In 2004, Promess Inc.’s founder, Larry Stockline, wrote an article describing how two fairly new technologies, real-time process monitoring and signature analysis, were combined to improve the quality of an automotive wheel-stud insertion system. The system he described used linear variable differential transformer (LVDT) sensors to monitor the operation and hydraulic cylinders to press the studs. A four-channel Programmable Control Assembly Monitoring System collected the inputs and ran the signature analysis software.
The goal was to provide missing and/or wrong stud detection and 100% traceable certification of every assembly. It worked very well, and was the basis for a number of similar systems built for wheel suppliers in several countries. Fast-forward to now where that relatively simple solution has morphed into an “intelligent” assembly system that does much more than simply insert studs and make sure they are present and seated. Now the hydraulic cylinders have been replaced with instrumented electric servo presses that control and monitor insertion force in real time as well as monitor seating depth.
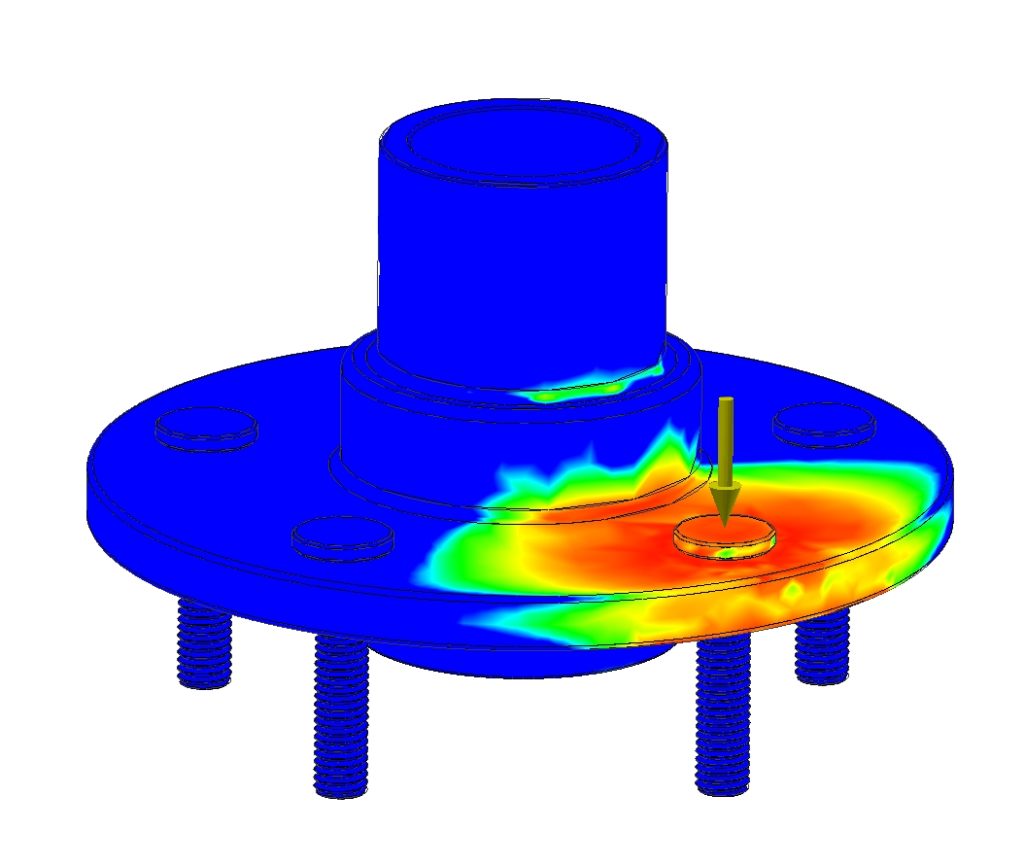
This came about because some clever customer engineers noticed that monitoring the signature during the insertion process told them not only when the stud was seated, but also exactly how much force it had required. With that information available in real time, they reasoned that a more precisely controllable cylinder could be programmed to supply just enough force to seat each stud and no more. The attraction of that concept was the inherent ability to minimize the force applied to the hubs and thereby reduce the number of bent hubs that had to be scrapped. The hydraulic cylinders in the old system typically applied 12,000 lb (53.4 kN) of force to make sure that even the most mismatched stud/hole combination would produce a properly seated stud. In reality, though, most studs were fully seated at 4000–8000 lb (17.8– 35.6 kN) of force, so excess force was frequently applied to the hub, often bending it.
Replace Hydraulics with Electric
The new insertion system replaces the hydraulic cylinders with Promess’ programmable Servo Presses (EMAPs) that are equipped with sensors to measure both force and location. The control software monitors the signature of each stud insertion in real-time and stops the press when the stud is properly seated, limiting the force used to only the amount of force required (instead of hitting each stud with the maximum 12,000 lb).
In practice that means that most studs are inserted with 4000–8000 lb of force, well within the plastic deformation limits of the hubs. By inserting the studs “intelligently” rather than by brute force, the system greatly improves the hub end-of-line flatness measurements and also saves energy by using just enough to properly seat each stud. The technology available for assembly systems today is far more sophisticated and capable than that of only a few years ago. That will lead to major changes in how technology is applied.
In many ways the situation is similar to the evolution of machining technology in the last few decades. Where purpose-built transfer lines were once the best solution for high-volume manufacturing, cells of flexible CNC machines are now the norm.
It’s only a matter of time until clever engineers make the same kind of transition in their thinking about assembly systems. The tools exist now; it’s time to put them to work.