In the world of automotive manufacturing, precision and reliability are critical. Universal joints, which connect the driveshaft to the differential and allow it to transmit power through variable angles, are crucial components that must meet exacting standards. One of the most challenging aspects of assembling universal joints is ensuring the floating spider mechanism remains precisely centered during the insertion and staking of bearing cups. Here’s how the innovative use of dual Electro-Mechanical Assembly Presses (EMAP) from Promess transformed this critical aspect of the assembly process.
The Challenge: Maintaining Perfect Spider Alignment
In the assembly of universal joints, the floating spider can shift during the insertion of bearing cups and staking, causing misalignment and potentially leading to functional issues or part failure. Ensuring the spider remains exactly centered is crucial for the joint’s performance and longevity. The challenge was to develop a method that could reliably maintain the spider’s position at the center of the universal joint throughout the assembly process.
The Solution: Dual EMAPs for Simultaneous Pressing
To tackle this challenge, the manufacturer implemented a dual approach using two Promess Electro-Mechanical Assembly Presses (EMAP). This innovative method involved inserting and staking the bearing cups from both sides simultaneously, ensuring the spider remained centered throughout the process. Here’s a closer look at how it worked:
- Simultaneous Bearing Cup Insertion:
- Two EMAPs were used to insert the bearing cups simultaneously from both sides of the universal joint.
- This simultaneous action ensured equal force was applied to both sides, preventing the spider from shifting.
- External Feedback Sensors:
- The system employed external feedback sensors to accurately detect the spider’s position and confirm it was centered.
- Real-time data from these sensors allowed for precise adjustments during assembly, ensuring the spider remained in the correct location.
- Coordinated Pressing and Staking:
- Both EMAPs worked together at the same speed and applied uniform force, maintaining the spider’s centered position.
- This coordination ensured that when the staking process began, the spider was securely and accurately positioned.
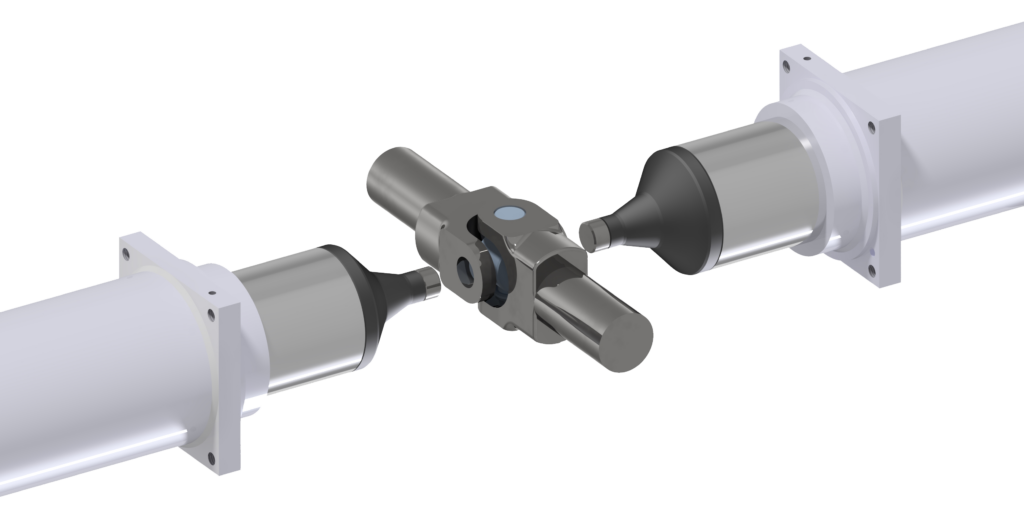
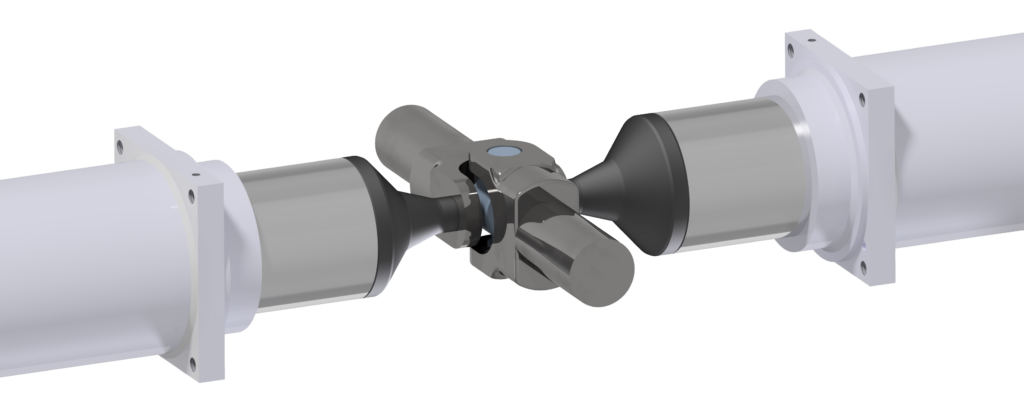
The Results: Superior Quality and Efficiency
The adoption of the dual EMAP approach yielded significant benefits for the universal joint assembly process:
Accurate Spider Positioning:
The dual EMAPs ensured the floating spider remained precisely centered, eliminating misalignment issues and improving the joint’s overall quality.
