While most industries rely on precision components, there are few where the need is as critical as in medical device manufacturing. Whether it’s a tool that ends up in the hands of a surgeon or a device used every day by a patient, the consequences of a poorly manufactured component could mean the difference between life and death.
How to Ensure Functionality
The question then becomes, how can every piece be produced to ensure correct functionality without employing costly options like end-of-line gaging stations or 100% inspection? One proven answer is to use a manufacturing system with built-in sensors that allow the system to “feel” the assembly as it is being put together, intelligent servo controls that allow the system to know what it’s looking at and adjust on the fly, and software with in-process monitoring capabilities that can gage the piece during the assembly operation.

Medical Industry Applications
Common medical-industry examples from among customers of our servo press include catheters or IV bags that are used to administer fluids to patients. Each of these uses a tube or connection that is crimped to a mating component to achieve a tight, leak-proof seal. With crimping, though, as with any manufacturing process, there is potential for defects. If a crimp is too loose, the fluid will leak and make a mess. If it’s too tight, the fluid won’t flow through the tube as fast as necessary, if at all.
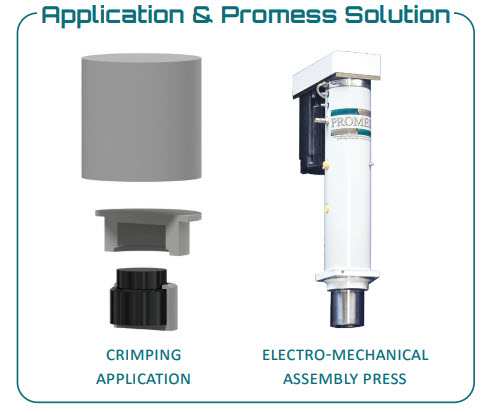
The key to the process is to use a system capable of “feeling” the difference between these defects and a good part. A system integrated with sensors and closed-loop control can crimp to a specified force every cycle, meaning that every part will have exactly the right amount of force applied during the crimping process. Coupling closed-loop servo controls with the integrated sensors means that the specified force doesn’t need to occur at the same position every time, allowing good parts to be produced even when the location of the part changes due to pallet height or fixture variations. A servo system can be easily programmed to accommodate multiple part models. That type of flexibility isn’t possible with a hydraulic or pneumatic system.
Software
