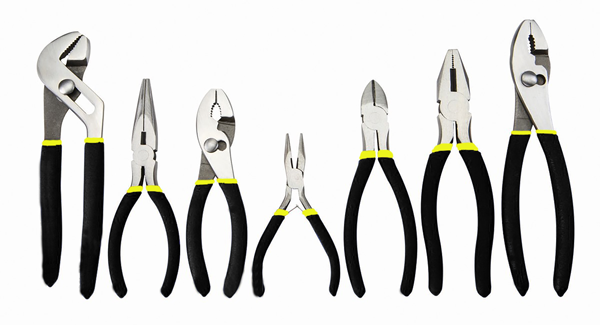
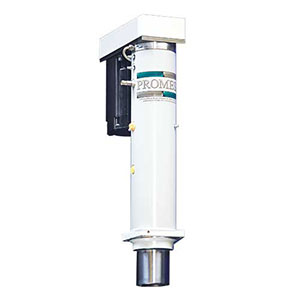
Have you ever purchased a brand new set of pliers and upon opening the package found them so stiff that you felt like you needed the ‘jaws of life’ just to pry them open? Or had them flop open because the rivet joining the two halves was so loose that it felt like they were going to fall apart at any second? This was a very common complaint voiced by professionals, from those who use these tools every day to the weekend warrior who only use their pliers once every six months. The tooling manufacturers have heard these complaints and turned to Promess to help them overcome these assembly issues.
Using a combination of Promess’ Electric Press (EMAP) and TorquePRO technologies, tooling manufacturers are now able to assemble each and every tool to specific functional criteria ensuring each completed tool will have a ‘just right’ feel to it when needed for the next job.
The Assembly Process
After the two halves of the pliers and the rivet are placed in the station by the operator, the Promess EMAP UltraPRO controller will move the press ram down to find a touch-point position and thus gauge the initial rivet height. Doing so allows the system to negate the variances inherent in the rivet heights. Once found, the servo press will extend an additional relative distance from the touch-point position to form the rivet. At this point in the assembly process, control is passed to the Promess UltraPRO controller for the TorquePRO unit which will rotate one of the handles through a predetermined set of angles. The system will measure, capture and store the torque at each position before returning to the initial ‘rivet position’. Following this initial press and measure sequence, three outcomes are possible.
- As the torque measurements are gauged in-process, the first outcome would be that the gauged values are within acceptable tolerances. If so, the part is removed from the station and moves on for further processing.
- The second outcome would be that the one or more of the gauged values were found to be below a determined threshold (i.e. the pliers are too loose). In this case the EMAP will cycle again but will now employ a ‘Move to Force’ strategy, moving to a preset force value instead of a position value. The TorquePRO will then test the assembly again. This Press-Measure-Press assembly strategy can be utilized as many times as necessary to ensure that every tool is assembled to the same functional criteria every time.
- The third outcome that may occur following the initial rivet press and measure sequence is that the first set of torque test readings are determined to be above acceptable limits (i.e. the pliers are to stiff). In this case, the TorquePRO system will run a ‘wear-in’ program where the tool is exercised through several closed-open-closed cycles. Measurements are taken to determine if additional wear-in is required.
Functional – The first time, every time!
By incorporating Promess’ Electric Press and TorquePRO technologies in conjunction with a unique assembly and in-process functional testing process, manufacturers are now ensuring that every tool they ship will have that ‘feels good’ functionality right out of the package the first time, every time!
Problem Solved = Satisfied Customers!
This is just one case where incorporating the feedback from multiple sensors into the process has resolved a major manufacturing issue and helped to make a better more consistent part, which in turn has led to satisfied customers. Something every company strives to achieve!
Crimping, staking or riveting to a functional torque for tool manufacturing is just one example. This same ‘build to a function’ solution can be readily incorporated into any hinged or ball jointed assembly operations.
Please contact Promess Sales Department for further information 810-229-9334 or email [email protected]