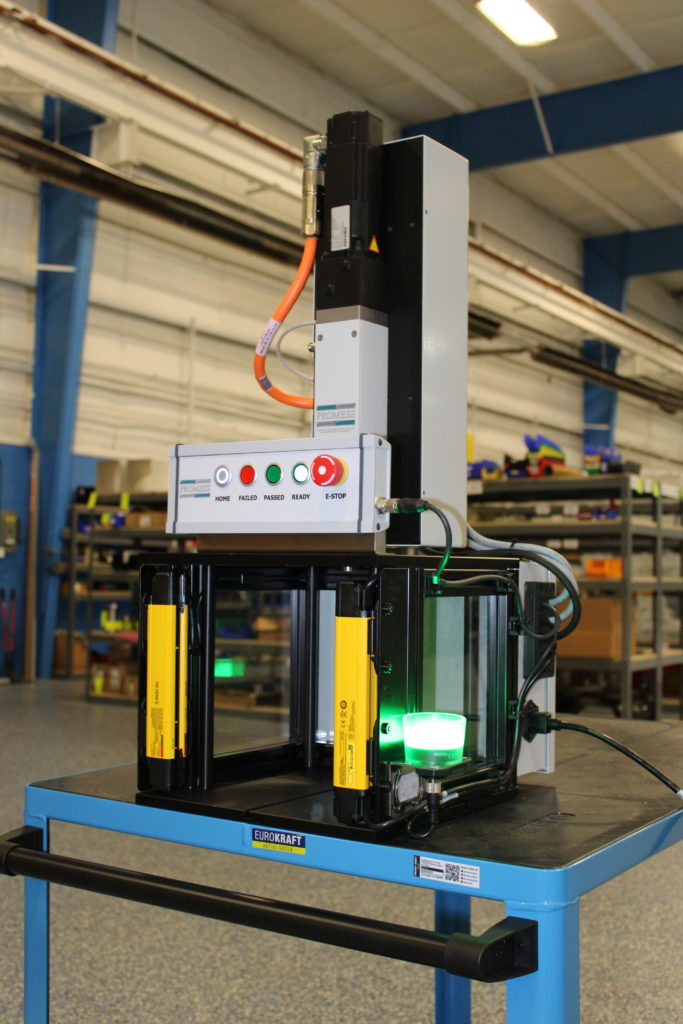
Promess Inc. is introducing a new smart press for assembly with fully integrated servo drive, force and position sensing, and controller electronics in a single light-weight package.
FlexIQ is designed for high-mix assembly environments. It delivers the flexibility needed to precisely assemble hundreds of part model variations in small batch production. It verifies the quality of every part through onboard data acquisition and monitoring algorithms.
Replace Arbor or Pneumatic Presses
FlexIQ is a compelling replacement for arbor or pneumatic presses that are traditionally used for high-volume assembly. The FlexIQ has built-in algorithms called “process types” that handle common applications. Applications such as bearing pressing, staking, crimping, bushing insertion, compliant pin pressing, as well as press-to-shoulder and press-to-distance. This approach using process types allows Promess to deliver decades of application expertise in a package that is easily installed and made operational in less than an hour. Bringing companies into the age of Smart manufacturing.
Smart Press Capabilities
At the heart of the FlexIQ is a simple web-based software served from the device itself. The human-centered design of the software walks newcomers through initial setup in a wizard-like fashion without requiring any programming skills. The software also provides a web-based dashboard that operators can view the force graph, live force and position readings, and quality measurements and limits, and overall part quality results.
The all-electric FlexIQ press is capable of forces up to 3.0kN (665lbf), has 300mm (12in) of available stroke, and can move at 200mm/s (8in/s). It also features a low 24-volt DC power requirement. This makes it ideal for assembly environments demanding quick changeover for varying part models. The low voltage power requirement obviates any concern over arc flash and the low weight makes it easy to move the press from one assembly station to another. It can also be ordered with a fieldbus interface for integration with a PLC.
FlexIQ can be easily installed into a customer-designed station or can be ordered with a standard 4-post station, called the FlexIQ Assembly Station. The station includes a power supply, safety controls, E-stop, light curtain, cycle start button, and plexiglass guarding along with T-slots to mount fixturing or tooling.
“When a manufacturer decides to purchase a new piece of capital equipment, the process from initial concept to production can be a lengthy one.” explained Promess Application Engineer Scot Stodart. “Many months, many man hours, and a significant amount of money, are consumed, often unnecessarily, during the process.”
We’ve made it our mission to drastically reduce the time it takes for an end-user, or a machine builder, to integrate new capital equipment into their manufacturing environment. We plan to expand the FlexIQ product line to handle larger loads and to offer additional accessories.
Promess is a 36-year-old firm that develops, manufactures, and markets its family of sensing devices, electronics, assembly presses and test systems on a global basis.