There are many different ways of testing gears and the assemblies in which they are incorporated.
Functional Gear Assembly Testing
Functional gear assembly testing could be defined as a series of tests that simulate the intended function of the product in an effort to determine whether an assembly operates within a specified performance range; quite simply, a method to test how well the assembly will function once it is applied to its intended purpose. In the gear world, unique methods coupled with advanced technology have lead to gear assemblies of exacting standards and unbelievable reliability and performance. For example, if a gear mesh is too tight then the gear assembly will function a certain way. If it is too loose, then other characteristics will be present. All of these nuances or differences contribute to how well an assembly functions in the “real world.” Current technologies can sense these insignificant differences and determine whether a part is acceptable or not before it leaves the production line. Coupled with data storage and part tracking, this now makes it possible to prevent “bad assemblies” from ever making it farther into the production process. This approach not only drives improvements and understanding, but it also adds value to each and every assembly produced, with the added piece of mind of knowing you’ve created an assembly that will function in a way that meets or exceeds customer expectations.
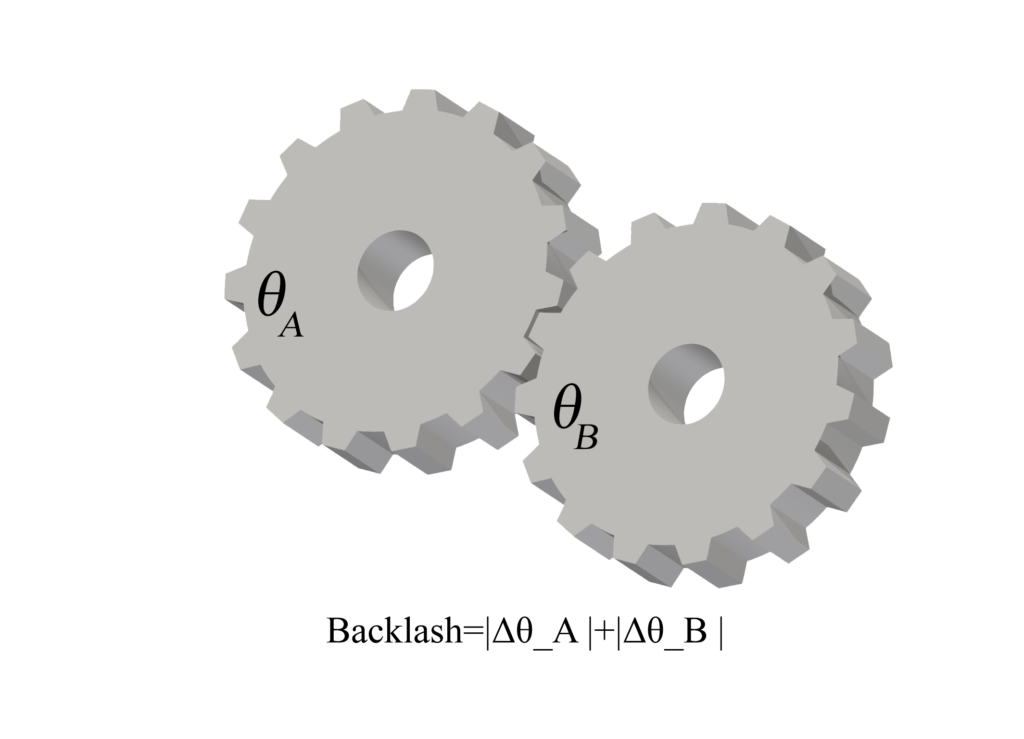
All functional characteristics derived from a particular gear assembly can be tested in one form or another, from differentials used in automotive drive trains to precision gearboxes used in wind energy. Take, for instance, automotive differentials. It is critical to know the amount of backlash developed with a certain amount of torque applied. In the real world this equates to how much “play” your vehicle is going to have in the power train, which will result in inefficiency and undesirable noise. In a windmill gearbox it is critical to have a minimal amount of effort to drive. Both of these examples can be functionally tested with various methods to determine how the gear assembly will work when applied to its intended application. There’s a whole litany of gear assemblies that are functionally tested, ranging from components that make up various drivetrains—such as differentials used in front or rear axles—and sun gears used in a transmissions to steering boxes that make up complete steering gears. Other applications including planetary gearboxes used in ballscrew press applications, low friction gearboxes used to create energy, or large PTO gears used in farm equipment.
There are several tests commonly performed, including backlash, measured effort, system efficiency, transmission error, and acoustical measurement. These tests are typically used to determine the functional level of a gear assembly. All of these tests are good indicators for determining whether a gear assembly will perform to expectations and beyond.
Backlash Testing
Backlash testing can be separated into two methods: static, and dynamic. In static testing the output (final driving gear) is held in a fixed position and torque is then applied in both directions to the input (driving gear) position values are captured and then stored. The difference of the captured position values becomes the static backlash of one gear mesh point. This will then typically be done in several other locations, and this measured movement is considered static. During dynamic testing the gear assembly is rotated to incorporate all gear-tooth combinations. All position values are then captured, stored, and plotted in both directions. Each position value is then compared to the corresponding one in the other direction to find the largest significant difference, the smallest significant difference or potentially any other difference that is relevant to determine whether the assembly is functionally capable.
