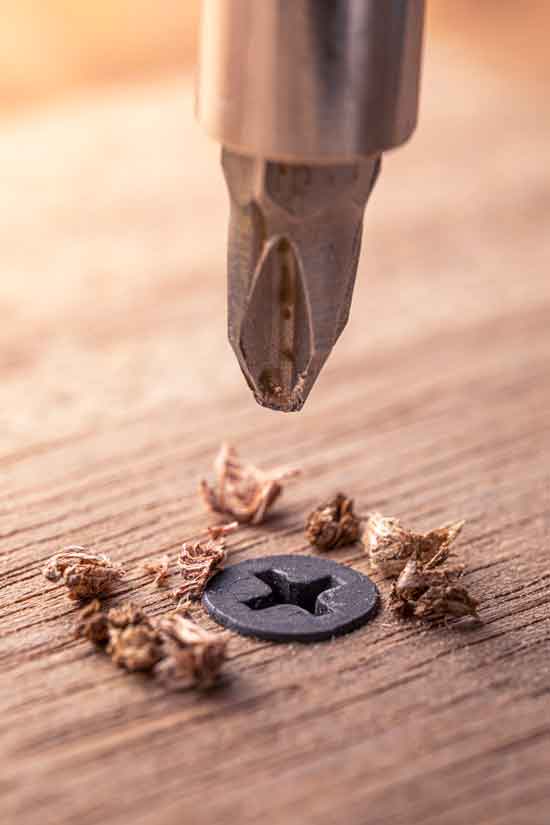
Imagine you’re developing a new product that requires precision compacting of powders into near-final shapes before sintering and assembly. Typically, your development team will use a collection of off-the-shelf components to cobble together a system to do a production and assembly proof-of-concept. Then, once all the bugs are worked out, it will be up to your manufacturing engineering team to figure out how to produce the product in volume using an entirely different system with its own set of bugs and challenges.
Drill Head Application using Programmable Presses
That was a familiar story for a Promess customer in the midwest who produces drill heads for mineral exploration, coring, mining and oilfield applications. The process for these particular drill heads involves compressing a carbon diamond powder mixture into a mold with forces up to 60,000 lbs. and holding this pressure for a set amount of time prior to sintering. The compacting force and dimensional requirements for the “green” components are critical process parameters.
In the past they would have used a hydraulic or pneumatic press in the lab and another on the production system, but this time they did the product development with a Promess Electric Press Work Station. The Work Station featured a 300 kN Electro-Mechanical Assembly Press (EMAP), which is a fully programmable, all-electric servo-driven press equipped with integral force and position sensors. These sensors that allow the process to be monitored and controlled in real-time.
Once the development was complete, they were able to use the same EMAP Work Station in the production system. The lab-developed process was exactly duplicated in production, because the lab machine really is a robust production machine. And because it’s fully programmable they use the same EMAP Work Station to press the finished inserts into the drill heads with force and position feedback to ensure consistent quality.
This is how a fully electric programmable press stations like the Promess EMAP Work Station saves time and money by enabling users to transition processes from the development lab to the production floor, seamlessly. While designed for the production floor, their programmability and built-in force and position sensing make them ideal for process development labs.
Benefits of Scaling Equipment from the Lab to Production
Using the exact same equipment in the process development lab as you do on the production floor offers many advantages, not the least of which is eliminating the often expensive and time- consuming task of re-engineering the production solution once the production equipment is available. An all-electric solution is also cleaner, quieter and much more energy efficient than a hydraulic or pneumatic alternative.
Programmable electric press technology has been used in the automotive industry for close to 20 years. The advantages are only now beginning to be recognized in the energy sector and other areas, but the compelling benefits of this technology assure its rapid and widespread adoption.
What is your application?
Talk to one of our expert engineers or learn more about proving your
application in our Process Development Center.