Consistent Assembly Outcomes:
The use of feedback sensors and synchronized presses provided consistent and repeatable results, reducing the likelihood of defects and enhancing product reliability.
Streamlined Production:
The integrated dual EMAP setup simplified the assembly process, increasing efficiency and throughput while reducing production costs.
Reduced Defects:
Accurate centering of the spider led to a lower defect rate, minimizing rework and enhancing customer satisfaction.
Enhanced Product Performance:
By maintaining precise alignment, the universal joints demonstrated improved performance and durability, leading to better overall vehicle reliability.
A Leap Forward in Universal Joint Assembly
The innovative use of dual EMAPs for simultaneous pressing and staking of bearing cups in universal joints has revolutionized the assembly process. By ensuring the floating spider remains perfectly centered, this approach has significantly improved the quality and efficiency of the assembly, resulting in more reliable and durable products. For manufacturers facing similar challenges, adopting advanced assembly technologies like dual EMAPs can lead to significant improvements in product quality and production efficiency, underscoring the value of precision in manufacturing.
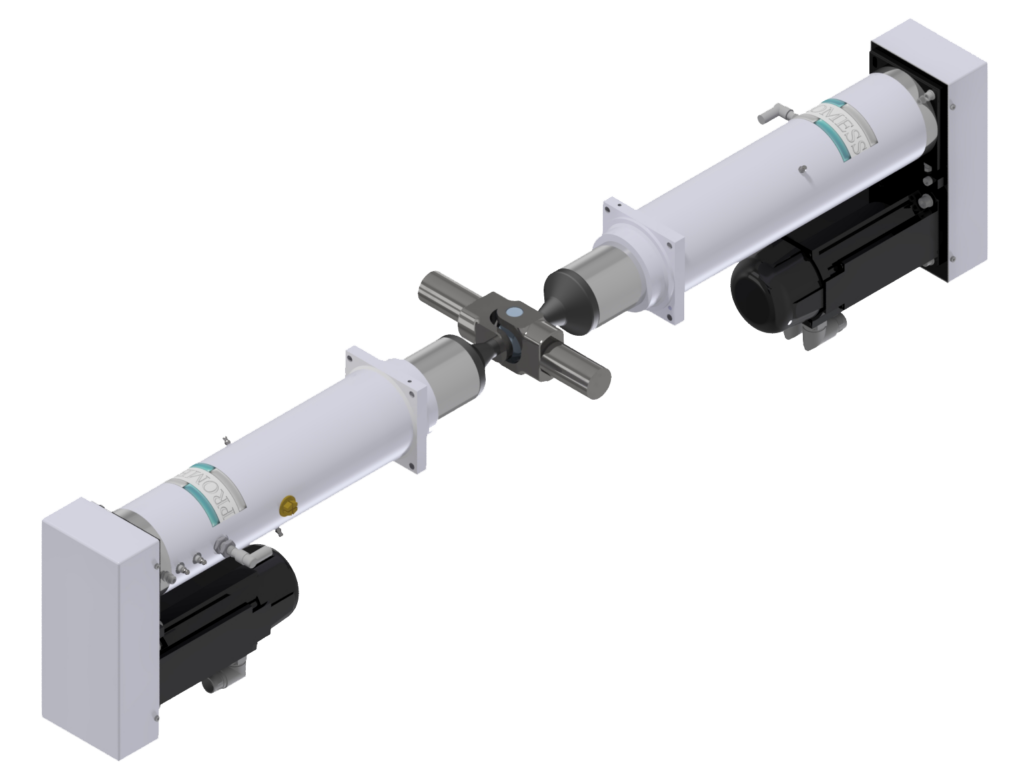