There are plenty of “dumb” systems out there which can press parts together. Pneumatics and hydraulics have been used to do just this for longer than most of us have been alive. Human operators, while not dumb, present problems of their own. Even if all of the factors outside of the assembly itself are performing as they should, even slight variations in the components going into the manufacturing process can cause significant differences in the outcomes. In order to achieve a consistent, verified, perfect press fit, every time, a few factors must come together:
- The apparatus doing the work must be CAPABLE of precision and consistency.
- The system must be “smart” enough to recognize any inconsistency.
- And the process must be nimble enough to respond quickly with corrective action.
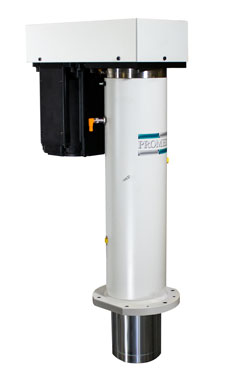
On the first point, pneumatics and hydraulics can be fairly consistent, but precision is usually out of the question. In most cases, components are smashed or driven together until the pressure exerted can no longer overcome the resistance. Unfortunately, with regards to the second point, there are countless factors which can affect just when this point is reached, and these processes, on their own, cannot account for all of these factors. (Most of the time, they cannot even account for ANY of these factors!) Older, “dumb” systems can be IMPROVED with high quality external sensors such as piezoelectric force transducers and analog position transducers, connected to quality monitoring software, so you can at least know if things went right or wrong, but this still does not allow them to respond to, correct or prevent the problems that are sensed.
A smart system, such as the Promess Electro-Mechanical Assembly Press (EMAP), with closed-loop feedback, can not only sense outcomes which are outside of a certain tolerance range, but can compensate “on the fly” to ensure that unacceptable assemblies are not produced in the first place. Here’s how it works:
- With unit in station, part to be pressed is loaded.
- Press ram moves rapidly to a point above the part, and then slows down until a touch point is reached.
- Part is pressed until precise position or force is reached, compensating for high force, low force and deflection as needed.
- Using the press ram encoder and/or analog position transducer, along with load cell(s), the quality monitoring software returns a force over position graph.
- Limits are placed around the curve on this graph and it is gauged to determine whether or not it falls within acceptable ranges
Promess’ Intelligent and responsive UltraPRO System, in conjunction with the Promess EMAP, is used to press to a precise position and/or force every time. So, how does one achieve a perfect press fit every time? Smart and responsive motion control with closed loop feedback is the answer.
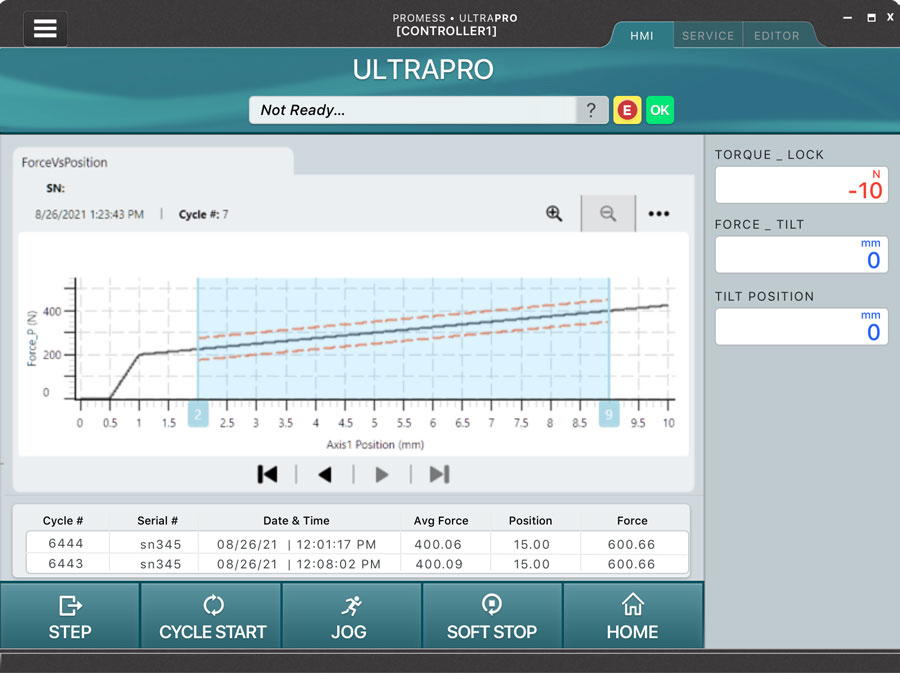