Measuring the amount of effort it takes to turn a gear assembly—also known as torque to turn—is another common test performed on gear assemblies. Methods may vary, but they typically consist of measuring the input, output, and the forward and/or reversing torque in some combination or another. Once captured and plotted these values are then used to determine if the assembly falls within a certain threshold. High, low, and average torques are typically also captured, and limits may put around these values, as well as being used as locations on the gear assembly to perform additional static backlash tests.
Gear Efficiency
Gear efficiency is often another test that can help to determine if a gear assembly is functioning at an acceptable level. The efficiency of a gear assembly is calculated by measuring the torque required to drive the input (driving gear) against a resistive torque being applied to the output (final driven gear). This ratio is known as efficiency. Additionally, varying the resistive load applied to the output will also determine if the efficiency of a gear assembly is affected by the level of load it has drive.
Acoustical measurements can range from measuring the noise in decibels as the gear assembly is being driven to sensing vibration generated while the gear assembly is rotating. Although it’s not as commonly tested in the production environment, it’s still a valid test to perform; after all, who wants to listen to a noisy gearbox?
The amount of error in one revolution of rotation in a gear assembly can be defined as transmission error, which is often tested in gear assemblies such as planetary gearboxes. Transmission error is typically induced into a gear assembly from variations in tooth dimensions, high torque, and wind-up. For example, if a gearbox has a one-to-one ratio from the input to the output, one revolution on the input should equal one revolution on the output, and 90 degrees on the input should be the same on the output, and any error generated during one revolution is considered transmission error. This is often tested to measurements as finite as tenths of a degree, or just a few arc minutes.
Current technologies used to develop gear-testing equipment have improved drastically over the past few years. Higher sampling rates for electronics and sensors built into smaller packages have allowed systems to be developed and integrated with greater ease than in the past. Some of the current technologies used to perform these tests can range from various sensors fed into a PLC to complete closed-loop servo systems that control motion as well as take in multiple sensors. As with most things, though, you get what you pay for. Sensors to measure torque, displacement, vibration, and acoustic emissions are commonly used to test a gear assembly, and configurations can range from one to all being used in some configuration or another. Some of the more sophisticated systems will create torque vs. angle graphs, while simple systems will only capture single points during the test. Understanding the customer’s needs and expectations are mandatory to successfully function testing a gear assembly.
Sensors, electronics, and software are all key components used to make up a system. Sensors typically consist of high accuracy digital encoders for positional feedback, strain gauge based force sensors for torque measurements, and quartz based accelerometers for vibration, just to name a few. Sensors need to be able to accurately measure “on the fly,” and oftentimes with high-speed duty cycles, which in turn translates into the need to use to highly sophisticated electronics. Electronics used in gear testing applications require the capability to take in more than one sensor and the ability for higher sampling rates. Another often overlooked and rather complex aspect of a test system can be the software. Software should be developed in a manner that is intuitive as well as flexible enough to make changing parameters and limits simple and easy to understand.
Turnkey Solutions
Many companies now offer turnkey solutions that incorporate everything required, including software, electronics, cables, and sensors. The result from increasing demand for turnkey solutions has cropped up into something of a niche industry.
Companies that now specialize in turnkey test systems often end up eliminating the unique “cobbled together” solution. These turnkey systems not only offer ease of installation, but also one point of contact when issues arise. Turnkey systems are often flexible enough to perform the various tests required, with software that is intuitive enough for most manufacturing engineers to grasp and maintain, and with the reliability needed to minimize downtime and cost in the production environment.
Integrating and applying the technology to the process is another important aspect of a “functional gear tester.” Machines need to be built like a gauge.
Precision fixturing and tooling need to be designed in a way that they’re able to couple and move with a minimal amount of friction and misalignment. Any induced friction will cause readings to skewer, and misalignment will cause side loading. This induced error is going to be measured, and sometimes amplified, by the sensors. This will be in addition to the values captured during a specific test, thus causing a potentially good part to be a bad part. For example, if there is induced side loading to the part this can cause higher torque values, which would result in larger backlash numbers. This variation can be the difference between a good and bad part. So the initial side loading can influence the results in a very negative way.
The location of the sensors used is another important factor to consider when building a machine to function as test-gear assemblies. Sensors should be located as close to the part as possible. Anything in between the sensor and the part—such as moving parts like tooling—is going to be measured, so keeping the sensor as close to the part as possible will minimize unwanted measurements.
With careful research in test equipment, along with a clever mechanical design, the result is a function tester that is a long-lasting, capable piece of equipment. Proven technology, innovation, and a little creativity go a long way toward incorporating function testing successfully into the production environment. Many companies are starting to realize the real cost savings associated with fully testing a part’s functionality, and not only in gear assemblies but with many of the parts, components, and assemblies produced in all facets of industry. It all comes down to whether the initial cost outweighs the real added value. Keep in mind that we all sleep better at night knowing the product we produce is going to function to the best of its ability, and with the data to back it up.