Software is another key element of the system. With advanced monitoring capability, a force vs. distance signature can be generated for each part that is crimped. Each crimp will return its own unique signature, showing what happened during the relevant part of the cycle. Parts that were crimped successfully will return similar signatures, while parts that had a defect will return a signature that differs in some way from the successful signatures.
Once the differences between a successful crimp and a defect are known, a master curve can be set based either on the curve for a known good part or an average of a number of good parts. Next, limits can be set around that master curve. The signature for every part will then have to fall within those limits, or it will be flagged as “bad.” Individual gage points such as peak force, final position, or average force can also be collected, each with its own set of tolerances. If any of the limits or tolerances fail during the process, the system should give options as to how to proceed. Those options could include anything from simply flagging the part as different so it can be checked or fixed later, to stopping the operation immediately so the process and part can be reviewed. This type of data collection and control allows for 100% in-process monitoring, and eliminates the need for expensive end-of-line gage stations.
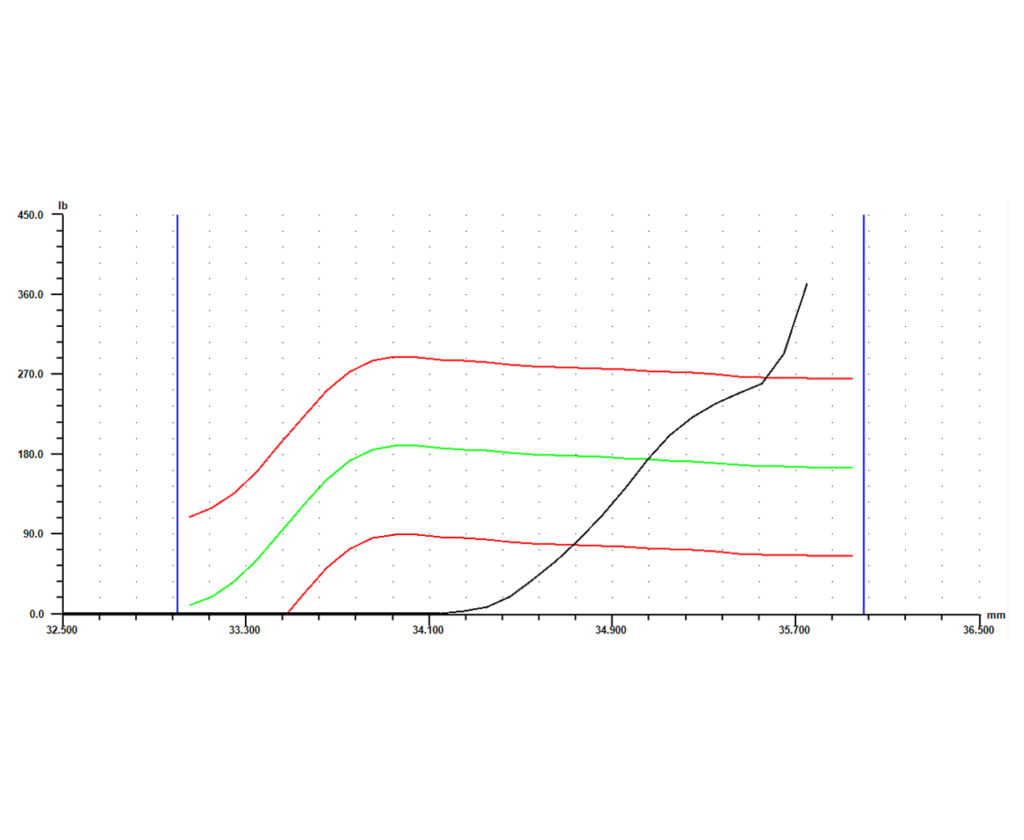
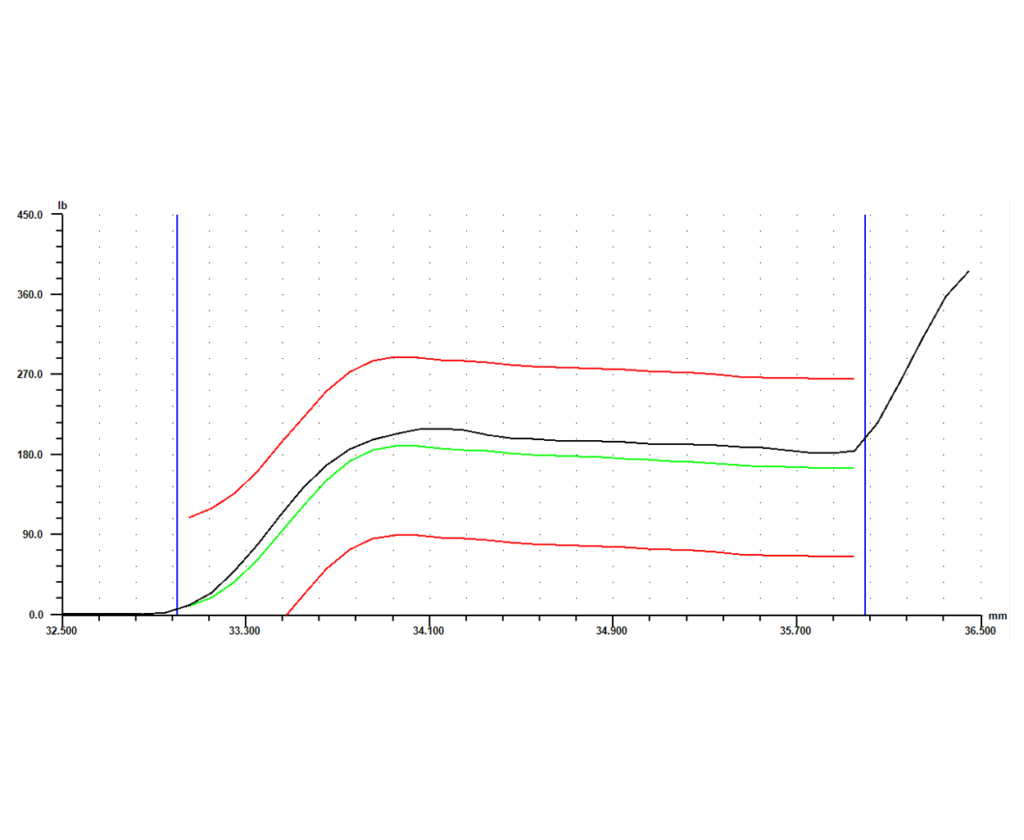
The final piece of the puzzle is storing the collected data. The system should have the capability to record any signatures and gage data it collects, along with identifying information like date, time, and serial number. Configured this way, the system not only gages every part as it produces them, it also keeps a record of every part for full traceability. This adds another level of protection to an already robust process, and allows the full benefits of the cutting edge system to be taken advantage of long after a part is manufactured.
The crimping application discussed above is just one example of many in the medical device industry. From crimped connectors to artificial limbs, simple tools to complex systems, medical devices are an excellent example of intelligent manufacturing systems, capable of producing a part that will function correctly every time. To make that happen, the manufacturing system needs to combine the latest hardware and sensor technology with cutting edge software. Doing so will ensure quality and reliability in a way that traditional assembly methods just can’t match.