The trend toward consolidating suppliers and buying modules or assemblies rather than parts is well-established and accelerating across a broad range of industries.
It started in aerospace, where typically up to 70% of each aircraft produced today is made by suppliers. It’s common for an aircraft manufacturer’s quality control team to be resident full time at major suppliers where they are actively involved in resolving workflow and product performance issues. The goal in the aerospace industry is to do final assembly in the manufacturer’s facility, and little more. All of the real manufacturing is being pushed as far upstream as possible, as quickly as possible.
Clearly, the future belongs to those who can make the transition from parts to assemblies while still meeting quality and productivity benchmarks that are also rapidly growing more stringent. The good news is that technologies are available to ease the transition, and perhaps even make the new upstream assembly operating model more profitable than the old one.
These technologies are the basis for smart assembly systems based on a combination of servo-control, real-time force and position sensing, and fast, computer based monitoring and feedback. This combination offers suppliers a whole range of new solutions to perennial manufacturing problems.
Automotive Industry
An example from the automotive industry illustrates the impact smart assembly technologies can have. Automotive control arms are made of components that cannot be produced economically with very close tolerances, yet they require geometric precision to achieve proper function. They consist of a triangular, heavy-duty stamping and two rubber-cushioned bushings which are pressed in place at each corner.
Automotive designers typically specify the geometry of the finished assembly, but leave it up to the supplier to figure out how to produce it. This is known as specifying a “phantom” dimension, and it’s quite common in many industries.
Traditional Solution
The traditional solution is to build very precise tooling that is continuously adjusted to compensate for the unpredictable variations in the component parts of the assembly. The alternative is “press-hope-measure-sort-scrap” which is about as efficient as it sounds.
Smart Solution
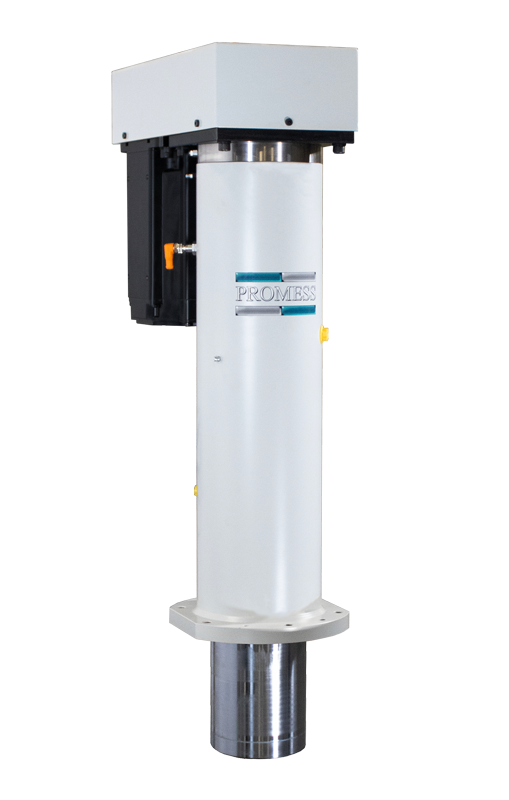
The ‘smart process’ solution uses two Promess Electric Presses (EMAPs) mounted at each corner of the control arm. The assembly is located on the pre-installed ball joint and shock absorber stud and the EMAPs then install the bushings in a “push-measure-push” process controlled by force and position sensors and a fast computer doing real-time analysis and feedback.
Since the process is controlled in real-time based on actual bushing position, it is completely independent of variations in bushing resilience and all but the largest errors in bushing and control arm dimensions. Using signature analysis, which compares the force/position signature of the current operation to that of a known-good operation, it is possible to produce virtual “clones” of the known good assembly with 100% assurance.
All of the elements of this smart system are available off the shelf. The EMAPs are essentially servo-driven ball screw presses equipped with force and position sensors. The control is a standard, PC-based CNC running a signature analysis algorithm that has been used in literally hundreds of applications. Everything else is essentially standard.
One of the less obvious benefits of the move to upstream assembly is the freedom it gives to the supplier. The build-to-print model often locks the producer into an inflexible “tolerance straight jacket” that defines quality in terms of the number of zeros in the size tolerance. With a smart process assembly system, though, the actual size of the component parts becomes much less important because the system can compensate for a broad range of variation and still produce 100% functional assemblies. Using such a system it often is actually possible to open the acceptable tolerance range for component parts and still meet stringent functional quality goals for the finished assembly.
For the traditional part supplier making the move to upstream assembly, the choice of a smart process assembly system can significantly smooth the transition. The system’s built-in intelligence can help compensate for the lack of assembly experience within the supplier’s workforce, and reduce, or even eliminate, the need to hire assembly experts to handle the new requirements.