Hydraulic Presses vs. Electric Presses
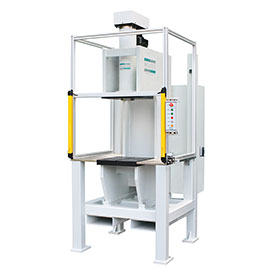
It is no coincidence that hydraulics became the default technology for pressing applications during the century of cheap energy. Well, that century is over and today’s reality is very different.
It is highly unlikely we will ever see energy that cheap again, which means, among other things, that it’s time to rethink the way we use electricity to generate kinetic energy in a broad range of pressing applications. The truth is that hydraulics are not a very efficient way to do it.
In fact, it takes on average 25–30% more electric power to produce the same level of performance in a hydraulic system as compared to an all-electric system.
If you’ve ever put your hand on a hydraulic unit after it’s been running for a while, the reason for that will be obvious. Chances are the system is so hot you can’t keep your hand on it.
Saving Energy Means Saving Money
That heat is wasted energy. It’s not doing anything productive, and it never will. Worse yet, even more energy is probably being expended keeping that system cool since heat is the acknowledged enemy of hydraulics.
In physics, the law of conservation of energy states that the total energy of an isolated system cannot change it is said to be conserved over time. Energy can neither be created nor destroyed, but it can change form.
If the goal is to convert electric energy to kinetic energy, as it is in most machines, a hydraulic system will only deliver 50–60% of the input energy at the point of application. Almost all of the rest is converted to heat, which is lost to the environment.
In a fully electric system, however, 85% or more of the input energy typically is converted directly into kinetic energy. That’s a significant difference, but it’s not the whole story.
Hydraulic vs. Electric: Which is Better?
In the hydraulic system the motor and pump run constantly, consuming energy whether or not any productive work is being done. That is significant because in a typical 15–18 second automotive work cycle the actuator is only energized for two seconds.
An all-electric system, on the other hand, uses energy only when it’s actually working. That accounts for the 25–30% missing energy in the comparison.
All of that hydraulic hardware—motors, pumps, reservoirs, manifolds, valves, pipes, hoses, filters, etc.—not only eats energy, it also eats up a lot of expensive plant floorspace. It’s noisy and requires constant maintenance to avoid costly and potentially dangerous spills.
An all-electric system, on the other hand, requires only power and control cables and perhaps an electrical enclosure that can be mounted virtually anywhere. It’s virtually silent, and as close to maintenance-free as any mechanical device can be.
With a modern all-electric press the entire process can be instrumented and controlled with a degree of precision that is simply not possible with a hydraulic system. This enables a whole set of innovative approaches to assembly quality, including performance-based measurements that can accommodate a wide range of component variables.
Hydraulics will continue to have their place, but that place grows more limited in scope every time the cost of energy increases. The future is electric because energy is just too precious to waste.