“… when perfection gets in the way of productivity, it’s time to consider an alternative. A couple of years ago, I started saying “Good enough” and it’s transformed my . . . life.”
Chip Scanlan
The Poynter Institute
“Quality” has been the holy grail of manufacturing for more than 40 years now, and it is a worthy goal. But, somewhere along the line the concept of “quality” became inextricably tied to the concept of “perfection” and the result has been a cascade of unintended consequences, not the least of which is the dawning realization that with perfection as a goal the cost of success may well be greater than the cost of failure.
The good news is that it doesn’t have to be that way. The bad news is that turning things around is going to take a great deal of courage and innovation on the part of the world’s manufacturers.
What’s Wrong With Quality?
In a word, nothing. Quality isn’t the problem. The problem is the way manufacturers have chosen to achieve quality by single-mindedly pursuing perfection in all of the components that go into an assembled product.
It’s only a slight exaggeration to say that manufacturers today are routinely specifying tolerances that couldn’t even be measured in the 70s when all of this got started. And, yes, the machine builders and process designers have responded with tools and systems that are capable of meeting those tolerances, and the even tighter ones that are sure to follow.
But, someone has to pay the price for all that precision, and the price tag grows larger each time tolerances become smaller. That someone, of course, is the consumer who will ultimately decide just how much “quality” is worth. It seems a safe bet that the customer won’t be willing to pick up the tab for perfection even if it were possible to produce it.
What’s The Alternative?
The first step is to consider just what “quality” means to the consumer. In most cases it means the product works as expected and lasts long enough to deliver reasonable value. That’s a long way from perfection, and it’s as far as a successful manufacturer needs to go to keep their customers happy.
Getting there will require re-thinking many of the procedures and processes used in manufacturing today. The consumer doesn’t care if all of the components in a product were machined to sub-micron tolerances before assembly, all that matters is that the product functions as expected and doesn’t wear out or break prematurely. Function is the ultimate measure of quality, and consistent, reliable function ought to be the goal of manufacturing and, especially, assembly operations.
Today, manufacturers are spending a lot of money to produce near perfect components so they can assemble them with simple, “dumb” systems using inexpensive tools like hydraulic and pneumatic presses and still get an acceptable level of quality. The alternative is to spend a lot less on components that are “good enough,” and invest part of the savings in “smart” assembly systems and tools that can use those components to achieve the same level of quality at significantly lower overall cost.
Smart Presses
The first requirement is a press that can be controlled precisely and instrumented easily to provide feedback on the operation it is performing. For several reasons that’s not easily done with hydraulic or pneumatic presses.
It is, however, relatively easy to do with an electro-mechanical press using a servomotor to drive a ball screw ram. The servomotor is connected to the ram with gears, or, more often, a timing belt so there is little or no backlash in the system. The encoder on the servomotor will then provide a precise measurement of the ram’s position.
My company, Promess, Inc., makes Electro-Mechanical Assembly Presses (EMAPs) in 33 different sizes with outputs ranging from 25 lbs. to 125,000lbs. and strokes to suit most assembly operations. These units, and similar presses made by other manufacturers, are widely used as the basis of intelligent assembly systems in the automotive, appliance, and other high-volume manufacturing industries.
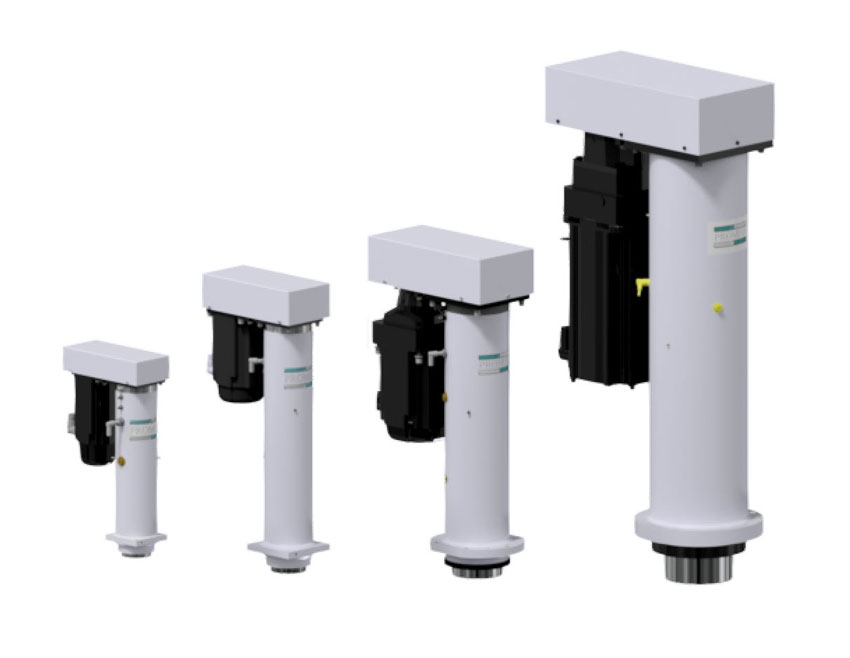
Automotive Press Application
To see how a “smart” press can improve even a simple operation, consider a system used to install studs into automotive wheel hubs. Due to manufacturing variables, the force needed to seat the studs varies from stud to stud and hole to hole, so the conventional answer simply is to set a hydraulic press to the highest force needed to insert a stud in the worst case, and hit them all that hard. The result is a lot of overstressed and bent hubs in the scrap pile because the “dumb” assembly system treated them all the same.
