Challenge: Accurately fit tubes onto the end of barbed fittings with 100% proper assembly certification
There were several complicating factors in this assembly process that needed to be overcome. Among them were:
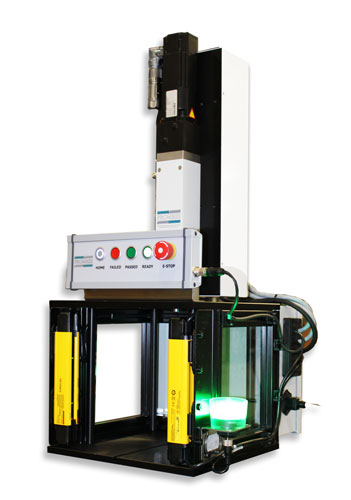
- The complications presented by having 2 different tube sizes and 2 different sizes of barb fittings on the same line, with one fitting/tube combination being slightly larger in diameter than the other
- The critical nature of proper alignment BEFORE the press action began. If the 2 components were not properly aligned, the barb fitting would rip through and permanently damage the tube
- The critical nature of full depth insertion. If the tube was not pressed to full depth, full engagement of the barbs would not be achieved, leading to the possibility that the tube may come apart during later processing
Solution
The Servo-Controlled FlexIQ Assembly Press System was used to control and measure force over distance through the entire working stroke of the process. These factors were able to be controlled and monitored in-process and simultaneously. By continuously measuring the force applied over the specified distance required for pressing completely, the system was able to ensure the parts were assembled 100% correctly without any of the errors occurring.
Promess’ Servo-Controlled FlexIQ Press System captured 100% of the errors outside the taught signature. The Promess FlexIQ Solution surpassed the expectations of the of the customer and allowed them to provide THEIR customers with certifiable documentation via Promess Data Acquisition.