By: John Derry, Applications Engineer, Promess, Inc
An overly complex assembly process can become the downfall of what would otherwise be a successful project. The main areas that tend to add to the complexity of an assembly process are the initial design, the integration and setup, quality assurance along with maintaining and supporting the process for the lifespan of the assembly equipment.
Initial Design
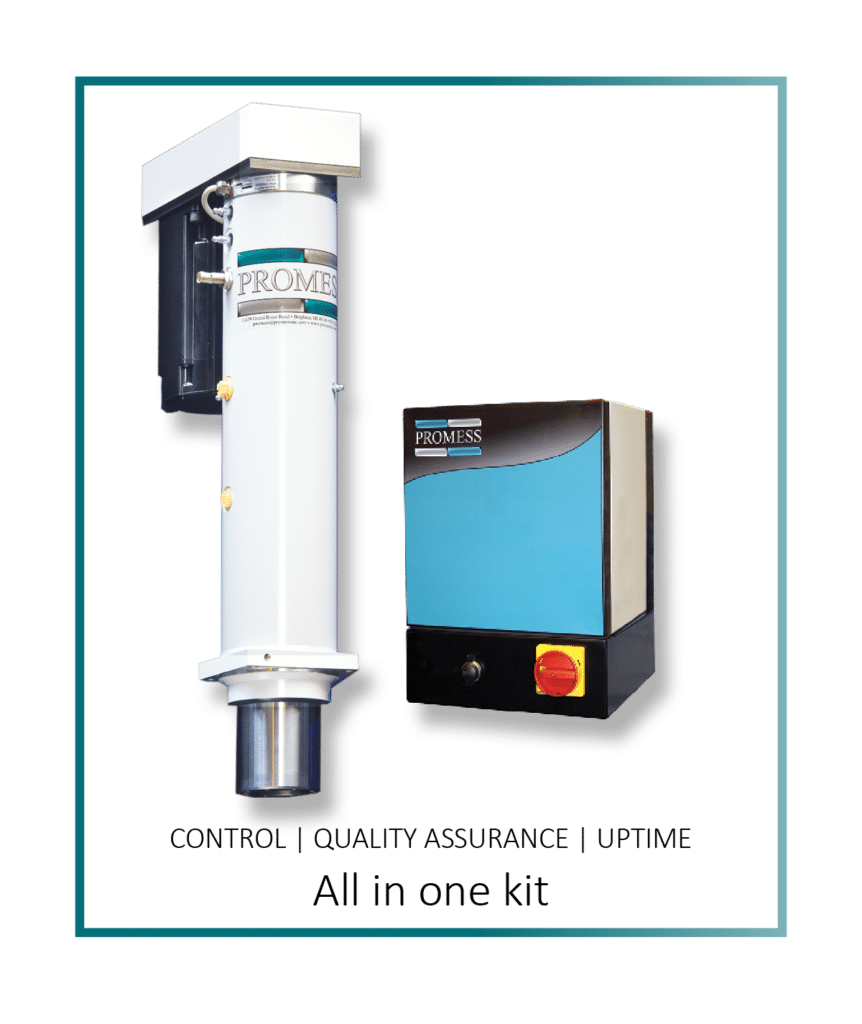
The Initial Design of an assembly machine can add unnecessary complexity to the process. Using different components, multiple controllers with unique interfaces and software often results in increased design time, mismatched components, and latency issues. Communication between these systems generally relies on an intermediate device such as a programmable logic controller (PLC) for translation purposes which increases complexity for each device. Promess is working to reduce the number of controllers required to perform an assembly process by utilizing our UltraPRO servo controller with multi-axis motion control capabilities, simple sensor integration and an intuitive, user friendly software.
Selecting robust components for an assembly machine during the initial design phase is one method to reduce support expenses and minimize machine downtime long term. Mechanically, a servo-controlled press should have a ball-screw with a load capacity that is at least is 2.5 X the dynamic range of the press. The drive train powering the servo system should also be sized appropriately. Many suppliers will skimp on the drive train to save cost upfront at the expense of long term robustness. Promess uses motors sized to work within the continuous current rating rather than requiring peak current to achieve rated press capacity. Robustness can also apply to the software used to control the system. Motion control and process monitoring should be integrated as much as possible to simplify the system configuration, this also lends itself to user-friendliness if changes to the software or process are required on the plant floor after equipment is installed.
