Much of the focus of getting pressing done right in your manufacturing processes has been placed on precisely placed hard-stops and hydraulic or pneumatic force, maxed out against the physical limitations of the system. Much of the time, this process works just fine. Visual and other types of inspections may be relied upon post-process, for quality assurance, but when problems are found, assuming they are found and not missed in inspection either, it is usually too late to fix the fault and the assembly at that point is simply removed and consigned to scrap.
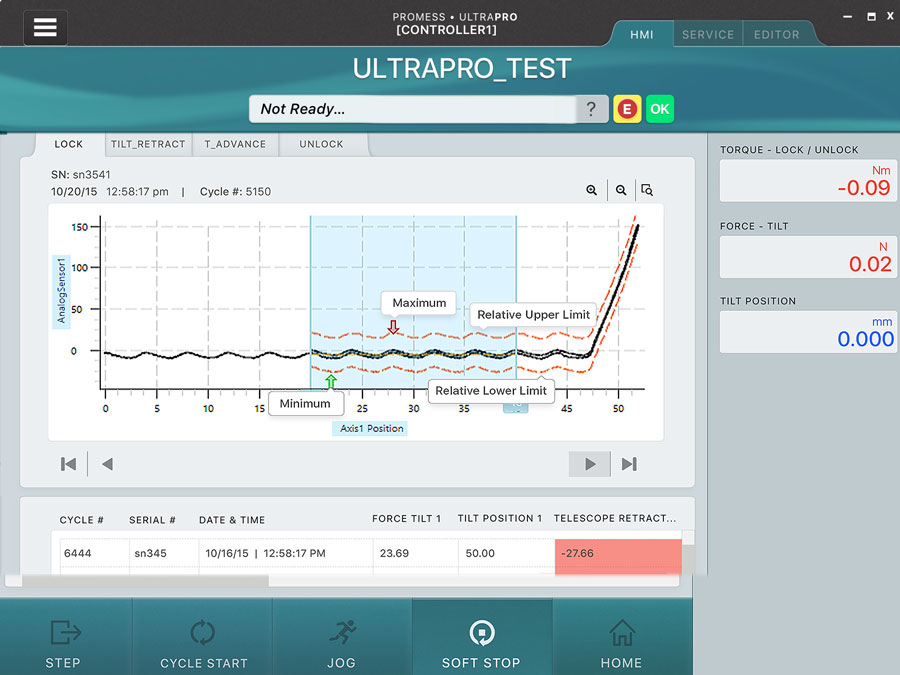
In-process monitoring and gaging, such as is possible with Promess’ EMAP Press systems, monitors and gages the most relevant part of the process, while it is being assembled. This gives the system the ability to react in real time so bad parts never leave the station; it gives you the knowledge that confirms and the data that proves every part produced is done so to spec & will function as expected; and it gives your customers the quality they need and the reason to keep coming back to you.
The integrated sensors, an inherent part of every Promess system, gather process data at the very point of production, while the part is being processed, and the system’s software gages that data in real time, before the part leaves the station. This closed-loop feedback enables you to make the best possible options for quality assurance.
Individual parts can be verified, and that same data can be used to validate and improve the process going forward.
The benefits of monitoring your press processes are almost countless, but there is no greater benefit than having full confidence, backed by Promess’ expertise and the Promess team, that you have delivered the highest level of quality to your customer. The quality that will keep them coming back to you.