Case Study #1930| HAND HELD PRESS
ROLL PIN PRESS
CHALLENGE
A major automotive manufacturer came to Promess with an issue; a small roll pin that holds a crucial component together in a drivetrain was falling out. This issue was happening out in the field during operation of the vehicle. This was not only causing potential catastrophic failure to the drivetrain, but also was a safety concern. The current technology for this process utilized pneumatic technology without motion control or force and distance monitoring. So, the manufacturer had no way to understand the assembly was being pressed to the correct force or distance.
Because of the nature of how a roll pin is manufactured, it can vary in diameter causing the press fit to be ‘too loose’ or ‘too tight’. If too tight, the pin would not be pressed all the way causing interference with other components in the assembly and if too loose it can fall out. Based off the physical location and the small nature of the part, a small press with force/distance monitoring and control that could be manually handled by an operator would be needed to get into this tight space. Unfortunately, this technology did not exist in marketplace.
SOLUTION
In typical fashion, the Promess Engineering team put together a solution and created what is now widely known as the Promess Hand Held Press! The Promess Hand Held press is a fully electric handheld servo press that includes built in force & distance sensing.
Its lightweight design along with configurable handle designs allows the user to physically hold the press, articulate into position and pull the triggers to actuate the press cycle.
Utilizing the Promess UltraPRO platform, gives the user simple and easy integration, yet powerful sensing and motion capabilities.
Results:
Working with Promess application engineers, the user was able to integrate the Promess Hand Held Press into the station and create programs that offered precise force and distance control. This allowed each press cycle to very accurately control where the roll pin was pressed to and that enough force was not going to fall out. In addition, the UltraPRO controller captured, saved, and linked with the customers plant system. This gave the manufacturer historical proof that the press process was done correctly every time.
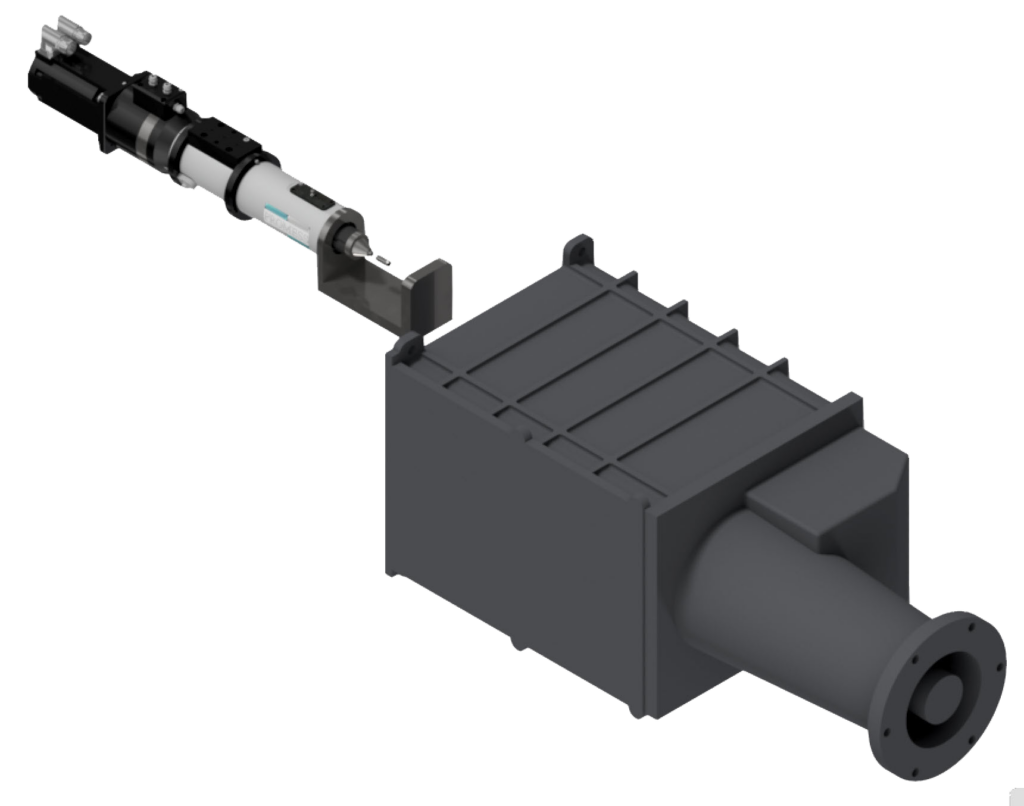
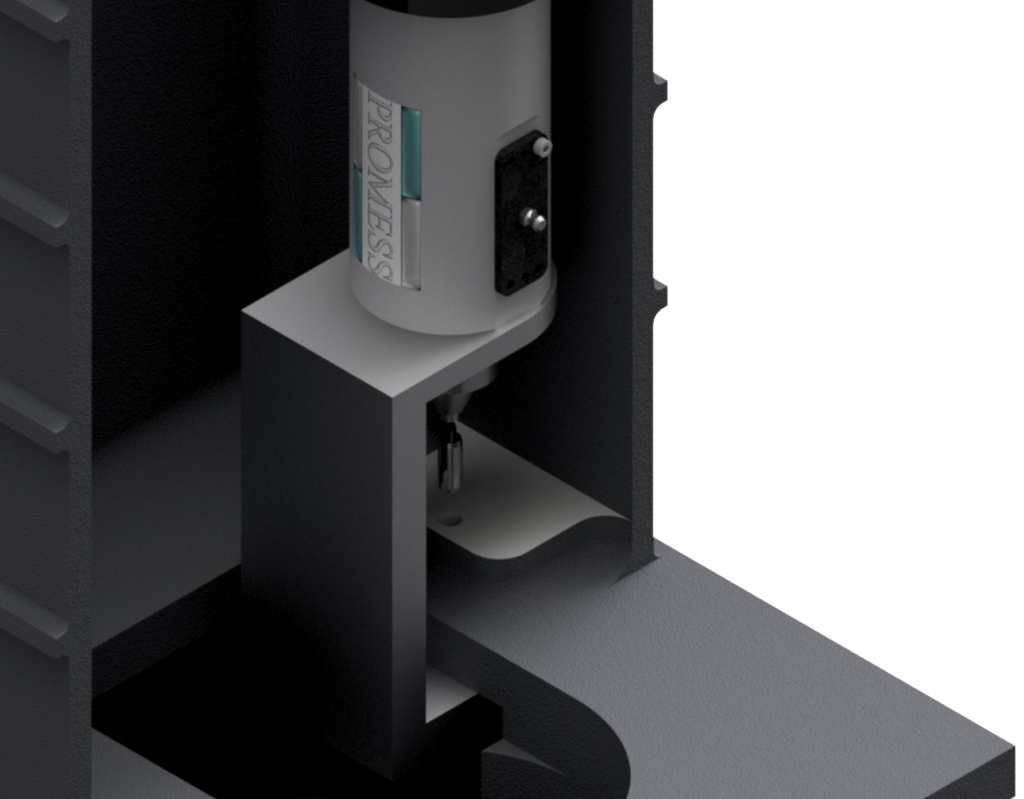