The traditional solution to this situation would be to tighten the tolerances on both the studs and the mounting holes and thereby avoid much of the scrap. But the increased cost of the components quickly outweighs the savings gained by reducing the scrap rate — a classic case of success costing more than failure.
The alternative is a smart system using an EMAP equipped with force and position sensors to monitor the insertion process, and a controller that can decide when the operation has been completed successfully. By setting upper and lower limits for the process variables, the manufacturer can reject assemblies likely to fail in customer hands, while producing a much higher proportion of good assemblies — even with less expensive components with much looser tolerances.
To make this work, one needs to install a load cell either on the EMAP’s ram, or in the fixture, to measure the amount of force being exerted on the assembly as the stud is inserted, and an encoder on the servomotor to measure ram position in real time. With these two pieces of information, force and position, one can then create a “signature” of the process by plotting one against the other.

If the baseline operation is performed with parts known to be within specification, the signature will define the parameters of a good assembly operation, and any subsequent operation producing the same signature will also produce a good assembly. In such a system, quality assurance means simply accepting all assemblies that match the signature and rejecting all those that do not.
Smart Assembly Systems
Obviously, the real world is a lot more complicated than that. To make this approach practical, a significant number of operations both good and bad must be measured to establish upper and lower limits for acceptable signatures. Then, the EMAP must be connected to a controller able to both generate and evaluate the signature in real time while the operation is performed.
Fortunately, the presses and controls are available off-the-shelf, and the balance of the system consists of the same sort of fixturing and material handling components that would be used in a traditional dumb system. Once all the elements are integrated, the only “custom” aspect of the system is the work required to establish the signature benchmarks and program them into the control. Again, these are very simple operations.
A Smart Approach To Quality
What works for wheel studs also works for assembly operations on products as diverse as automotive hood latches, medical catheters and pacemakers, even hydraulic valves. In the case of the hood latch, an EMAP is used to peen the rivet that holds the latching hook to the baseplate while a motorized torque system cycles it. When the force needed to move the hook is “just right” the peening operation stops.
Here, the smart system replaced a hydraulic press that simply peened all the rivets with the same force. Then employees had to manually “wiggle” the assemblies to discard any that were totally immovable, and “work in” any that were salvageable. Their experience was used to establish the baseline for the amount of force that was “just right” when the smart system parameters were established.
In the catheter assembly operation an EMAP-based system virtually eliminated separations of a critical press-crimped joint with a history of failures, sometimes inside patients. This system replaced a hydraulic press that the customer found impossible to calibrate with sufficient precision to produce good assemblies reliably.
Here, the signature included data on both force and tool position during the process, since both too-deep and too-shallow crimps are prone to failure. The result is a 100-percent effort test certification for every catheter produced, and the virtual elimination of crimp failures in the field.
A similar EMAP-based system is used to crimp electrodes to the leads of cardiac pacemakers. And yet another is used to calibrate hydraulic valves by adjusting the pre-load on the spring holding the poppet down against system pressure.
None of these assemblies, or the hundreds of others produced on smart systems, are perfect by any measure. What they all are, however, is 100 percent functional and reliable in the hands of customers who measure quality in terms of performance delivered for the price paid. And, measured that way they are probably as close to perfect as anything made by human beings is likely to get.