The need for data collection in manufacturing is well established.
For decades now, the idea has been pushed pretty hard, and most (successful) companies have gotten on board. Quality of individual assemblies, efficiency & effectiveness of processes, and environmental impact, all stand to be improved with relevant data.
But, (and here’s the big question):
All that data you’re collecting… What are you doing with it? Are you putting it immediately to good use? Or have your good intentions fallen by the wayside? Are you now, simply collecting and hoarding data unnecessarily? What could you be doing better with your data to improve quality, productivity and efficiency? How can that data be put to use for you to improve customer satisfaction and, ultimately, your bottom line?
In-process data collection, monitoring & gaging
Unlike previous manufacturing technologies, Promess’ lines of manufacturing & test systems (for all of your operations that involve press-force, torque and/or linear & axial positioning,) collect, analyze & USE data, in real time, to improve your outcomes.
The closer to the point of assembly that data is collected and analyzed, the better; and no one gets you closer to that point than Promess, with their advanced systems for Torque, Force & Positioning, all with in-process data collection, monitoring & gaging.
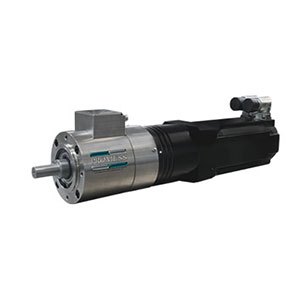
Regarding torque, Promess’ TorquePRO system is primarily used for torque testing. With Promess, this testing can be done during the assembly process, where adjustments can still be made if, and when, a product is found to be out of spec. This allows for maximum throughput of the highest-quality assemblies, first-time-through, avoiding costly repairs and preventing scrap and lower-quality assemblies from affecting your final products and your customers.
Data Collection: Software
Regarding force & positioning, the software behind Promess’ Servo Press system, in conjunction with integrated load cells, precision ball-screws and encoder-based feedback, monitors and gages applied force, final position (and position throughout the stroke), and gages this data, against user-defined parameters, to ensure sub-par assemblies never leave the station. The software’s easy-to-use programming options give you full control to determine what happens with good parts, and in the rare incidents when out-of-spec parts do result, Promess’ software gives you the ability to determine what happens with those components. Options include stopping the process for manual intervention, re-running the part, or allowing the part to continue on (tagged with its associated data) to be removed or re-processed later.
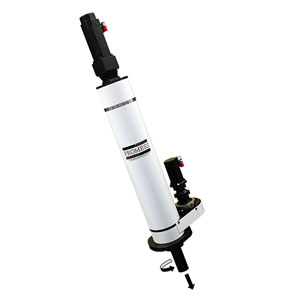
In those cases where your assembly process relies on both force/positioning AND torque, Promess’ REMAP also has you covered with real-time, in-process data which can be controlled & processed fully independently of each other, or with Promess’ new UltraPRO capability, utilizing coordinated motion.
Whatever your process needs are, and whatever your need for data and control is, Promess gives you the ability to ensure you are getting the most out of your data, putting it to use in real-time to ensure the best outcomes for you and your customer.
The unnecessary “data-hoarding” days are over. How is YOUR process benefiting from the data you collect?