By Glenn Nausley, President, Promess, Inc.
Hydraulics have been the technology of choice for aerospace actuators almost as long as the industry has been in existence, but that’s now changing very rapidly. The trend today is strongly toward replacing hydraulics with advanced electric actuators utilizing new permanent magnet materials and sophisticated electromagnetic designs.
The primary driver is weight. Hydraulics are very power dense at the point of application, but the fluids, pumps, motors, piping, valves and actuators make the overall system heavy.
In an industry where every pound can represent thousands of dollars in annual fuel cost the weight-saving benefits of today’s electric actuator technology are compelling. For example, it’s been reported that American Airlines saved $1.2 million annually simply by replacing a 35-pound paper manual with an iPad.
Another, not so obvious benefit of electric actuators is that they easily can be configured to generate both power and real-time data that can be used for control, diagnostics and performance analysis. As modern aircraft increasingly utilize “fly-by-wire” technologies that integrate human and computer controls, feedback data from electric actuators provides essential system inputs to close the loop.
Aerospace and Aircraft Applications
Given the clear advantages of electric actuators in many aircrafts and aerospace applications, it’s only a matter of time until the technology used to control aircraft migrates into the systems used to build aircrafts. Here again, hydraulic applications still dominate many manufacturing and assembly processes, but electric technologies are challenging that dominance with a set of compelling benefits.
As an example, let’s look at the process for assembling ball joints, a relatively simple but widely used component in aerospace systems. Many of those applications are critical to the safe operation of the aircraft and proper function literally can mean the difference between life and death. Every ball joint used in a critical mechanism absolutely must operate smoothly and reliably with minimal lash and articulation resistance within very tight specifications.
Traditional Ball Joint Assemblies
The traditional ball joint manufacturing process uses a hydraulic press to form the cup around the ball. The product is then tested to determine if it meets functional specifications. Assemblies that fail are scrapped, wasting costly materials, labor, time and money. It’s not a very efficient system, but it’s the only one available to manufacturers using the traditional hydraulic press- based assembly process.
Replacing the hydraulic press with an electrical actuator, however, creates a system that produces ball joints with virtually identical functional characteristics and almost no scrap. By combining the control and decision-making power of modern computers and software with the precision of servo-controlled electromechanical devices, such a system can measure and adjust the functional characteristics of a ball joint while it’s being assembled.
Lash and articulation resistance are determined primarily by the fit between the ball and cup which can be tested by articulating the ball while the joint is being assembled and monitoring the values. This is done easily with a pair of servo-controlled devices, an instrumented electromechanical press and an instrumented torque application and measurement system controlled and monitored by a computer running analytical software.
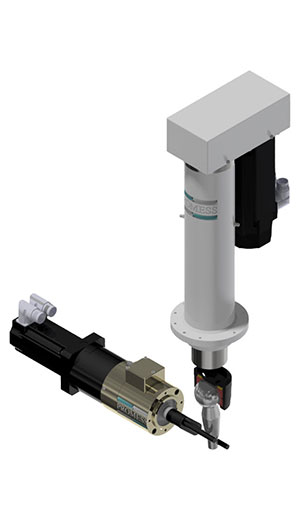
My company has built a number of ball joint assembly systems using our Servo Press (EMAP), TorquePRO and UltraPRO multi-axis controller.
The Servo Press (EMAP) is a press consisting of a ballscrew driven by a servomotor and equipped with an array of sensors to measure position, force, and any number of other process parameters.
The TorquePRO combines a servo motor and torque transducer in an integrated torque spindle package that delivers plug and run functionality.
The UltraPRO is a very powerful multi-axis controller running both servo-control and patented force/position signature analysis software.
Once the parts are loaded the EMAP moves down to the pre-programmed initial engagement point and the onboard sensors send position data to the control. That data is used to compensate for dimensional variations before the EMAP is advanced to begin forming the cup.
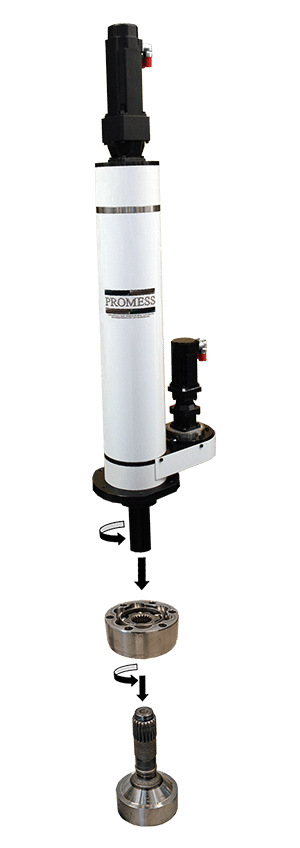
As the cup is formed, the TorquePRO articulates the joint through a programmed set of motions and resulting torque values are monitored, communicated to the UltraPRO and stored. This real-time data is used to control the ultimate functional characteristics of the joint.
Suppose the articulation force is too low which indicates a loose crimp. In that case, the EMAP is cycled again using a Move-To-Force algorithm rather than the initial Move-To-Position operation. The articulation force is measured while the EMAP presses the cup and the Press-Measure-Press process is repeated until the specified articulation force is achieved.
The TorquePRO can even run a short “wear-in” routine on the finished ball joint and then re-test the articulation force as an additional quality control measure. All of the data generated during the assembly process can be captured and stored to provide individual ball joint traceability and forwarded to other systems and/or other quality software packages.
As noted above, the data generated by an electric actuator is a serendipitous benefit of the technology that delivers extra value at no additional cost. There is a similar benefit associated with the kind of electrically-based assembly technology used in the ball joint manufacturing system just described.
That benefit is scalability.
Because the components used in the assembly system are standard off-the-shelf items, they are easily combined to produce interchangeable workstations. In practical terms that means that the system developed to prototype a product also can be used to produce the product.
As demand increases more identical workstations can be added without any additional design or engineering expense. Later, as demand decreases, workstations can be removed and re-purposed for new and/or different products. And, when the product reaches the end of its lifecycle one or more workstations can be placed back in production as needed to meet the long-term demand for service and replacement parts without tying up capital in a system that is only used occasionally.
The building block approach also offers uptime advantages because each element is independent. So, if one station requires maintenance the whole system doesn’t need to be shut down.
Unlike hydraulic systems that require constantly running pumps whether or not the actuators are being used, electrically-based systems only use power when they are actually functioning. That can generate significant operating cost savings.
Electric actuators rapidly replacing hydraulics in the air and in space. It’s only a matter of time until that’s true on the ground as well. The benefits simply are too compelling to ignore.