Case Study #1535 | EMAP
WATER PUMP ASSEMBLY
Challenge

In the assembly and manufacturing of automotive water pumps, there are various components that need to be pressed to a dimension relative to a machined surface on the pump housing, and not to a shoulder. This is important for proper pump flow and belt alignment These assemblies include the bearing pack, the impeller, and the hub.
Assembly Options
Traditionally, there have been two ways to assemble a water pump:
- Use a hydraulic press with fixed tooling and hard stops
- Problem – the tolerances of the parts are greater than the required assembled tolerances, so hydraulics cannot be used
- Use a servo controlled press and premature the parts in the station before the press station, then feed this offset to the press. The parts are then pressed together and the critical dimension is measured in the third station, after the press.
- Problem 1 – eats up valuable floor space and adds additional cost to the machine by having two gauging stations
- Problem 2 – the press cannot compensate for variations at the press station. These include: pallet height variations, machine deflection, load cell deflection and part spring back, which all vary with the load needed to assemble the part. These variations use up 50% or more of the tolerance.
Solution
The Promess Electro-Mechanical Assembly Press (EMAP), is a closed loop, servo controlled, ball screw press system. An external position transducer was integrated into the press tooling to measure the critical dimension of the assembly. The output from the position transducer is fed directly into the Promess motion controller. Utilizing the Measure function, a master part is used to master the external position transducer (establish the zero point). The system will then try to press to this position every time.
Process
- During the assembly of the water pump, the components are pressed just short of the desired position.
- The Measure step then reads the deviation, or offset, from the master and the press moves that exact amount.
- Then it rechecks the offset and verifies that is within the acceptable plus/minus part tolerances, if not, the press will adjust again.
- The EMAP then gauges the part and stores the value into a gauge table.
Every part is pressed to tolerance and gauged all in one station. The force versus position signature is also monitored to ensure that the part has the correct interference fit.
The bearing pack must be pressed to within a tolerance of ± 0.2mm. The external position transducer with the Measure function is used to achieve a tolerance of ±0.03mm. The variations from pallet to pallet can be as great as ±0.05mm. Part and machine deflection can vary as much as ±0.12mm depending on load. The Measure function compensates for all those variations in the press station.
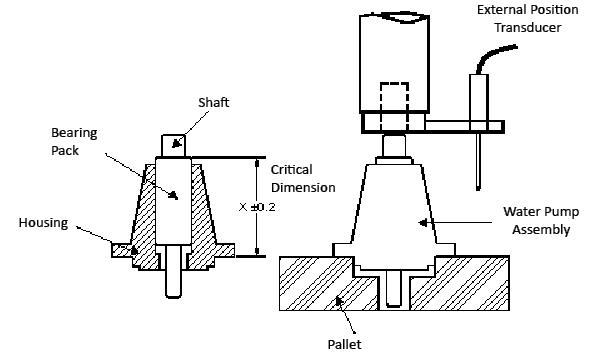
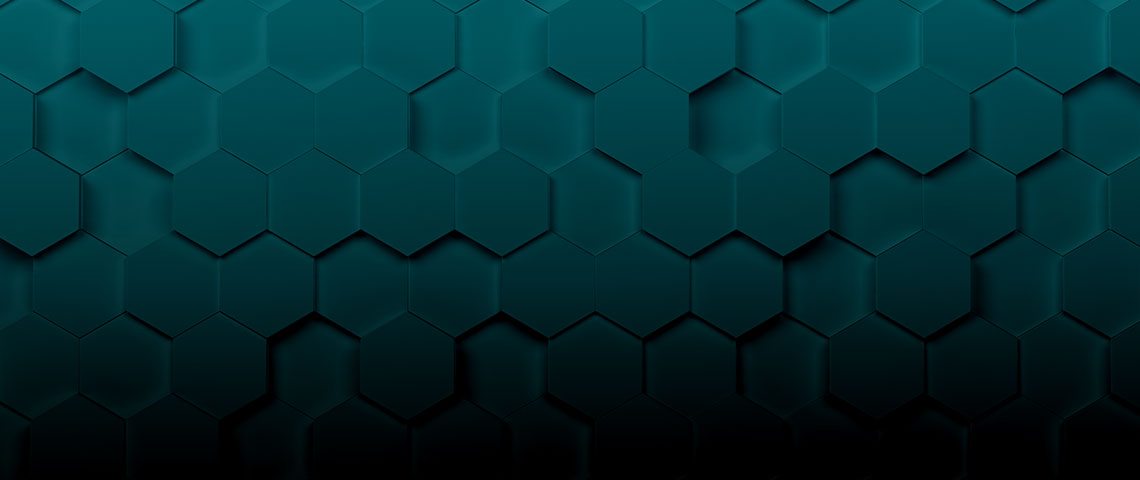
Do You Have an Application?
Talk to one of our expert engineers or learn more about proving your
application in our Process Development Center.