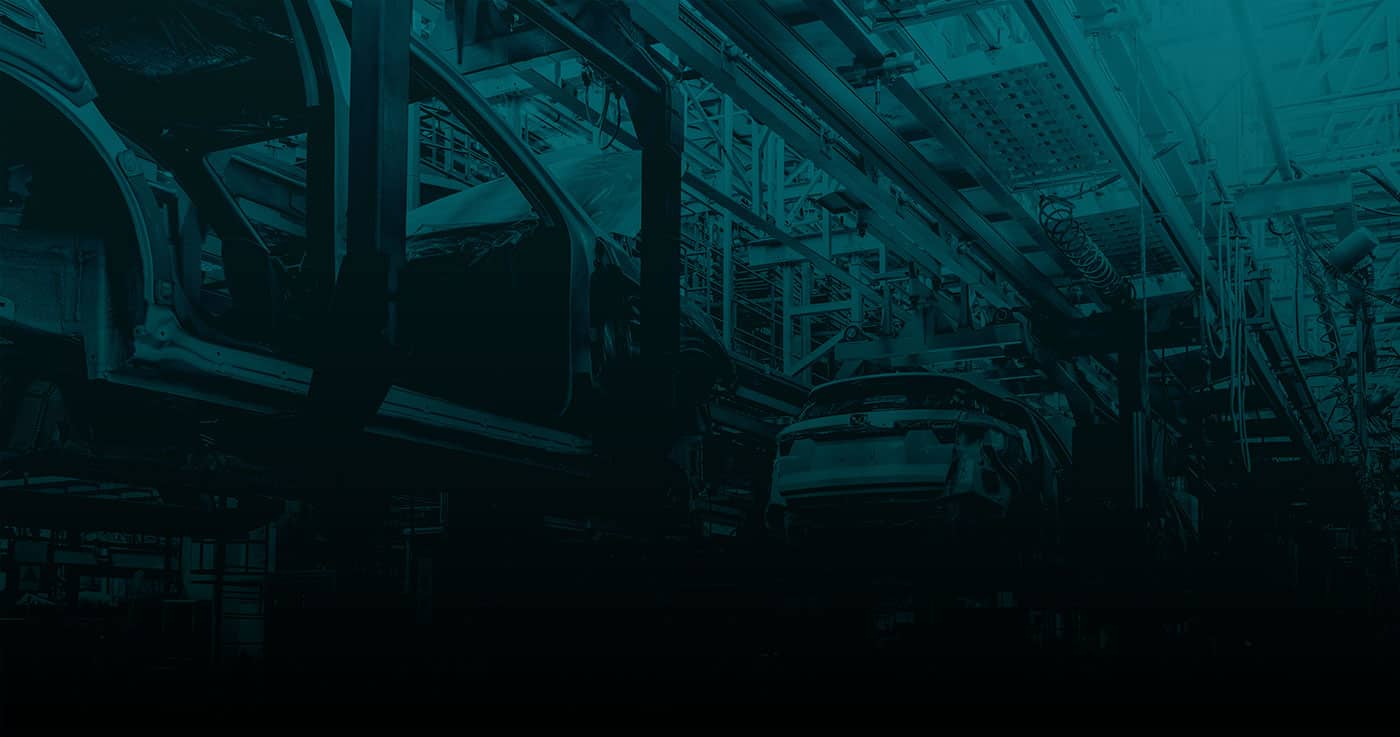
Application:
Powder Compaction
Complete solution utilizing standard Promess technology, packaged for Powder Compaction Application.
Application: Powder Compaction
As the demand for more precision and tighter tolerance increase, Promess now offers a complete solution for powder compaction. This comprehensive solution for powder compaction combines integrated motion control and safety with advanced sensing technology, resulting in improved quality and enhanced data analysis capabilities.
The UltraPRO software provides operators with real-time monitoring and data analysis capabilities, allowing them to identify and address issues quickly and effectively. It includes a range of tools for data acquisition, visualization, and analysis, as well as customizable reporting functionalities that support process optimization and documentation.
