There are several critical factors that are encountered through the various steps of the injection molding process, all of which can be solved with a Protech Machine Injection Molding work cell powered by a Promess, servo-controlled REMAP system.
The REMAP was developed by Promess to provide controlled & programmable rotational & linear motion, while simultaneously monitoring & gaging force and torque in a single system. The REMAP is modeled after the Promess EMAP servo-controlled press that has been in production since the early 1990’s. Both the REMAP & the EMAP combine servo-controlled ball screw press technology with Promess’ fully programmable UltraPRO controls and software.
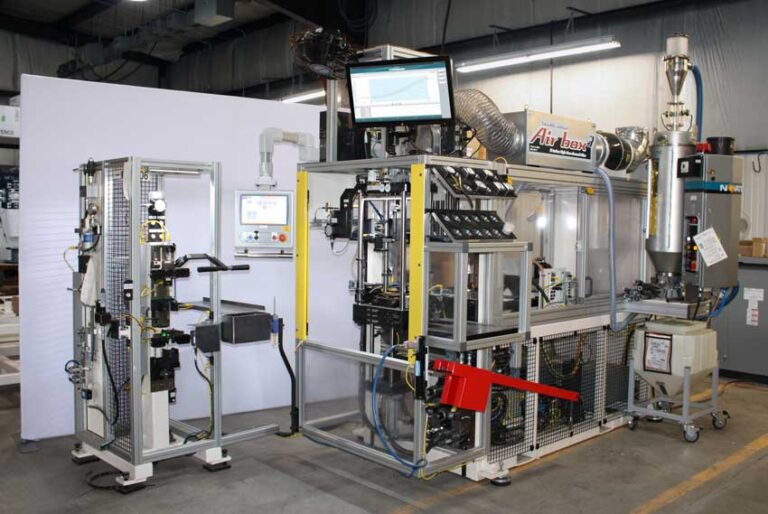
Promess, Inc. and Protech Machine have partnered to become the leading supplier of critical injection molding machines. Combining Protech’s decades of specialty machine building expertise with Promess’ motion and sensing expertise, over the last 20 years, the two companies have provided solutions for complex processes to companies worldwide.
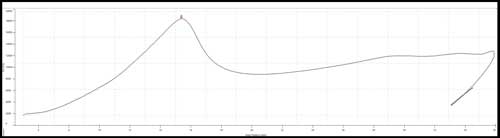
Among the critical factors the REMAP can control and monitor in the injection molding process are:
- auger rotational speed (and torque)
- initial press force and linear speed
- press force and linear speed through the mid-phase of the injection molding process
- final press force & linear speed
- as well as hold time, as required
With Promess’ REMAP system for injection molding, you get:
- Improved Quality: Improved dimensional quality of injection molded part by up to 50% over conventional injection mold processes. Eliminated short shots by use of Promess’ patent-pending fill process.
- Servo Control: Servo control gives you complete control of motion, and especially of maintained force, throughout the process. When adjustments need to be made, even to accommodate changes in the materials as they are processed (heated, cooled, etc.), servo control can accomplish that.
- Closed Loop Feedback: Closed-loop sensing and feedback keeps you informed at every point in the process and gives you the data, in real-time, to respond. Integrated sensors in tandem with Promess’ powerful software, provide feedback so you know what’s going on and so the system knows what going on. This gives the system the “sense of feel” so that it can respond appropriately, automatically, to whatever circumstances arise, alerting you to problems that occur, and often, correcting and preventing those problems from occurring in the first place.
- Data Acquisition: The advanced data acquisition engine for process monitoring is the “brains” of the Promess system. It takes your easily programmed parameters for positioning and force, as well as any other sensible dimension, and ensures that they are maintained throughout the process. The system’s programmability gives you the control, and the data acquisition tells you what has actually occurred in the process, to ensure you have created a “perfect” assembly, every time.
- Intuitive Programming: The linear and rotational axes, which are the primary factors in achieving such a high level of control, are easily programmed through a straightforward, intuitive interface, that requires a minimal amount of training to master.
- Energy Efficiency: Finally, the Promess REMAP system for injection molding operations is a cleaner, more energy-efficient solution, requiring power only while in active use and having no requirement for messy, potentially hazardous materials like hydraulic fluid. It does all of this within a minimal footprint too, taking up considerably less of your precious floor space.

If you had the option to perform your injection molding operations with state-of-the-art, all-electric, servo-controlled processes that virtually guarantee the success of each individual product produced, why would you do it any other way?
Want to learn more about our Injection Molding Kit? Click Here.
Promess is recognized as the leading U.S. manufacturer of highly adaptive motion systems used by companies around the world to assemble and test their products.