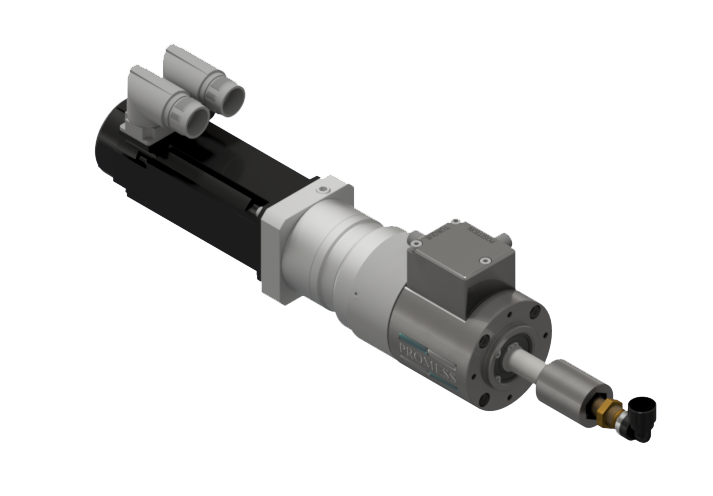
The Solution: Advanced Torque Testing Technology
To effectively tackle the problem, the company turned to Promess, a leading provider of precision assembly and test systems. They implemented a Promess TorquePRO unit to conduct a thorough inspection of each part. This device performed a revolution versus torque test, which plotted a detailed graph for each inspected part. By establishing upper and lower torque limits, the TorquePRO unit could accurately determine if a part was cracked or not. A cracked part would exhibit a torque that was too loose, allowing the system to flag it for rejection.
This method provided a reliable, non-destructive way to inspect every part, ensuring that only those meeting strict quality standards advanced through the production line. The clear, quantitative data from the TorquePRO unit gave the company confidence that they were catching all defective parts, significantly reducing the incidence of undetected cracks.
In addition to the TorquePRO unit, the company also considered using a Promess Motion Controller or EMAP (Electro-Mechanical Assembly Press) during the insertion process. These devices would allow real-time monitoring of the fitting process, instantly detecting any cracks as they occurred. This proactive approach could further enhance quality control by preventing defective parts from progressing through the manufacturing process.
The Results: Improved Quality and Process Efficiency
The implementation of the Promess TorquePRO unit transformed the company’s quality control process. With the ability to conduct 100% inspections, the manufacturer saw a dramatic reduction in defective parts. The precise torque testing ensured that every part met the required standards before moving forward in production, eliminating the frustration of dealing with hidden cracks and reducing waste.
The consideration of additional solutions, such as the Promess Motion Controller or EMAP, demonstrated the company’s commitment to continuous improvement and innovation. By exploring advanced technologies, they positioned themselves to further enhance their quality control processes, ensuring consistent product quality and boosting overall manufacturing efficiency.
A Commitment to Quality and Innovation
This case study highlights the importance of leveraging advanced technology to solve complex manufacturing challenges. The use of the Promess TorquePRO unit provided a reliable and effective solution to the persistent issue of cracked plastic housings, demonstrating the value of precise, data-driven inspection methods. As the company continues to explore new technologies like the Promess Motion Controller and EMAP, they set a standard for quality and innovation in the industry.
If your manufacturing process is facing similar challenges, consider how advanced torque testing and real-time monitoring technologies could help you achieve better quality control and efficiency. Investing in the right solutions not only resolves current issues but also paves the way for a more reliable and productive future.