When an automotive starter needs to be replaced, it’s very likely that the most expensive components—the armature, commutator or gears—are still functional, or can be restored economically. Precision Parts & Remanufacturing (PPR) of Oklahoma City has been doing exactly that for more than 45 years, turning precision components that might have been scrapped in the past into OEM-quality replacement parts that can be returned to service with a warranty.
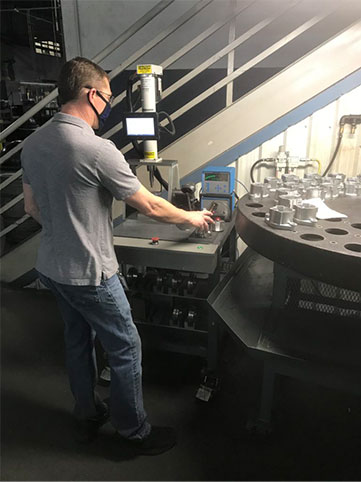
“Our customers supply remanufactured starters and alternators to many major automotive OEMs,” said PPR Product Engineer Daniel Anderson, “and they depend on us to deliver products that meet or exceed OEM standards for quality and performance. What started out as a ‘hammer-and- chisel’ operation almost five decades ago has grown into an increasingly high-tech business using validated computer monitored processes that let us track and record data down to the individual operation level.”
A good example of the way PPR has harnessed technology to replace manual operations is its use of servo-controlled electric presses. These presses automate assembly of the oil-impregnated bushings that support the starter motor shaft. The traditional process used an arbor press to install the bushings which were placed, located and pressed by hand.
“That worked until it didn’t,” Anderson said, “and there was no way to tell until a bad assembly became a warranty claim. Our customers do not like warranty claims and neither do we, so we started looking for a better way to assemble bushings.”
The requirements were simple—a repeatable process that generated tracking data for each part. The initial solution was a foreign-made, electric screw-type press. While that press represented an improvement over the manual arbor, it did not offer the data capture PPR was looking for.
“We came across the Promess Electro-Mechanical Assembly Press (EMAP) at a trade show in Chicago and it looked like the answer to our needs,” Anderson said, “It was more expensive than the foreign press we were using, but it also had significantly greater performance and data generation capabilities. It took some effort, but our management was persuaded to make the investment.”
Servo-Driven Ballscrew Ram
The Promess EMAP uses a servo-driven precision ballscrew ram. It is instrumented with force and position sensors to provide feedback to the controller. That feedback provides a complete “signature” of every operation, which in turn can be used for process control. The feedback data can also be stored for process validation and quality documentation.
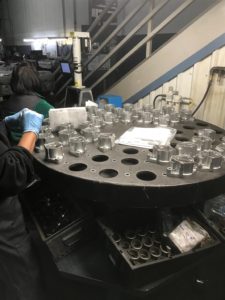
PPR processes automotive starters in standardized, 50-unit batches. While the EMAP was being installed in the new work station, Anderson’s team added bar code scanning to the control software they were writing. This was so data on the lot, quantity, employee and date were captured in addition to the operational signature of each part. Once the EMAP was installed, feedback data allowed the team to determine a maximum and minimum force level and the right contact height for each type of bushing placed.
The software also verifies that the correct bushing is being used, the correct tooling is in place, and the bushing is in the correct location. When all requirements are met, the press moves the tooling to contact the bushing and apply a nominal force prior to a final parameter check—then it initiates the pressing operation.
Once the bushing is installed, an air gage is used to measure the ID as a final verification of a successful operation. That data is added to the previously stored information on the individual part.
“If a customer calls about a particular starter, we can tell them how much pressure was applied to the bushing, exactly where it was located and what the ID was at the end of the process,” Anderson noted. “That hardly ever happens, though, because the system simply won’t process a bad part. If anything is out of spec it stops and notifies the operator.”
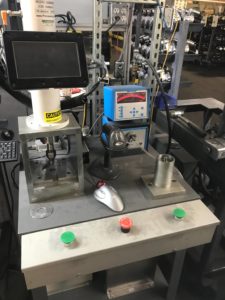
PPR now has three Promess EMAP systems for bushing installation. It is building a fourth to install an end cap on the drive body. The drive body contains the one-way clutch that disengages the starter when the engine starts. The end cap had been attached with a roll-forming process, but that sometimes allowed the cap to rotate, which did not meet the customer’s specifications.
“Pressing the cap is more consistent than roll forming it,” Anderson said, “and it doesn’t rotate at all. We proved the process the old way, with an arbor press, but we’ll use an EMAP for the production operation.”
One of PPR’s marketing goals is to develop more business from customers that require high volume spread over many small batches of starters. Anderson noted that serving a customer with 100 part numbers but only 10 or 15 batches of 50 each month is not practical with a manual operation. That is not true, however, with an automated process. An automated process only requires PPR to change dies and registers for each batch and load the correct program into the EMAP.
“Proving the process is a big issue,” Anderson said. “[That is] one of the reasons small batches aren’t really practical in a manual operation. But with the EMAP feedback data, I can generate a process capability report for a typical 30-piece sample in 10 minutes. That makes a difference, whether it’s a prospective customer or an existing customer who wants to change something.”
Manual to Automated Operations
The move from manual to automated operations has impacted PPR’s business beyond quality and productivity improvements. It is having a direct impact on employee retention and satisfaction as well. “It’s hard to find and keep people who are willing to do manual labor the same way it was done 40 years ago,” Anderson noted. “That leads to high turnover and high training costs that hurt profitability. The EMAP stations help solve that problem because they are clean, easy to use and require less operator training than a manual station.
