Intelligent Servo Technology
Dumb presses utilizing hydraulics and pneumatics may be just fine for simple applications that don’t require much in the way of precision, accuracy or consistent quality. Outdated technology may be just fine when there is little at stake if the component fails once in use and when data regarding the assembly of the component is unnecessary.
But when a product’s performance is on the line, when a poorly assembled product will result in a shorter lifecycle & lower customer satisfaction, or when a customer’s health and safety may be put at risk, you need more intelligence in your system than a typical hydraulic or pneumatic system can deliver.
That’s where Promess’ all electric servo technology comes in. Whether your application involves precise and repeatable force, torque, and positioning, or some combination of any or all of these, Promess’ suite of products for use in industrial, assembly, and lab settings, has you covered.
EMAP Snap Ring Application
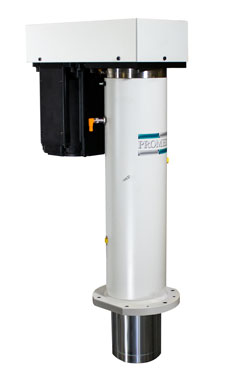
Take, for example, an application that involves incorporating snap rings as an integral component in a steering column assembly. Simple enough for a dumb press to push a snap ring down over a shaft, but if not done correctly: if the snap ring is not properly in position or properly secured, that could cause major performance issues AND possibly put the user of such a system, in a very dangerous position.
Can Businesses Avoid This Problem?
Yes they can. The best way to avoid these problems, is to use a smarter press system that is able to do the job right while verifying whether or not the job has been done properly, and will let you know if and when there is a problem. In this case, the Promess Electric Press (EMAP), would be a great solution.
Signature Analysis
During the set-up and run-off phase of the application, once the Promess Electric Press is in place, several parts can be run in “teach mode.” While in teach mode, the Promess Electric Press can identify precisely the appropriate range of position & force that are required to create good parts. Furthermore, the in-process monitoring capability of the EMAP system can be used to create a signature analysis curve which can be immediately gaged against the known good signature (+/- acceptable variation) to guarantee every part is a good part, and that when something is potentially dangerously out of the ordinary, the system is smart enough to let you know.
Snap Ring Application: Signature analysis curve example:
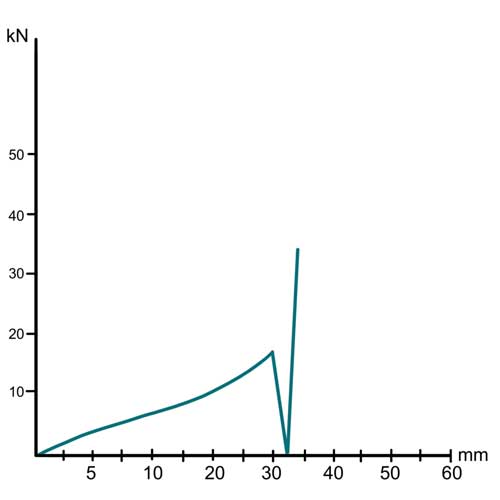
During the initial phase of the press cycle, very low force is seen as the press ram extends to just above a touchpoint. At the touchpoint, which should be very close to a known position value relative to the ram’s home position, the press should register an increase in the amount of force being applied. Once the snap ring reaches the detent in which it will remain, the press ram should see a brief drop in force, followed by a sharp spike, all within a known position range, at which point the press should begin to back off and retract.
This is exactly what is shown on the signature analysis curve above.
Once this curve is collected, it can be gauged against a known good curve, +/- appropriate limits, and this assessment can be used, in real time, to determine whether or not the process has created a good part that will perform properly and safely in the field.
Furthermore, the data collected can be used to verify both individual parts, and the entire process, contributing to continuous improvement efforts down the road.
How smart does your press system need to be?
The answer to that question is, of course, smart enough to get the job done right, however much that may be. And Promess is the only company out there which produces smart systems for force, torque, and positioning in industrial assembly and test applications that are not only smart enough to “know” what they are doing, but are also capable of providing you and your customer with the data that verifies it.