The quality advantages of using an electric servo press to crimp, join, fit, stake and bend components of medical devices are driving an increasingly widespread adoption of this technology in the industry. It really started with catheters that require a small metal tube to be crimped to a larger metal tube that connects to the flexible portion of the catheter.
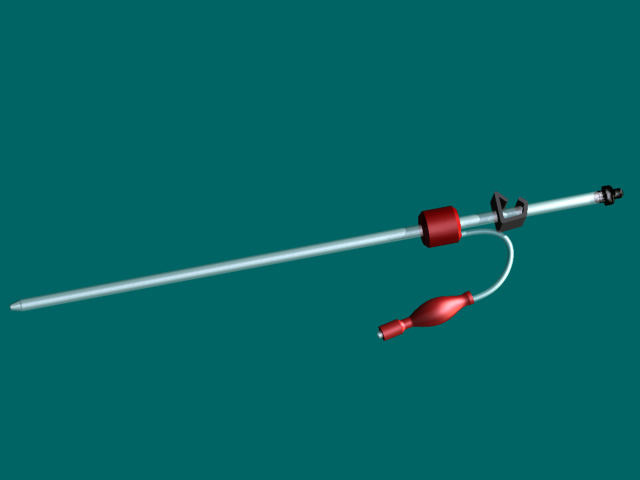
Under-crimped assemblies tend to come apart in use while over-crimped assemblies restrict, or even prevent, any flow through the joint. Both conditions lead directly to a less than-satisfactory patient experience with potentially serious repercussions for the manufacturer.
Using an appropriately instrumented electric servo press instead of the traditional hydraulic or pneumatic press has helped a number of catheter manufacturers overcome this challenge. Because the servo press can measure and record the force/ distance signature of each operation and compare it to that of a known-good operation, out-of-spec assemblies can be detected and discarded literally while they are being made.
As the application technology evolved, more sophisticated control algorithms allowed the press to “feel” the operation happening in real-time and use that information to control the crimping depth regardless of part variations. As the press is actuated, it feels the first contact with the part and uses that as a reference point. It then crimps to a depth relative to this reference point that can be controlled down to a few microns, if needed, by adding an external high-precision measuring device.
The most obvious impact of the technology is on product quality. Badly crimped assemblies are virtually eliminated from the customer’s viewpoint, and the fact that the parameters of every operation can be recorded helps in identifying the source of problem components so they can be removed from the process.
Those are critical contributions, but electric servo presses deliver a number of other less obvious advantages. They are, for example, extremely clean—no hydraulic fluid to leak or spill; no pneumatic cylinder oil mist in the air. They are also energy efficient: Hydraulic cylinders need a constantly-running power unit; pneumatic cylinders need a constant supply of compressed air; an electric servo press, however, only uses energy when it’s actually working.
Eliminating pumps and compressors also makes an electric servo press installation extremely quiet, and the floor space savings can be substantial. Self-contained electric servo press systems are easily configured as stand-alone workstations that deliver flexibility in system layout along with quick changeover capabilities from process to process. These benefits are all in addition to the much higher level of control, flexibility and accuracy available in assembly systems based on electric servo press technology. These advantages have enabled process engineers to create innovative new ways to make better, more repeatable, more reliable assemblies—and not just in catheter assembly operations.
A key requirement in medical battery manufacturing, for example, is to hold a constant pressure on the internal battery material during the curing process. Traditionally this has been done with pneumatic or hydraulic cylinders set to a pressure that attempts to match the load required for the operation. It doesn’t always work out as planned. But, with a programmable electric servo press system with built-in force and position control the operation becomes easier and much more repeatable. The press system is simply programmed to apply and hold the required force on to the material for the length of time prescribed. Moreover, the programmability of the system allows for very easy changeover when running a different product requiring different force levels and setups. And because the force and position sensing is built in and being controlled it can also be monitored and collected for record keeping and quality control. Better catheters and better assemblies powered by better batteries lead directly to better patient outcomes and that’s a benefit to which no price can be attached.