“All the operator really needs to know is that a green light means put the part in one place and a red one means to put it in a different place,” he continued. “The software and EMAP do the rest of the job and ensure a quality outcome every time.”
Because its automated assembly stations are so efficient, PPR is now moving employees off individual shop floor stations and into producing “kits” to feed them. Kit production is housed in separate rooms with environmental controls designed to keep parts clean.
“Some of the parts have to be greased before they’re installed,” Anderson explained. “The cleaner working environment in the kitting areas helps prevent contamination. It’s also a lot better environment for the people working there, which helps with employee retention.”
Replacing Individual Work Stations
PPR is also installing assembly lines to replace individual stations for some of its parts. This is also impacting employee satisfaction.
“Instead of an operator performing the same job on the same part 50 times every day, we rotate them through the assembly line stations every day,” Anderson said. “That way they don’t get bored and each operator learns every facet of the process, which makes them happier and more valuable.”
Like all businesses, PPR has been impacted by the COVID-19 pandemic, which substantially reduced customer demand. Instead of laying off employees, however, PPR chose to retain them and build stock for inventory that will be needed when the economy recovers.

“We kept all but 10 or 12 of our regular employees,” Anderson said.
Conclusion
Based on the successful introduction of EMAP assembly stations, PPR is looking to expand its product offering to include an expanded line of alternators and motors for power windows, windshield wipers and power seats. However, automotive starters will continue to be the mainstay of its business while that happens.
“We sell quality while many of our competitors have moved production to Mexico so they can sell on quantity and price,” said Anderson. “When a customer buys one of their starters and it fails, they just replace it with another one. When a customer buys one of ours, it just works—and that’s a big difference.
“Modern systems like the EMAP stations and assembly lines have a lot to do with that and we’ll be using more of them in the future,” he concluded.
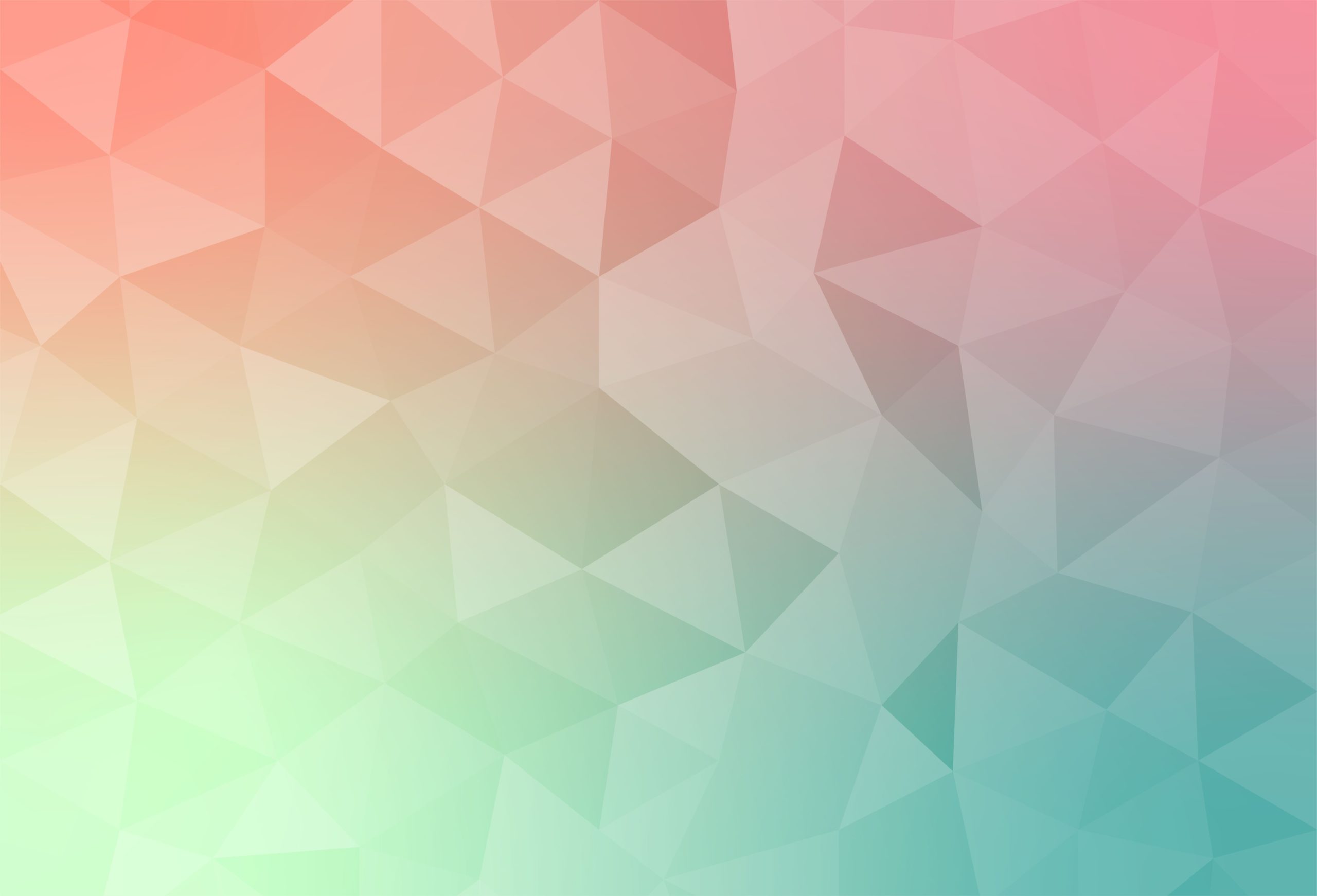