Case Study #1865 | EMAP
BATTERY ASSEMBLY
Challenge
Customer was looking for a turnkey assembly cells that had flexibility, data storage and management, but more importantly, a system that could provide accuracy to the battery manufacturing process.
Solution
Promess provided a turnkey battery assembly Work Station, using the UltraPRO platform as the base control, and coupling that with the our Electro-Mechanical Assembly Press (EMAP). This gave the customer the ability to control their process and provide flexibility to the continuing evolution of battery development and assembly.
This included the EMAP, with precision matched frame and base, Promess platen technology along with a fully functional electrical and safety enclosure. Force and position feedback integrated into the system allow each battery assembly to be assembled identical to the next, with data to prove it.
Using precise motion control and industry leading software, the system can easily, reliably and efficiently assemble automotive battery components from powder compaction, laminate stacking to case assembly. Force and position feedback integrated into the system allow each battery assembly to be assembled identical to the next, with data to prove it.
With the constant evolution of battery technology, the assembly process can now evolve alongside the products technology, giving the end user a flexible and infinitely programmable turnkey Work Station solution, while also simplifying complexity and making quality parts each and every cycle.
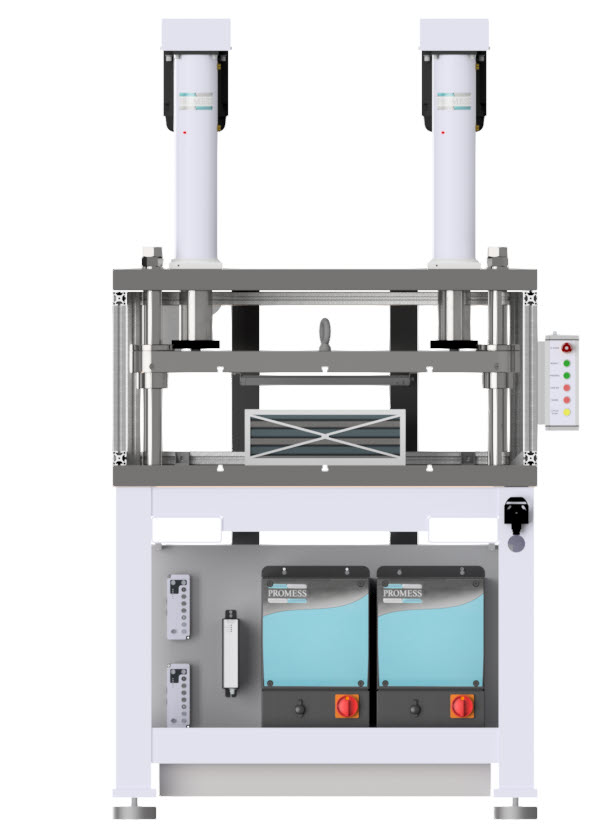
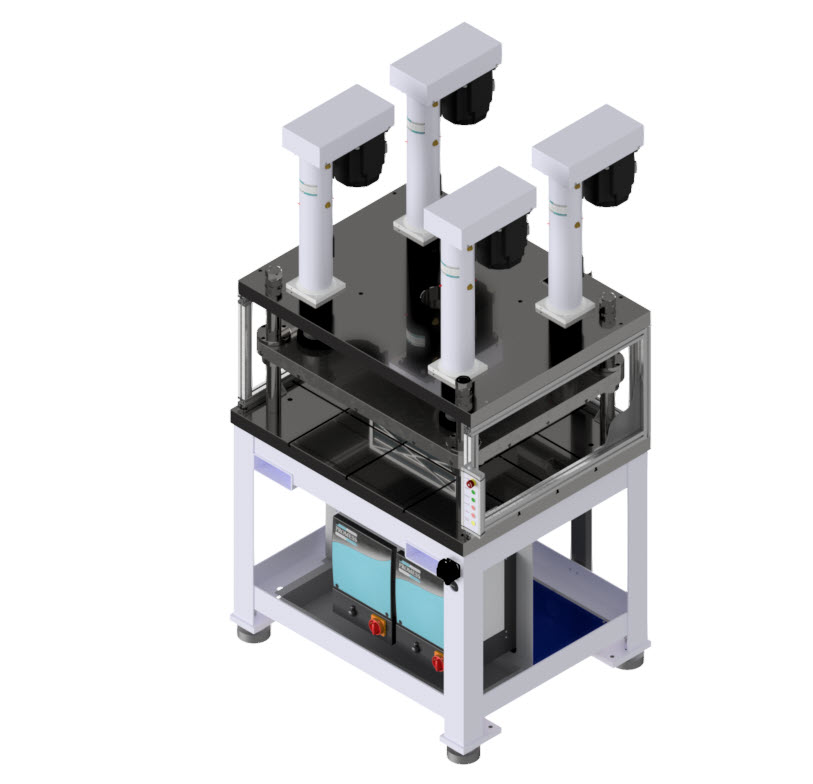
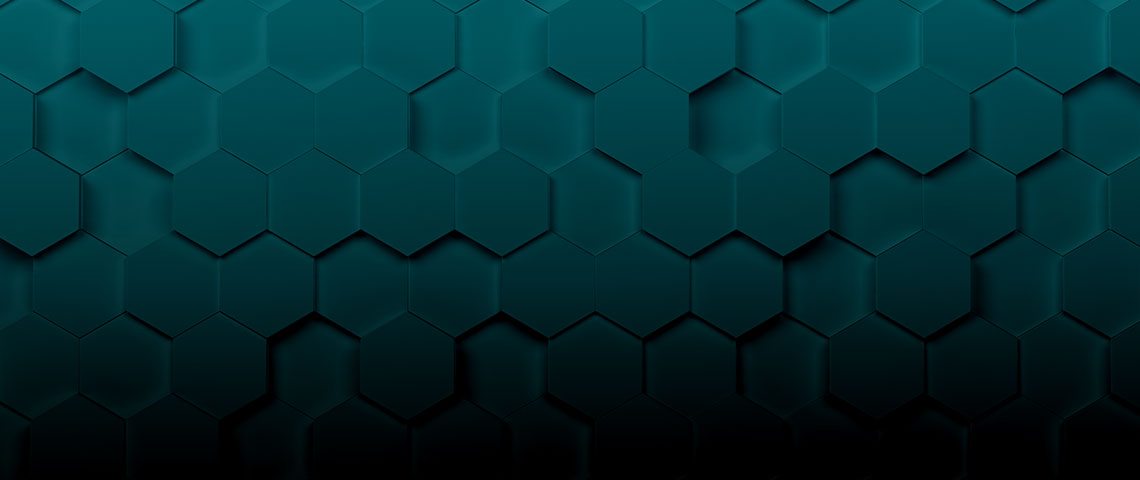
Do You Have an Application?
Talk to one of our expert engineers or learn more about proving your
application in our Process Development Center.