Integration and Setup
A tremendous contributor to complexity is the implementation of an assembly process; expecting many different systems to work cohesively within a cell. Promess simplifies the implementation of the assembly process with our Electro-Mechanical Assembly Press (EMAP) which is a fully programmable, servo-controlled ball-screw press that has integrated force and positional feedback and can be equipped with a multitude of sensors to measure force, position, and any additional parameters that are integral to the process. The flexibility and reconfigurability of servo-controlled presses allow greater throughput and superior quality control capabilities while greatly simplifying the process.
Quality Assurance
A fundamental aspect in reducing the complexity of an assembly process is streamlining the quality assurance procedure. One approach to accomplish this is to begin assessing each operation or subassembly for quality rather than performing only an end-of-line style quality check. Every operation performed on a component or assembly adds cost. With the use of Promess Software in-process evaluation is possible allowing for parts that do not meet specifications to be caught before they are integrated into a finished product. Recognizing quality concerns earlier on in the assembly process reduces the rate of component scrap, recalls and potential legal issues, and it preserves your customer’s confidence in your expertise.
Maintaining and Supporting
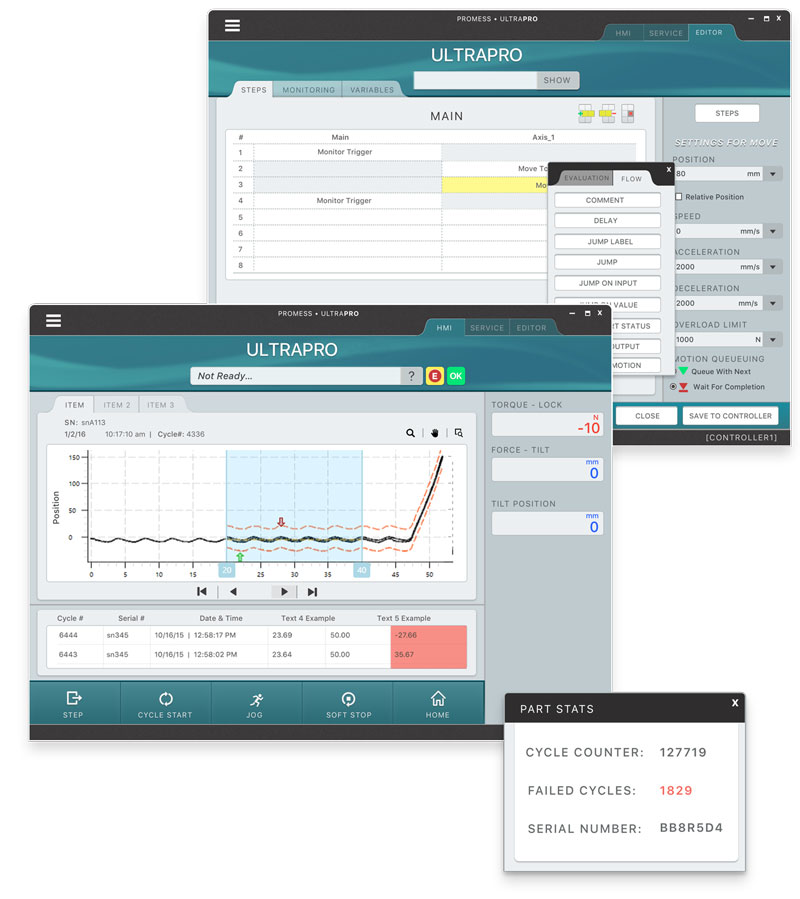
Maintaining and supporting an unnecessarily complex assembly machine is not only costly but can become time consuming. Time spent servicing assembly equipment is time that the assembly line is not able to produce parts and make money. Unlike hydraulic presses, fully electric servo presses reduce environmental impact by only consuming electricity while in use, not requiring hydraulic fluids that often have high toxicity and require much less maintenance reducing down time.