The real question is, if 100% in-process verification of quality could help you more consistently achieve higher quality, why aren’t you doing it already?
Too many manufacturers rely solely on statistical testing to verify product quality; at best they test random samples. They assume since their samples are all in spec, then everything else should be too. Some Manufactures have more robust end-of-line inspection, which are a bit more reliable, but it only catches a problem after the part has been poorly produced. This usually results in higher rates of scrap.
If there was a way you could easily and reliably test for product quality, in-process, where the problem could still be rectified without having to scrap the part, you’d do it, right? And if there was a way to achieve 100% in-process quality verification, you’d certainly jump all over that.
With today’s manufacturing technology and innovative engineering it’s already being done by the most successful and prominent manufacturers in the world.
Sample Application: Simple Press-Fit Operation with an EMAP System
Process
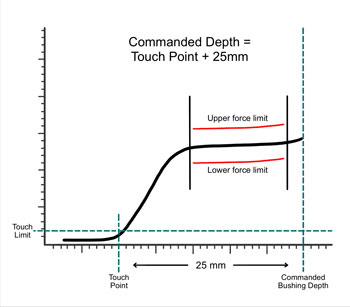
- Parts are loaded into the fixture (in this case, a bushing being pressed into a bore). Prior testing determines a good press-fit occurs with 12kN of force and bushing is properly positioned when it has been moved 25mm past the touchpoint but not so far that it has bottomed out
- Operator inputs part-present sensors or any of several other devices potentially used to initiate the process.
- Process initiated
- EMAP ram extends at a fully-programmable, appropriate speed until it makes contact with the part, the touchpoint. The systems built-in force transducer recognizes the touchpoint
- The EMAP continues to press the bushing to a location 25mm from this touchpoint, and the ram retracts. The RAM captured both the final position AND the force, throughout the work that has been done
- The captured data is graphed, displayed and gaged against a known or “taught” ideal part, +/- the amount of variance you have determined is acceptable
- The assembly is assigned pass or fail status
Results
This process, using an EMAP press, produces results that are 100% verified, in process, before the assembly ever leaves the station. The manufacturer receives immediate data on the process, giving you the power to decide, intelligently, how to best proceed.
What Does This Mean for You?
With today’s technology and innovation, backed by support available 24/7/365, there is a way to achieve 100% in-process quality verification. You can ensure every assembly you produce meets or exceeds your customers’ expectations while minimizing scrap and/or waste.
Knowledge is power, and with the data produced by a Promess system as it delivers accurate and repeatable, programmable force, position & torque, you have the power to supply your customers with the best products, consistently and reliably.
The real question is not merely how to achieve 100% in-process quality verification; we’ve got that figured out already.