Case Study #1925 | ROBOT PRESS
CUP PLUG ASSEMBLY
CHALLENGE
A customer working on large scale engine needed to update their old process of hammering in cup plugs by hand to an automated assembly line. They were previously using an air/pneumatic hammer operated by a human. This process created excessive noise pollution, multiple pinch points and some serious safety concerns to the operator. In addition, this old process didn’t provide in-process quality verification, and this was a requirement for our customer. Along with the automation of their cup plug process our customer needed a way to detach the robot from the electric press so that it could continue through the other operations cycles on this assembly line without halting the process.
SOLUTION
The Promess solution for this cup plug application utilized the Promess Robot Press with our quick connect/disconnect capability. This solution allowed our customer to remove their operator from the assembly process and full automate their assembly line.
This tailored solution required a 6-axis robot to handle the payload for this engine application. The quick connect/disconnect feature allows the robot to drop off the press and cut the cables from the robot without faulting the process. In addition, this process is repeatable without the need to cycle power. Like all Promess systems, the Promess Controller was also utilized to give in-process quality verification and data acquisition.
Results:
Our customer was able to automate their manual process, eliminating the need for an operator at the station and the noise pollution of their previous process. Our customer was also able to provide a safe work environment for their employees by removing the hammering process. The Promess Controller provided the ability to make commands with high accuracy, and the customer without buying new equipment. Our customer was able to take a previously very manual process and transform it into a fully flexible and completely automated process.
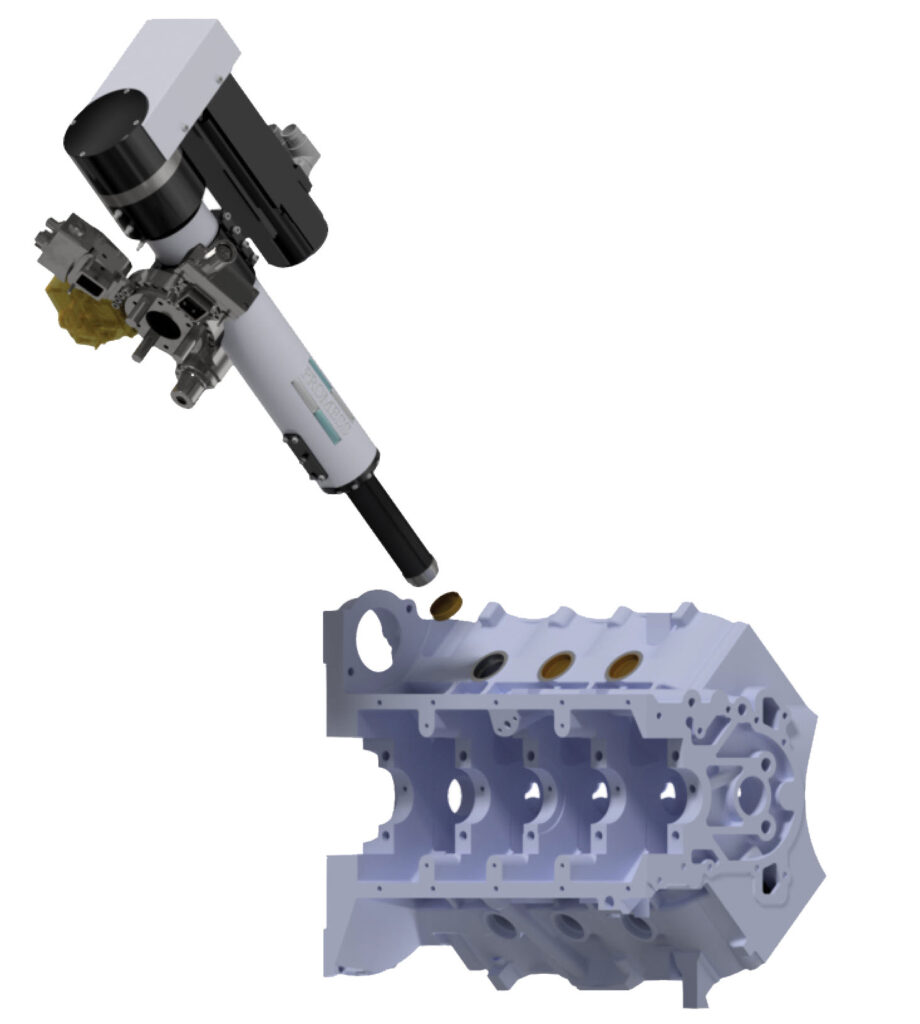
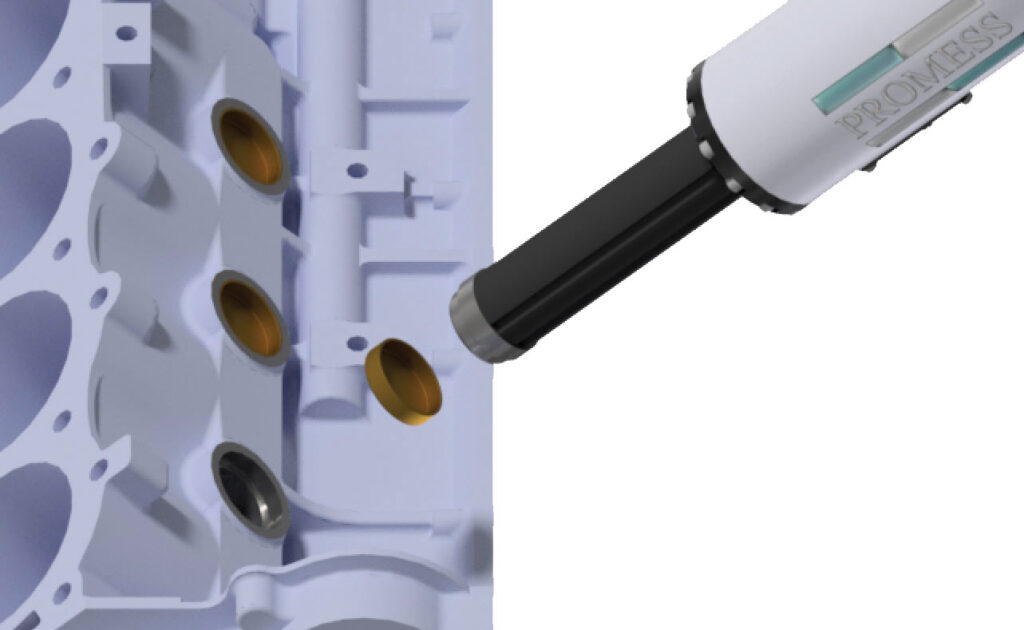