If the battery in your flashlight or cell phone fails, it’s an inconvenience. But, if the medical device batteries in your surgically implanted medical device (IMD) fails, it’s a medical emergency. Needless to say, batteries for the latter are very special and put together with extreme care.
Up to 90% of the volume of an IMD is the battery and the balance contains the electronics and other devices required to make it work. All of that is packed into a compact container that has to be as small as possible. Once it’s implanted and connected, it simply has to work.
Electro-Mechanical Assembly Press (EMAP)
Most IMDs today are powered by lithium-ion batteries, the same chemistry used in thousands of rechargeable applications from flashlights to cell phones to electric cars. Those consumer and commercial batteries are generally produced in large sheets with the lithium compound on either side of a center collector. The sheets are then cut to the size required for the final application and assembled. The thickness and density of the lithium compound on either side of the collector must be as nearly identical as possible to ensure that the chemical and electrical properties of the battery will be consistent from unit to unit. Any variation can shorten the life of the battery. The precision, feedback and verification required in applications like this make fully-electric servo press technology the right choice.
Promess Inc. has been involved in a number of battery projects in which its Electro-Mechanical Assembly Presses (EMAPs) with built-in force and positioning control technologies have replaced hydraulic press systems in both electrolyte pressing and battery assembly operations. While the fully-electric solution is cleaner and more energy efficient, the primary reason Promess technology is selected is that it provides the level of consistent process control and process verification required in the battery industry.
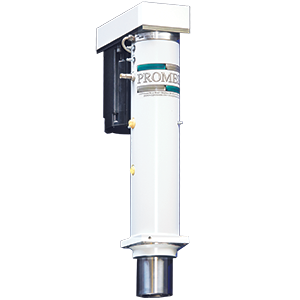
The EMAP is essentially a CNC press consisting of a ballscrew driven by a servomotor and equipped with an array of sensors to measure position, force, and any number of other process parameters that may be necessary. It applies force with extreme precision while measuring the functional result and feeding that data back into the control system. The precise control makes it especially ideal for various processes used in the manufacture of lithium-ion batteries used in IMD applications. Whether the challenge is to press the layers of electrolyte powder to extremely uniform thickness or compacting the material to a very specific density, utilizing a fully-programmable servo press with built-in force feedback delivers an optimum solution.
Electrolyte Thickness
Electrolyte thickness can be controlled to microns using the press’ precise positioning capability and the density of the material can be controlled and verified with its closed loop force feedback. In some applications the powder must be held at a very specific pressure for a period of time while it “cures”. With an electric press with force control, this is an easily programmed standard function. The programmability of an electric press also allows it to adapt quickly to variables in the compaction process like different powder chemistry or volume between battery models. Depending on the type of battery the same precise technology is also commonly used to crimp the two halves of the battery housing together. Finally, the built-in force and position sensors in the Promess press provide process verification data that is used to certify that each process was performed properly.
Fully-Electric Press Systems
Fully-Electric Press Systems have been operating for more than 10 years, producing batteries for literally thousands of IMDs that are performing precisely and predictably for patients all over the world. Many battery manufacturers have come to understand that the only way to achieve the levels of control required is with fully-electric servo technology.