Case Study #1860 | TorquePRO
Gear Backlash Testing
CHALLENGE
Controlling for backlash in the assembly of gear systems is a challenging process. Manufacturers have often had to go out of their way, spending exorbitantly in order to ensure incredibly precise dimensions, and still failing to produce the most efficient systems of gears.
The amount of backlash in your gearsets is, no doubt, a critical dimension that will directly affect performance. Too much backlash, and gearsets are noisy, inefficient, and may experience premature failure from the damage caused by too much “play” in the gear system. Not enough backlash, and gearsets jam, efficiency is sacrificed, and gears are almost certainly subjected to excessive wear & premature failure.
Testing for and controlling backlash in the gearset assembly process, while problems can still be addressed, is critical for properly functioning gearsets which lead to successful outcomes for you and your customer.
SOLUTION
Promess’ Gear Backlash Test System facilitates a series of tests that simulate product function and assess performance.
There are two types of Backlash Testing: Static & Dynamic
With Static Backlash Testing, the output gear (final driving gear) is held in a fixed position and torque is applied in both directions to the input gear (driving gear). Position values are captured and stored. The difference in position between the two directions is the static backlash at that gear mesh point. This test is typically done at several gear mesh points throughout the gears’ rotation.
Additional tests, such as torque-to-turn testing, can also be performed by the Promess Gear Backlash Test System, to determine the best location for additional static testing.
With Dynamic Backlash Testing, the gear assembly is rotated to incorporate all the gear-tooth combinations. All position values are captured, stored, and plotted, and compared to their corresponding positions in the opposite direction to find the largest & smallest significant differences, and any other differences that may contribute to the gear system’s function.
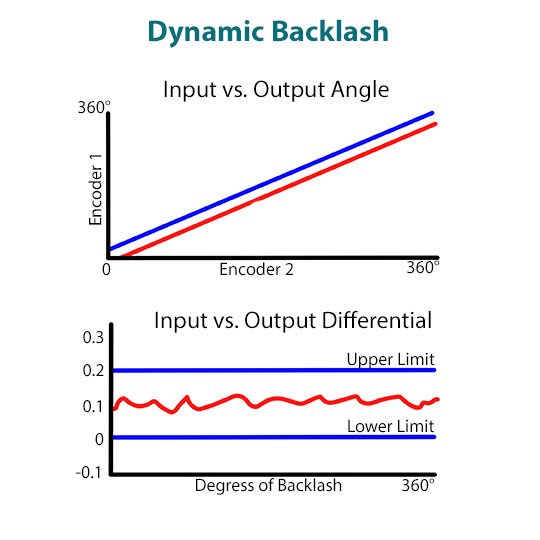
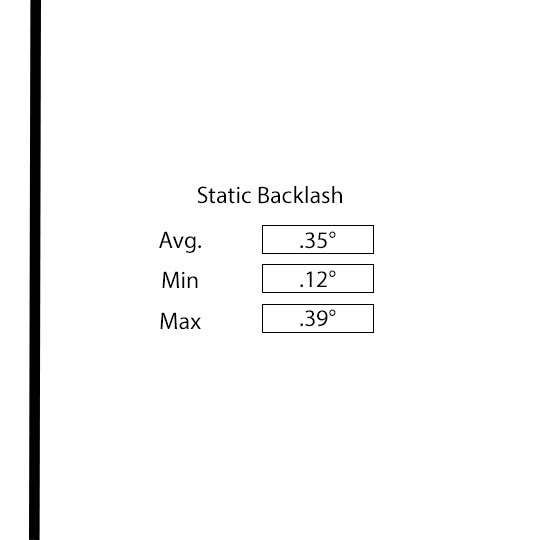
RESULTS
Using Promess’ TorquePRO-based Gear Backlash Testing System, the manufacturer was able to identify and correct problems, improve their processes going forward, and ensure that every gear system they produced would function as it should, providing efficiency and long life for their end-users.
Good gear systems were verified; problematic systems were removed and/or repaired; and, with the data, and the knowledge, they had obtained, many problems were able to be prevented from occurring repeatedly in the future.
Both the gear manufacturer and the end-user of the gears were positioned that much closer to continuing and increasing success.
Controlling Backlash in Your Gear Assembly Process Yields Higher Efficiency, Longer Life, and All-Around Better Results for You and Your Customer.