In the competitive realm of automotive manufacturing, ensuring the highest quality components is paramount. Yet, for one manufacturer specializing in injection molded automotive parts, achieving this goal proved to be a persistent challenge. Defects plagued their production line, resulting in subpar components reaching customers’ floors.
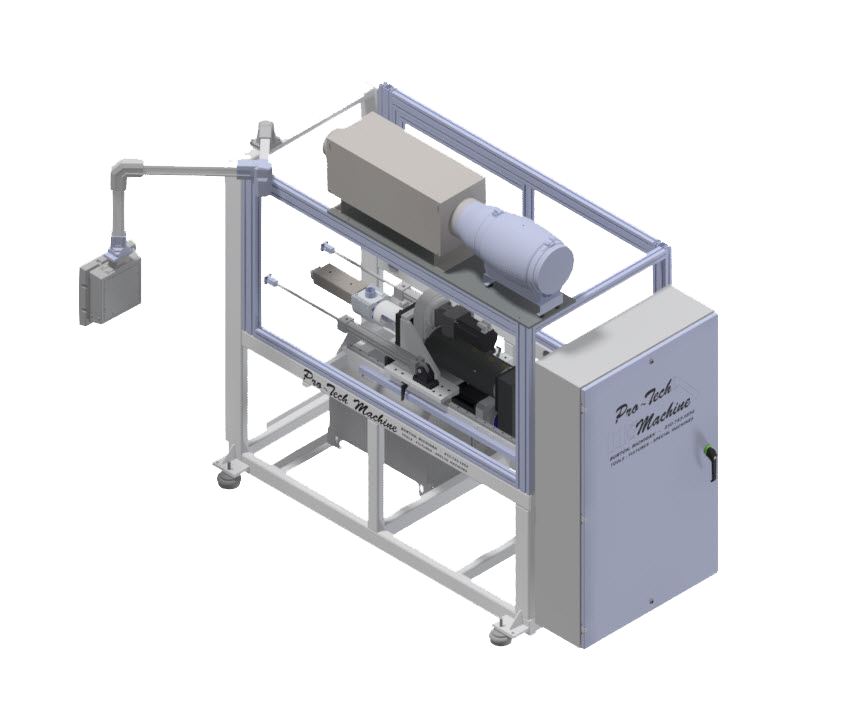
These defects were primarily attributed to a lack of control, poor positional accuracy, and an inability to adapt to the varying specifications of different components, such as plastic quality, temperature, and humidity.
Faced with this critical issue, the manufacturer sought a solution that could deliver reliable, precise processes while offering the flexibility needed to accommodate diverse production demands. Enter Promess, a pioneering force in manufacturing automation solutions.
Understanding the manufacturer’s needs, Promess collaborated closely with their engineers to develop a groundbreaking solution: the Injection Molding Machine. This innovative solution boasted fully programmable control of both linear and rotational motion, equipped with integrated, in-process position, force, and torque sensing capabilities. Moreover, the machine’s flexibility was enhanced by its ability to integrate additional sensors, such as pressure and temperature, as required.
At the core of the Injection Molding Machine lay Promess’ proprietary REMAP (Rotational Electro-Mechanical Assembly Press) system. This sophisticated system combined encoder-based rotational and linear motion with Promess’ patented reload algorithm, empowering manufacturers with programmable control and easily adjustable process parameters. Furthermore, in-process monitoring and gauging ensured meticulous verification of every production aspect.

The implementation of Promess’ Injection Molding Machine yielded remarkable results for the manufacturer. Instances of short shots were drastically reduced, thanks to Promess’ reload algorithm and the kit’s infinitely adjustable process parameters. Moreover, when issues did arise—often due to incoming quality variations or other external factors—the manufacturer possessed comprehensive insights to swiftly contain and rectify the situation, thus averting further quality concerns.
The outcomes of adopting Promess’ solution were profound. Manufacturers could now furnish their customers with undeniable proof of top-tier component quality, backed by hard, traceable data. Additionally, this data served as a catalyst for internal process refinement, leading to potential cost reductions alongside a significant decrease in scrap rates.
The collaboration between the manufacturer and Promess stands as a testament to the transformative power of innovative automation solutions in the automotive industry. By prioritizing quality, precision, and adaptability, manufacturers can not only meet but exceed the exacting standards of their customers, driving success in an ever-evolving market landscape.
Learn More: Injection Molding Machine