Valve manufacturers today are able to inspect parts during assembly rather than after to produce near-perfect fluid pressure relief valves. The Promess Electro-Mechanical Assembly Press (EMAP) uses no pneumatics or hydraulics; instead, press motion is initiated by a servomotor and ball screw. A computer monitors the press ram’s position and pressing force, and accepts data from additional external sensors. To make the pressure relief valve, the EMAP is fitted with an attachment that pumps fluid through the valve at 1.2 liters/min while it is in the press.
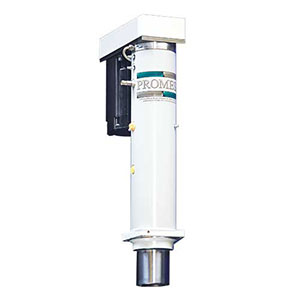
Sensors provide information on fluid flow and pressure to the EMAP’s controller. While the valve is assembled, the system monitors the valve release pressure. The EMAP compensates for variations in the valve components that affect release pressure by compressing the spring inside the valve to increase its resistance. The EMAP presses the valve seat into the valve body until the target release pressure of 1,000 psi is reached.
The new process lets the pressure relief valve company make valves with a plus/minus 2 psi tolerance.
Installation Report: Electro-Mechanical Assembly Press
Application: Pressure Relief Valve Assembly and Test
Customer: Valve Added Screw Machine Shop
Part: Fluid Relief Valve
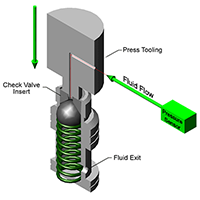
Reasons for Purchase:
- Reduce pressure tolerance from 1000psi to +70psi +/- 50psi
- Monitor press force of valve insertion
- Test while assembling to eliminate expensive test station
- Instant change over to new part
Results:
- Repeatedly pressed to 1000psi +/- 2psi
- Monitored force of valve insertion with signature printout of each valve
- Eliminated secondary test station and labor
- Increased throughput and quality at a reduced cost