In the fast-paced world of automotive manufacturing, quality control is paramount. Each component must undergo rigorous testing to ensure safety, durability, and performance. In this case study, we delve into a partnership between a tier one automotive stamping supplier and Promess, showcasing how collaboration and innovation have transformed the testing process.
The Challenge:
Our automotive stamping supplier client faced a daunting challenge: conducting destructive tests on the welds of seat rails while maintaining efficiency and accuracy. With the mandate to destroy 6 parts out of every 100 produced, and the need to store comprehensive test data, the task seemed formidable. Enter Promess, with its cutting-edge Electro-Mechanical Assembly Press (EMAP) technology.
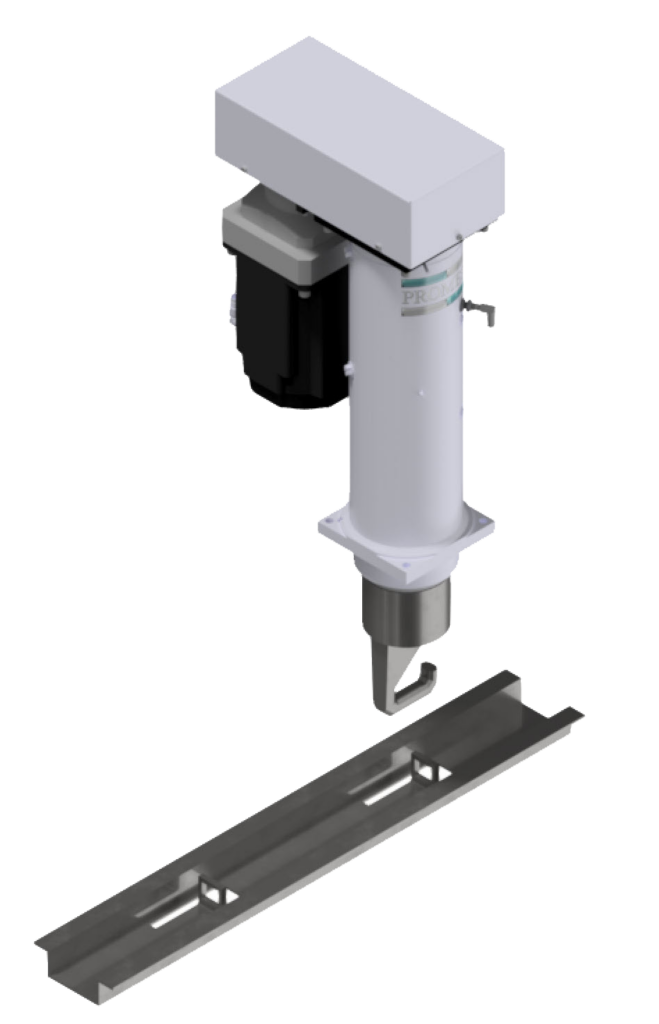
The Solution:
Rather than opting for a conventional approach of assembling individual components and developing custom software, our client embraced the innovative solution offered by Promess. Leveraging the capabilities of the EMAP-80, with its impressive 18,000-lb. capacity and bidirectional force measurement, proved to be a game-changer. This collaboration streamlined the testing process, reducing turnaround time by half compared to traditional methods.
Key Benefits:
- Standardization and Flexibility: The integration of Promess EMAP technology provided our client with a standardized, yet highly flexible testing solution. With the ability to run multiple programs depending on test requirements, the system offered unparalleled versatility.
- Cost Savings: By partnering with Promess, our client achieved significant cost savings, with the test machine costing 50% less than a specialized alternative. This not only enhanced their bottom line but also maximized their return on investment.
- Ease of Use: The intuitive operation of the Promess EMAP simplified the testing process for operators. With features such as remote control and automated data collection, it ensured seamless execution of test protocols.
- Data Integration: The seamless integration of data collection with the plant network facilitated real-time monitoring and analysis. Test data was archived to the mainframe at specified intervals, enabling comprehensive tracking and traceability.
Operational Excellence:
With the new testing solution in place, our client’s operators could effortlessly conduct destructive tests with precision and efficiency. From rapid engagement of pull hooks to the measurement of peak forces, every step of the process was optimized for operational excellence.
The collaboration between our automotive stamping supplier client and Promess exemplifies the power of innovation and partnership in overcoming industry challenges. By embracing cutting-edge technology and collaborative problem-solving, they have revolutionized automotive testing, setting a new standard for quality control in the industry.
At the heart of this success lies a commitment to excellence and a dedication to pushing the boundaries of what’s possible. As we look to the future of automotive manufacturing, it’s clear that collaboration and innovation will continue to drive progress, shaping the industry for years to come.