Lean manufacturing is a concept that engineers often tend to over-think in design and over-complicate in execution. When it comes to assembly operations this often results in engineers stripping equipment back to the bare bones, which is almost always a huge mistake.
Lean means cutting the fat, not the muscle, or as Sami Niemela, the creative director of Finland’s Nordkapp Creative Oy, put it: “Lean is about being an athlete, not a skeleton.” You may ask, “What does that have to do with energy?” The answer is, a lot, because properly thought-out and applied lean assembly operations can be very green and energy-wise without any additional investment.
Application Example
Here’s an example from the electronics industry. Circuit board manufacturers have a problem because the connectors that have to be installed on their products can’t fit though the SMT (surface mount) reflow soldering systems used to attach the electronic components. That means high value, fully-assembled boards have to be processed through manual soldering stations where skilled technicians hand solder the connectors in place. A single connector may have a hundred or more pins and they are often small and densely packed. Scrap rates tend to be high and costly.
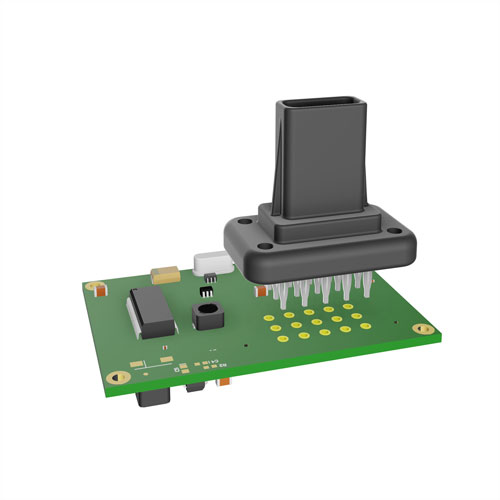
Compliant pin technology is a potential solution to this problem. The idea is to press the connectors into the circuit boards rather than soldering them. The compliant pins are radially flexible and create a mechanically and electrically stable connection to the sockets on the circuit board—with no energy-consuming solder operation required.
Obviously, a press-fit assembly process is familiar and easily automated, which should make the transition from hand-soldered assembly a no-brainer. In practice, however, it has turned out to be neither simple nor straightforward.
The issues come at initial engagement between the connector and circuit board, where many things can go wrong. For example, what happens if a pin on the connector is bent and doesn’t line up with the hole it is to be pressed into? What if there is a mismatch and the wrong connector is going to be pressed into the board? Maybe one or more of the holes is blocked by an imperfection or solder. What if the machine didn’t line up the connector and board properly?
The outcome of these “what-ifs” is generally the same. The press tries to force the connector and board together, destroying both—at its most expensive point in the process.
These challenges can be overcome by using a sophisticated servo-driven electro-mechanical press with the appropriate sensors and the right software. Promess has supplied hundreds of these systems to circuit board manufacturers for use in automated cells implementing compliant pin process.
The heart of these systems is a proprietary digital signal conditioner (DSC) designed specifically to monitor the initial engagement between the connector and the circuit board. The DSC has a linearization algorithm built into its calibration routine that gives the press the ability to measure force accurately at the low end of its measuring range. This lets it monitor the initial engagement point precisely and the closed-loop positioning control of the system allows it to stop the press cycle before it damages the part if a problem is detected.
Once past this critical stage with no problems detected, the system continues the operation until the connector is fully installed. Force and position data for each assembly is analyzed and stored for quality assurance purposes.
Because the system is fully programmable, the hardware can be used to assemble a wide range of connectors to a wide range of boards simply by changing locator and gripper details. One smart piece of equipment in one cell doing a multitude of operations is the essence of lean manufacturing.
Manually soldering thousands of circuit boards a day means that hundreds or more of industrial soldering stations are consuming electricity all day, every day in the plant. Much of that energy is wasted keeping the soldering iron hot while the operator is handling boards and positioning connectors. The electro-mechanical press, though, draws electricity only in the pressing operation. It uses no power when it’s idle.
Moreover, SMT reflow soldering systems can be precisely calibrated to handle the high temperatures at which today’s lead-free solders have to be applied without damaging sensitive electronic components. That’s not as true of the manual irons used in the traditional process.