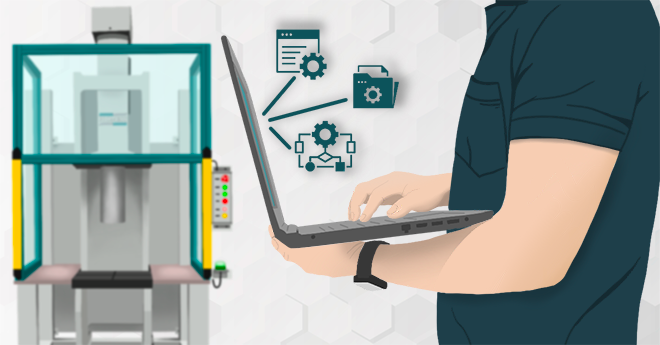
A Coca Cola machine on the campus of Carnegie Mellon University in the 1980’s is often held as being one of the earliest examples of the Internet of Things (IoT), even though the term IoT didn’t appear until almost a dozen and a half years later.
In the beginning, it was a curiosity for the initiated few. The Coke machine had been outfitted with a few simple sensors which could detect whether or not the machine was stocked, and if stocked, how cold the Cokes were.
These same sensors were connected via the internet, to be remotely accessed by the few individuals on campus who had internet access at the time, so they would know whether or not it was worth making the trip to the machine to get a Coke. As whimsical and frivolous as this endeavor may seem, its implications have been felt across the globe, in the military, in nearly every industry, and increasingly, in more recent years, in more and more households across the world.
Fast forward to today, almost 40 years later; our televisions, our automobiles, our smartphones, our refrigerators & other household appliances, nearly everything that is powered, has sensing and data-collecting capability, and nearly all of it is designed to be accessed remotely. We can close a garage door, turn a light on or off, or monitor our pets, our children, or our home security systems, all with the touch of a couple of buttons on our cellphones. Our auto insurance companies offer us discounts in exchange for access to remotely accessed data on our driving habits, and if our vehicles are stolen, or if we’ve simply forgotten where we parked, we can easily access their location, too.
In the manufacturing industry, the effects of the Industrial Internet of Things (IIoT) cannot be overstated. Machines used in automated assembly processes collect in-process data on their performance, and on everything they produce. One machine informs the next what has been done and what may need to be done for optimal further processing.
Data, collected and communicated through the Industrial Internet of Things, matters because it is the key to making informed decisions regarding improving the efficacy and efficiency of your processes, and data matters because it is key to verifying the quality of the assemblies that have been produced. Data collected through the Industrial Internet of Things can be used, also, for predictive maintenance, and maximizing the lifetime of your connected capital equipment.
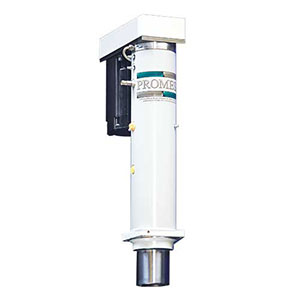
Not only is there tremendous potential for data, but the IIoT is proving itself to be a powerful force regarding control as well. The gains that have been possible regarding quality, efficiency, & productivity are nothing short of revolutionary. A few have made the argument that the IIoT, in conjunction with Cloud-based computing and data-storage, is well on the way to rendering PLC’s obsolete, while most experts agree that the two will exist side-by-side, symbiotically, for a long time to come. Whatever the future holds for manufacturing & automation engineering, we can be sure the Industrial Internet of Things will be a significant part of it.
Some manufacturing technologies will be relegated to the trash-heap of history and new ones will rise to take their place. And some that already exist, and that have perhaps even presaged the coming of the Industrial Internet of Things, such as Promess’ lines of smart Press & Torque systems with integrated sensing and data monitoring & gaging, will be integrated seamlessly as an integral part of tomorrow’s IIoT, allowing you to sit back and reap the benefits, perhaps while sipping from an ice-cold can of Coke…