The intelligent sensors offer advanced sensing capabilities that enable operators to monitor process variables such as force, displacement, and temperature in real time. This data can be used to identify trends, detect anomalies, and optimize process parameters to ensure maximum efficiency and quality.
Benefits
Precise control over the compaction process, ensuring consistent quality and reducing the risk of defects or errors. Included safety functions such as emergency stop and overload protection, as well as advanced motion control capabilities that enable precise positioning during the compaction cycle. Allowing you to make the perfect part every time.
Application
Compression Molding, Powder Compaction, Powdered Metals, Plastic Materials
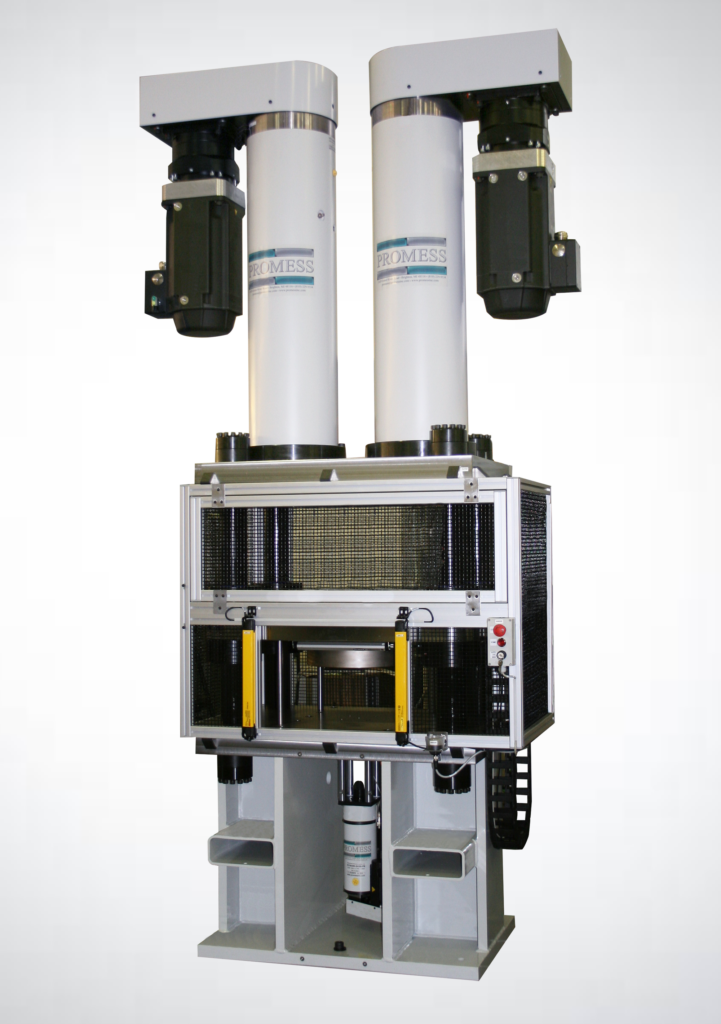
Powder Compaction Press Features
- Data acquisition and storage
- In-process verification
- Real-time monitoring
- Data analysis
- Integrated load cell
- Electric Servo Press
- Platen
- Work Station
Watch the video to see the process for a powder compaction application.
Case Study: Compression Powder
The most common assembly process for composite parts is compression molding. Material is inserted between coordinated metal dies and then pressed together under a high amount of force.
The customer was previously using hydraulic presses and running into issues with inconsistent parts. The customer needed to be able to monitor the force and position throughout the process…
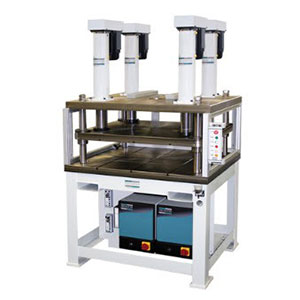
What is your application?
Talk to one of our expert engineers or learn more about proving your
application in our Process Development Center.