By: Lawrence Moebs, Applications Engineer, Promess, Inc
In modern manufacturing, from simple parts to complex final products such as automobiles and medical devices, bushings and bearings play an important role. Whatever material your product is made of, if it has any type of hole through which something else is routed, from wiring and cables to other smaller parts, chances are, you are using bushings and/or bearings.
Bushings vs. Bearings
A bushing is a simple device which is used as a spacer or guide for connecting fittings of differing sizes, or which acts as insulation so that the edge of the hole does not put unnecessary wear or stress on anything that passes through it.
A bearing is a slightly more complex device which facilitates movement through a hole or other tight space. Whichever your application calls for, having your bushings and bearings securely in place and verifiably assembled to the specs you and your customers demand, can make all the difference.
Focus on Quality
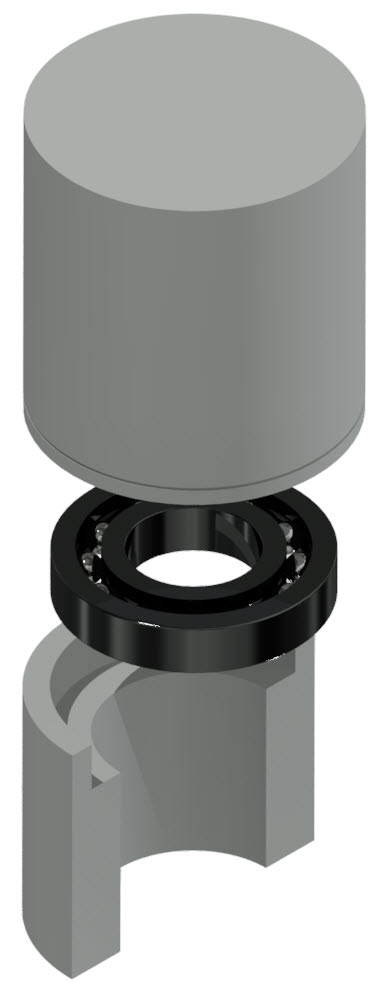
When assembling parts which rely on bushings and bearings, there are several key points to consider in order to ensure that you and your customers are getting the quality you both demand. In today’s competitive marketplace, if you can’t, or simply won’t meet your customer’s demand for high quality, there are countless others ready to step in and take your place! So, how do you ensure that your customer is getting what they need in order to be successful, thereby ensuring your own success? And perhaps more importantly, how do you guarantee it? In order to achieve a higher standard, nearing perfection, a few key things must first be put in place:
- Your process and equipment must be capable of the required force and precision.
- It must be intelligent enough to distinguish between a “good” and a “bad” assembly.
- And it must be flexible enough to respond to the circumstances and ensure that “bad” assemblies are not produced in the first place.
Two Factors When Pressing in a Bushing or Bearing
Generally speaking, there are two primary factors which come into play when pressing in a bushing or bearing: force and position. And there are many other secondary factors which can affect these first two, including part variation, ambient temperatures, and other materials which may be present, from oils and grease to dust and gritty powders, to name just a few.
Certainly, older systems, using yesterday’s hydraulic and pneumatic technologies, can achieve the force required, as their decades of use has proven, but they fall short when it comes to precision, intelligence, and flexibility. In order to overcome the countless mitigating factors which can negatively affect your outcomes, while returning consistently accurate and precise data, among the best options available, is an electrically powered, servo-driven ball screw press with load cells.
Saving Energy TODAY Will Make TOMORROW Bright
The advantages of electric power are numerous and include the facts that electric power is readily available, relatively clean and cheap, capable of being easily and efficiently transmitted, and primarily, electric power can be easily controlled and monitored. A servomotor, which is really any suitable motor coupled to another device (such as an encoder) that can return speed and position feedback, provides several advantages as well. Most notably, the feedback from the servomotor can be used for precise position and speed control. Along with the servomotor, use of a ball-screw provides for an additional level of precision. A ball-screw, which is typically made to very close tolerances, is a low friction linear actuator which efficiently converts the motors rotational motion into linear motion. Ball-screws are also typically very durable and have a long working life. Finally, the load cell, especially when paired with the right software, provides many benefits.
