Application
The most common assembly process for composite parts is compression molding. Material is inserted between coordinated metal dies and then pressed together under a high amount of force.
Challenge
The customer was previously using hydraulic presses and running into issues with inconsistent parts. The customer needed to be able to monitor the force and position throughout the process, while regulating the speed until the desired programmed force is reach. Then this force must be maintained for a specified time.
Solution
The Promess Platen Press and Promess UltraPRO controller were the only solution on the market with these capabilities. The Platen Press consists of two or more fully electric presses and a platen working together to provide force capacities of up to 2,000kN over a large area and the UltraPRO controller can coordinate the motion and force of the multiple axes to work as one. The Platen Press’ platen gives the needed surface areas for larger dies, as well as maintaining parallelism throughout the pressing.
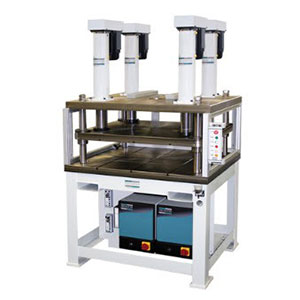
By using the Promess Platen Press and UltraPRO controller in the assembly process the customer was able to make consistent parts with added benefits of cost savings and simplification of the Station. Since the synchronization of the motion and the monitoring of the signals are done within the controller, a PLC was not needed on this station. This is a significant cost savings, not only from not needing to purchase the hardware, but also by not requiring someone to program and maintain the PLC logic, reducing the complexity of the station.
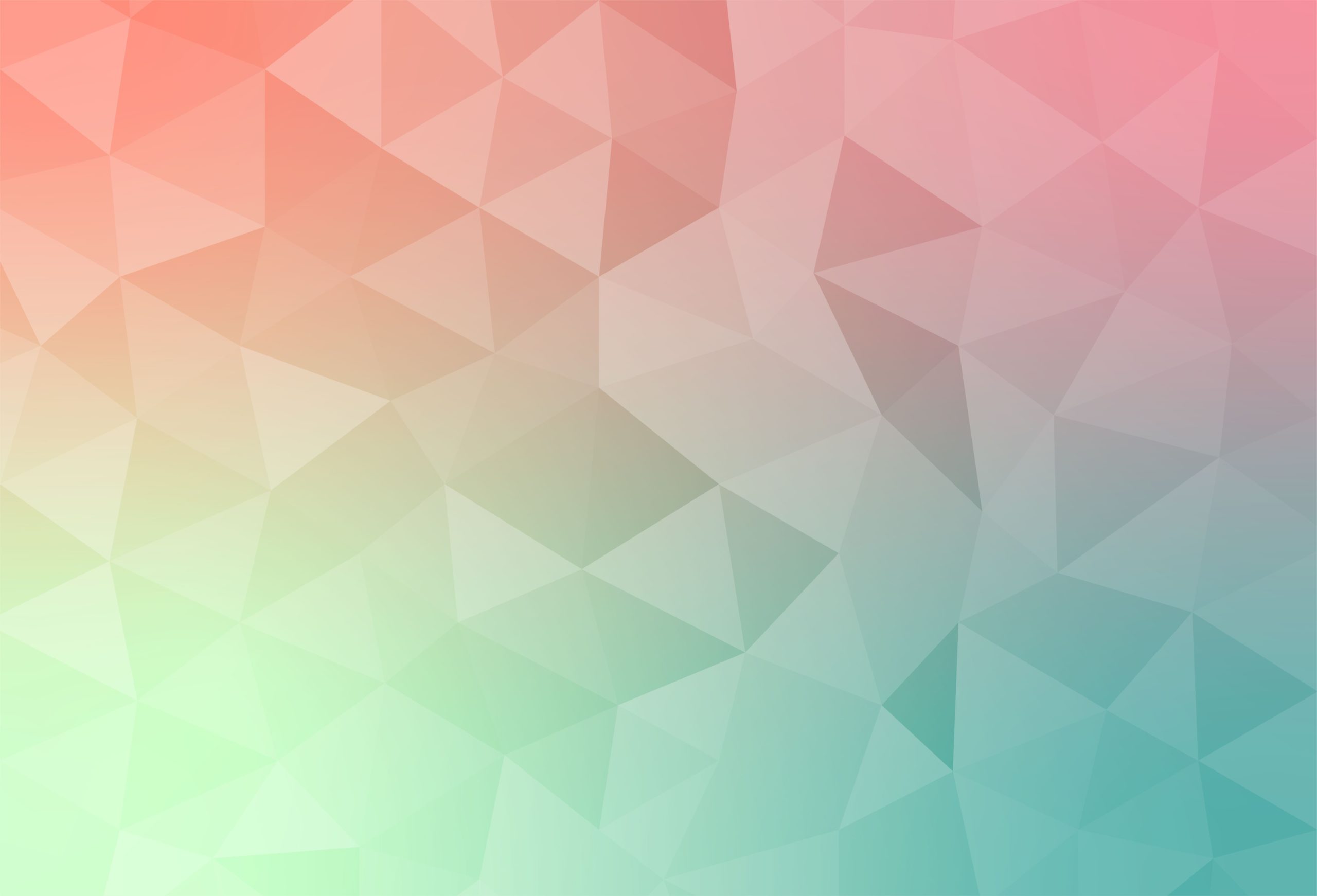