Load Cells
Load cells commonly used in industrial applications can be one of a few different kinds. Typically, the best and most reliable systems use strain gauge load cells, piezoelectric load cells, or some combination of the two. Strain gauge load cells are particularly well suited to industry, in part, because of their reliability and long life even in high cycle applications. When force is applied, the strain gauge, a planar resistor, is deformed slightly.
This deformation proportionally affects the resistance of the strain gauge, which, in turn, provides a consistent and measurable change which can be calibrated to the load that is being applied. Once properly calibrated, strain gauge load cells are known for their consistence and reliability.
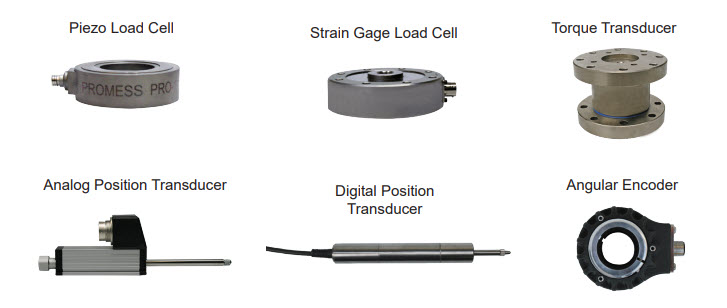
Piezoelectric sensors, sometimes added externally to increase precision, use the piezoelectric effect to output a voltage when pressure, or force, is applied. In fact, the prefix “piezo-“ comes from the Greek word meaning “to press, or squeeze.” And since the output voltage is linear and proportional to the input force, converting from one to the other is not only easy, but can be done very accurately as well.
Like the ball-screw, strain gauge load cells and piezoelectric sensors tend to be very durable and can withstand, and operate in, even harsh industrial environments.
But, having all of the components mentioned so far, as important as they are, is still only a fraction of the whole equation. If your system doesn’t have the intelligence to make all of these components interact to produce the outcomes you require, you’re not likely to get very far. The software that runs your operation is what provides the necessary intelligence. If your software is too difficult to understand, and if it doesn’t return the data you need in the form that you need it, you are setting yourself up to fail. If your software is not robust enough to accommodate your wide variety of needs, you are setting yourself up to fail. And if your software is not flexible enough to quickly change as your, and your customers’ needs change, you are setting yourself up to fail. But, when the software you are running on your system is intelligent, robust and flexible, you are ensuring your, and your customers’ success.
Oftentimes, the final piece in the puzzle does not even make itself known until after the fact: after the equipment is purchased and in use, after the training is complete… And this final component, which may turn out in the long run to be the most critical one of all, is service and support. There are a lot of companies out there that will sell you their products, and even provide some training on them, but then leave you high and dry once payment is received, so they can go on to pursue the next quick buck. Some of these companies may even have the lowest initial costs, but fortunately, most intelligent and forward-thinking engineers, as well as others across the manufacturing spectrum, have gotten wise to this. You don’t have to get burned too many times before realizing that cheap initial costs from a company that does not stand behind its products with world-class service and support, when you need it, will only cost you more over time.
Once you have established that all of the basic system requirements to get the job done are in place, much of the rest of the work required for setting up is just finding and plugging in the numbers. Manually jogging your press ram down to a point just above your part will give you your first positioning move. In order to maximize your overall process speed and efficiency, this step, in your actual manufacturing process, can usually be done more quickly, since no “work” is being done. After this initial position is reached, the press is slowed to the speed that is most suitable for your application, and your software can begin monitoring the force and position more actively. Graphic data can also be returned and viewed almost instantly so you can see your results, verified, in real time. The data is then also gauged to determine quality and ultimately, it can be fed back into the system to guarantee a perfect bushing, or bearing assembly, every time. Even after your process is completed and verified, the data collected, whether simple values along the way or complex graphs and gauging data, can be stored as a record of the work done, and as further verification and proof that your bushings and/or bearings have been assembled to within acceptable levels of the rigorous specifications you and your customers demand.
Capable, and proven hardware, such as Electro-Mechanical Servo-Driven presses, paired with smart, responsive and intelligent software, is the best solution to consistently guarantee that you and your customers continue on the path to overall success.